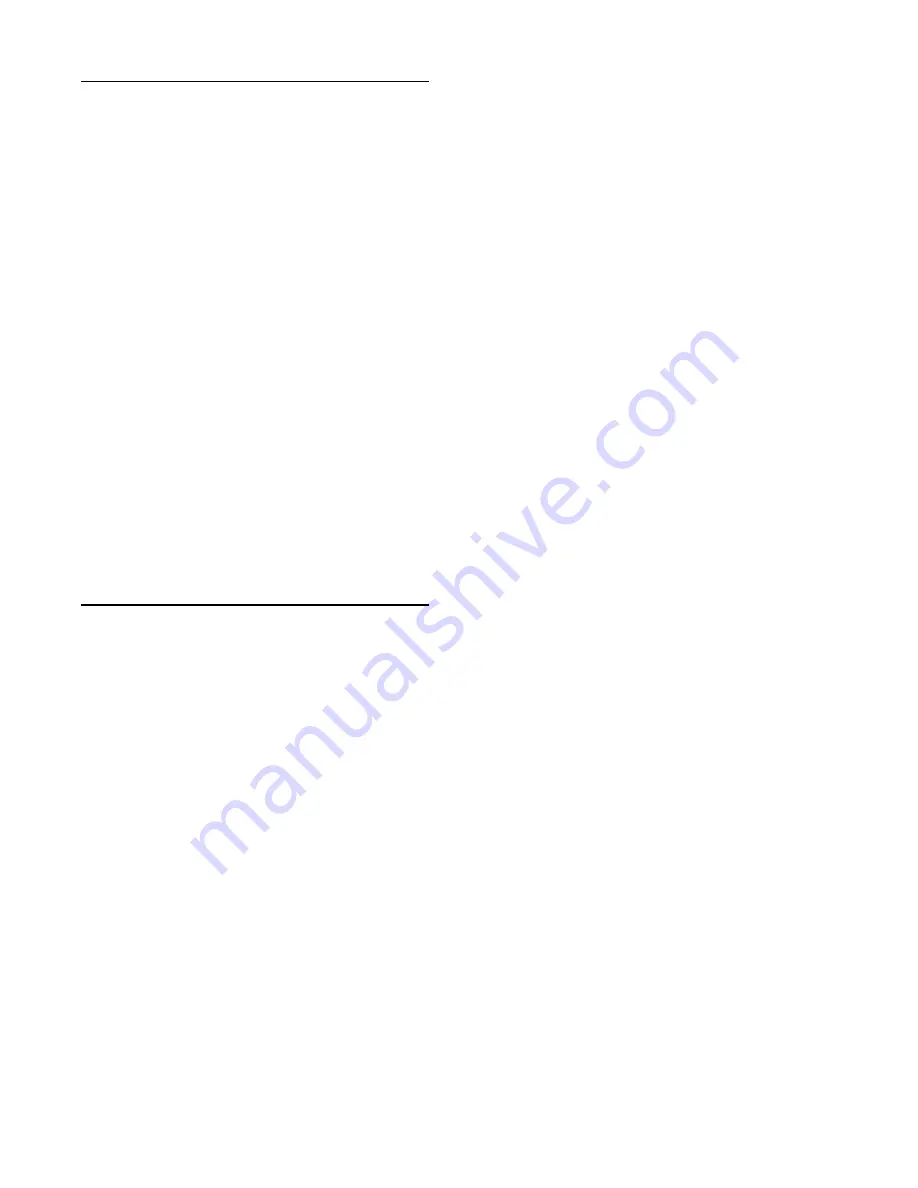
1 - 1 6
1 - 1 6
1 - 1 6
1 - 1 6
SEALED SYSTEM REP
SEALED SYSTEM REP
SEALED SYSTEM REP
SEALED SYSTEM REP
SEALED SYSTEM REPAIR
AIR
AIR
AIR
AIR
S U M M A R Y
S U M M A R Y
S U M M A R Y
S U M M A R Y
S U M M A R Y
A .
Recover the refrigerant in the
system, if any.
B.
Repair the low side leak or replace
the evaporator and heat exchanger,
whichever applies. If the complete
low side is replaced, do not braze
the suction line to the replacement
compressor until the completion of
Step 3 of System Flush Procedure.
C .
Proceed with the following flush
procedure which includes the
compressor replacement.
D.
After flushing procedure is com-
pleted, continue with the normal
sweep and final charging procedure.
SYSTEM FLUSH PROCEDURE
SYSTEM FLUSH PROCEDURE
SYSTEM FLUSH PROCEDURE
SYSTEM FLUSH PROCEDURE
SYSTEM FLUSH PROCEDURE
1. Isolate and flush the Condenser
1. Isolate and flush the Condenser
1. Isolate and flush the Condenser
1. Isolate and flush the Condenser
1. Isolate and flush the Condenser
Score and break the discharge line at a con-
venient location to which the replacement
compressor tubing can be connected later.
Attach a process tube adapter to the con-
denser side of this break. Connect a quick
coupler hand valve to the process adapter.
Connect the hose from the charging cylin-
der to this valve
(refer to figure 1).
(refer to figure 1).
(refer to figure 1).
(refer to figure 1).
(refer to figure 1).
This con-
nection will remain in place throughout the
flush procedure in Step 3.
NOTE:
NOTE:
NOTE:
NOTE:
NOTE:
Due to the extra flushing and
Due to the extra flushing and
Due to the extra flushing and
Due to the extra flushing and
Due to the extra flushing and
sweep charge procedures, about 12
sweep charge procedures, about 12
sweep charge procedures, about 12
sweep charge procedures, about 12
sweep charge procedures, about 12
ounces of R134A refrigerant should be
ounces of R134A refrigerant should be
ounces of R134A refrigerant should be
ounces of R134A refrigerant should be
ounces of R134A refrigerant should be
added to the original charge specified on
added to the original charge specified on
added to the original charge specified on
added to the original charge specified on
added to the original charge specified on
the model/serial plate and loaded into the
the model/serial plate and loaded into the
the model/serial plate and loaded into the
the model/serial plate and loaded into the
the model/serial plate and loaded into the
charging cylinder initially
charging cylinder initially
charging cylinder initially
charging cylinder initially
charging cylinder initially.....
Next, score and break the tube at the yoder
loop to the input side of the drier. Attach a
process tube adapter to the condenser side
of this break. Connect a quick coupler hand
valve to this process adapter. Connect the
hose from the recovery equipment to this
valve
(figure 1).
(figure 1).
(figure 1).
(figure 1).
(figure 1).
Use the heater on the charg-
ing cylinder to ensure the cylinder pressure
to be approximately 30 pounds above
room ambient temperature. For example,
if room temperature is 70 degrees, cylin-
der pressure should be 100 p.s.i.g. Start the
recovery system and open the valve at the
process adapter attached to yoder loop.
Open the valve from the charging cylinder
and allow 4 ounces of R134A to flow through
the condenser and into the recovery sys-
tem. This process should take about two
minutes. Keep the process adapters and
hoses attached at this time.
Содержание R134A
Страница 4: ...iii iii iii iii iii 599 513 874 EN ...
Страница 8: ...vii 599 513 874 EN ...
Страница 40: ...2 1 2 AUTO DAMPER CONTROL Exploded View ...
Страница 94: ...7 9 REFRIGERANT FLOW RD1 ...