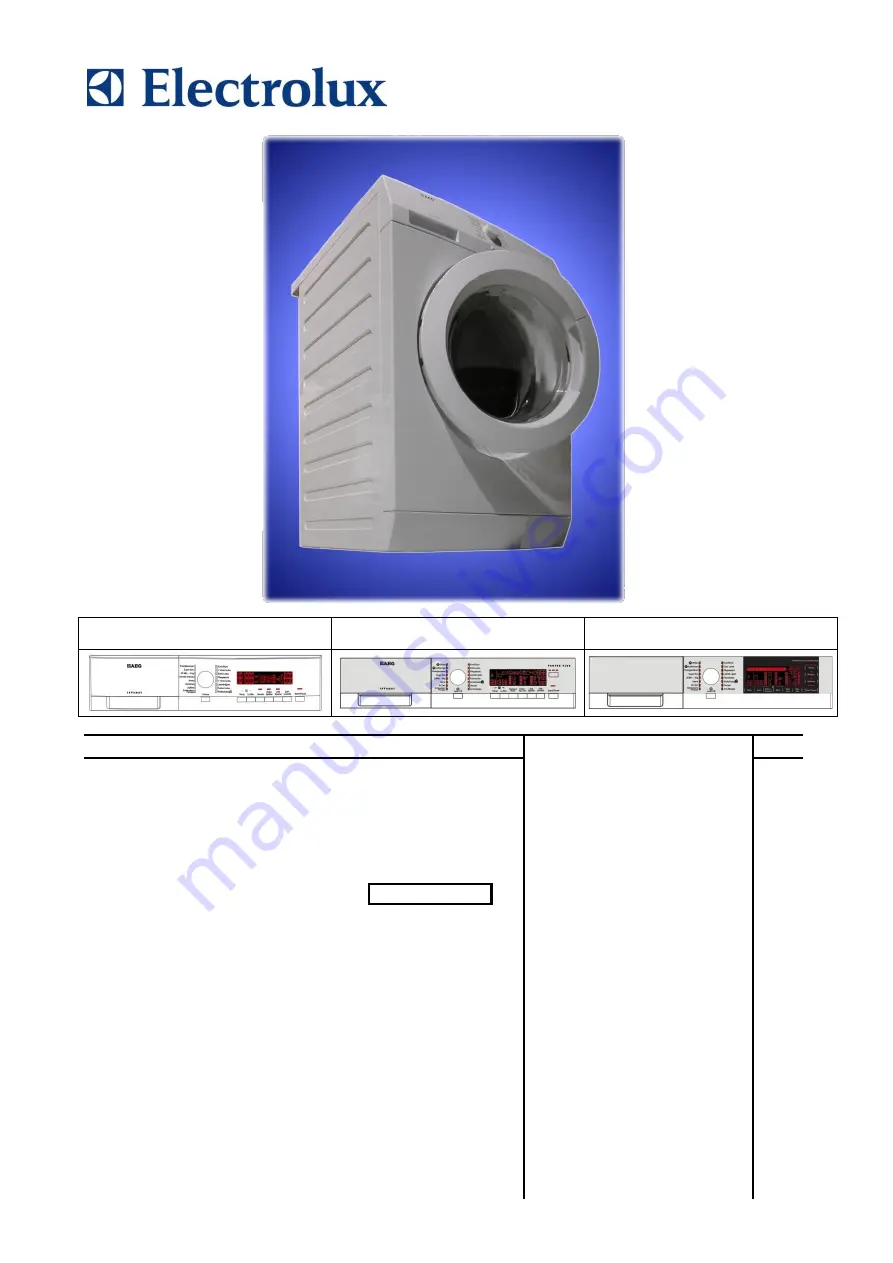
SERVICE MANUAL
WASHING
Washing machines
with electronic control
system
EWX11831
EWX14931
UIMC / EMC14
Inverter
Technical and functional
characteristics
NEW
COLLECTION
SERIES
7/8/9
ELECTROLUX HOME PRODUCTS
Customer Care - EMEA
Training and Operations Support
Technical Support
Publication
number
599 77 23-65
Edition: 06/2015 - Rev. 03
EN
SERIES 7
SERIES 8
SERIES 9