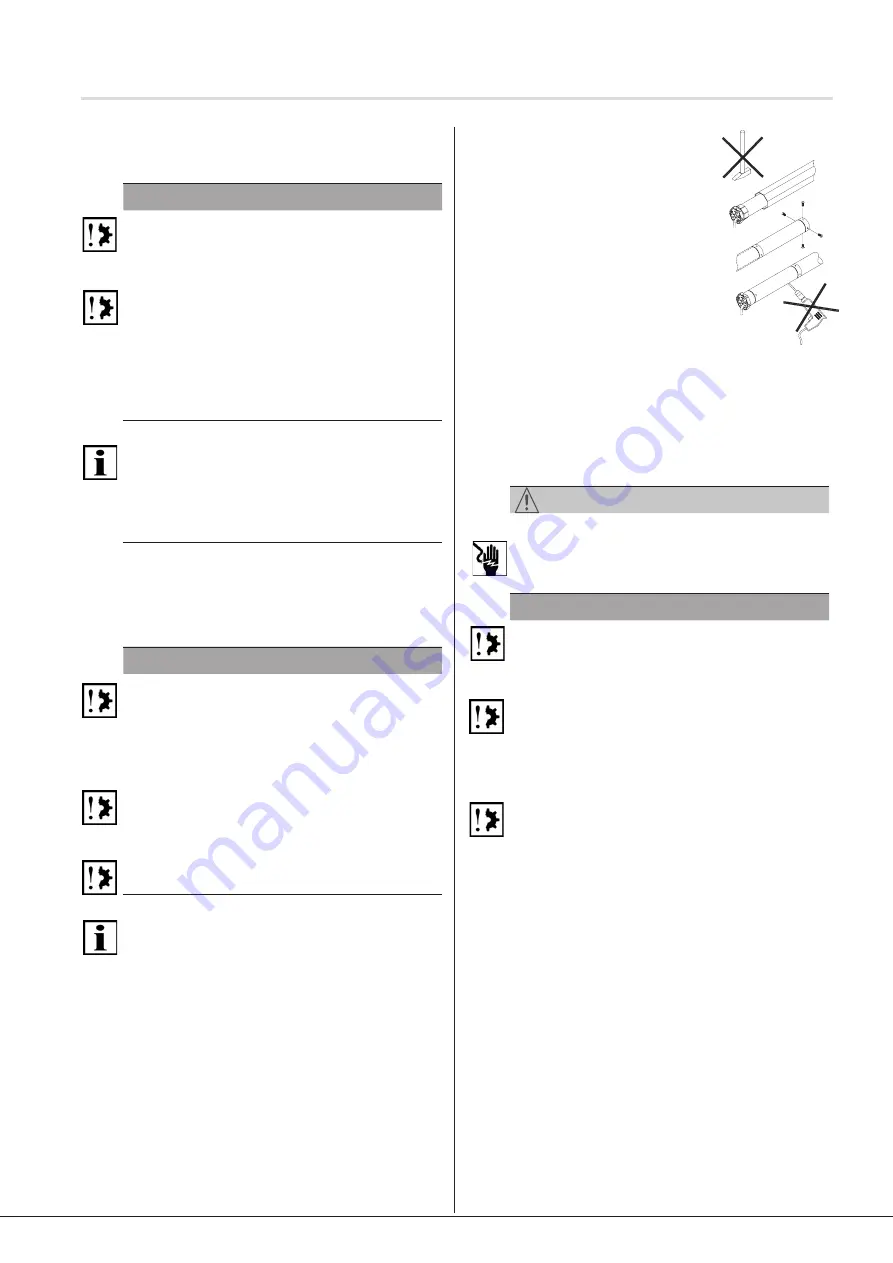
Installation in profile tubes
Ⓐ
Push drive with relevant adapter and
crown into the profile tube.
Install the motor cable so it is protected
to prevent damage from the driven
part.
Ⓑ
Secure the counterpart support to
prevent axial movement, e.g. screw
or rivet on the idler. Secure the drive
axially in the support!
ⒸAttach the blind to the shaft.
The drive is fastened on the wall anchor and the blind
mounted on the shaft using the suitable motor bearings and
adapter components according to building requirements
and, depending on the type of blind, with suitable connection
elements, also provided by the system supplier.
Only operate the drive horizontally, as intended, with the
connection cable leading out from the side and away from the
slat movement area.
5.2 Electrical connection
WARNING
Faulty electrical connections constitute a fatal hazard.
Risk of electric shock.
►
Prior to initial commissioning, check the PE wire is correctly
connected.
ATTENTION
Damage to the InDrive M30/1.6 RH due to incorrect electrical
connection.
►
Prior to initial commissioning, check the PE wire is correctly
connected.
Damage to or destruction of the InDrive M30/1.6 RH due to
the penetration of moisture.
►
For devices with protection class IP 44, the customer-side
connection of the cable ends or plugs (cable feed-through)
can also be implemented according to protection class
IP 44.
Damage to or destruction of the InDrive M30/1.6 RH for
variants with 230 V 1 AC due to incorrect activation.
►
Switches for drives that are set to OFF by default (dead-
man's switches) are to be installed within visible range of the
InDrive M30/1.6 RH, but away from moving parts and at a
height of more than 1.5 m.
4 | EN
©
elero
GmbH
Assembly (electrical connection)
Drive is overwound and may destroy parts of the application.
►
For safe operation, the end positions must be set/taught in.
►
Manufacturer training is available for specialist companies.
ATTENTION
Power failures, breaking of machine parts and other
malfunctions.
►
For safe operation, assembly must be correct and the end
positions must be configured upon commissioning.
Damage to InDrive M30/1.6 RH due to the penetration of
moisture.
►
On devices with protection class IP 44, the ends of all
cables or plugs will need to be protected from ingress of
moisture. This measure must be implemented immediately
after removing the InDrive M30/1.6 RH from the original
packaging.
►
The drive must be installed so that it cannot get wet.
Important
In its delivery state (factory setting), the InDrive M30/1.6 RH
will be in commissioning mode.
►The end positions will need to be configured
(see section 5.6).
5.1 Mechanical fastening
Important preliminary consideration:
The working area around the installed drive is usually very
small. For this reason, obtain an overview of how the electrical
connection has been implemented prior to the mechanical
installation (see section 5.2) and make the necessary changes
beforehand.
ATTENTION
Crushing or tension will damage the electrical cables.
►
Install all electrical cabling so that it is not subject to any
crushing or tensile load
►
Observe the bending radii of cables (at minimum 50 mm).
►
Route connecting cables in a downward loop to prevent
water running into the drive.
Damage to the drive due to the effect of impact forces.
►
Slide the drive into the shaft. Never knock the drive in or use
force!
►
Take care not to drop the drive!
Damage or destruction to the drive by drilling.
►
Never drill the drive!
Important
Only secure the InDrive M30/1.6 RH using the fastening
elements provided for this purpose.
Fixed installed control devices need to be attached so they are
visible.
•
The profile tube must have sufficient clearance from the
motor tube.
•
Make sure there is sufficient axial play (1 - 2 mm)