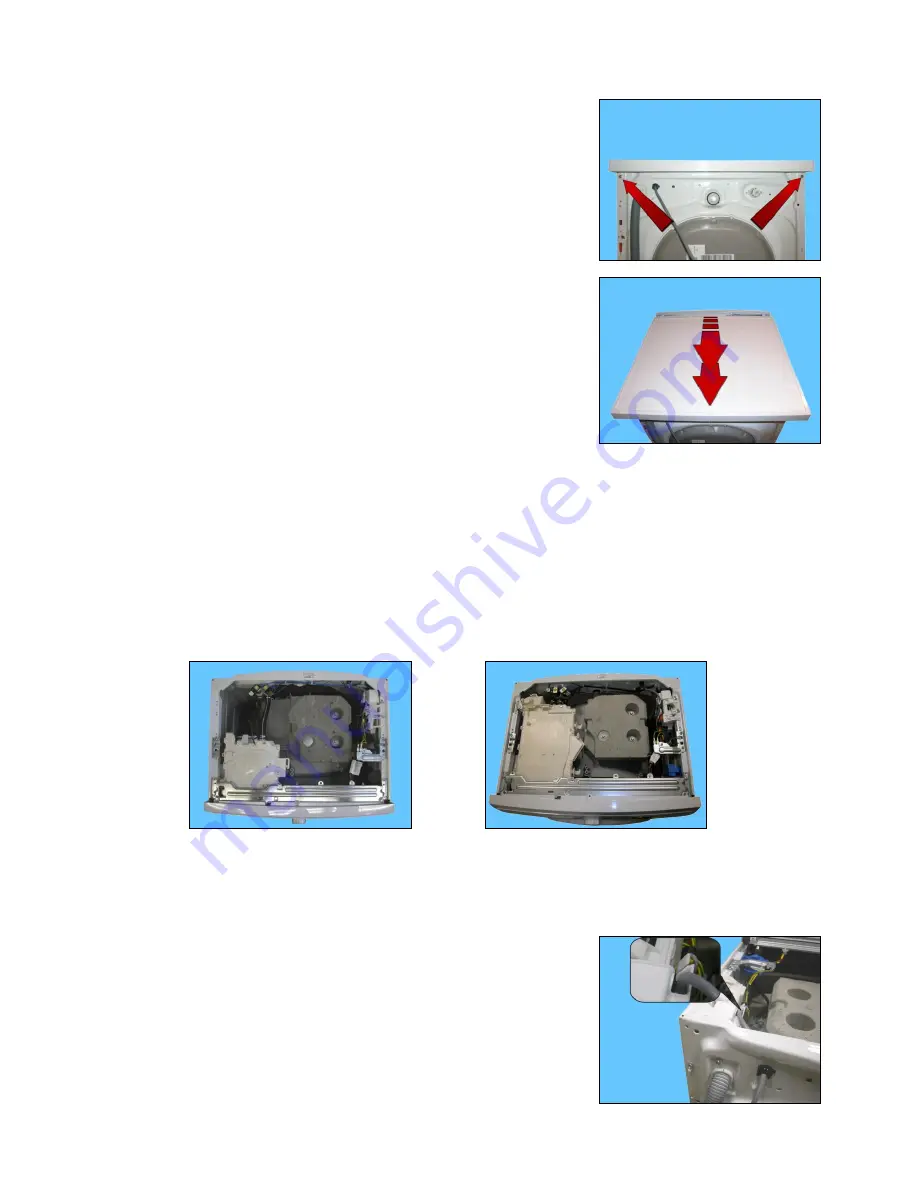
Technical Support - MDM
71/97
599 76 11-68 Rev. 01
14 ACCESSIBILITY
14.1 Worktop
Remove the screws that secure it to the back panel.
Pull it out from the back.
14.2 From the worktop, you can access
1. Main board
2. Solenoid valves
3. Control panel
4. Assembly of display board/selector/LEDs light diffuser
5. Electronic pressure switch
6. Short/Long detergent dispenser
7. Detergent fill pipe
8. Top counterweight
Short dispenser
Long dispenser
14.2.1 Main board EWM09312
Remove the worktop (see relevant paragraph).
Take the power supply cable out of the hook that secures it
to the main PCB casing.
1
2
3
4
5
6
7
8
1
2
3
4
5
6
8
7
Содержание EWF1284EDW
Страница 1: ...Service Catalog PNC ELC Brand Category Model EWF1284EDW 914533914 01 Electrolux Washer FL EWF1284EDW ...
Страница 2: ...Technical Support MDM 2 97 599 76 11 68 Rev 01 ...
Страница 67: ...Technical Support MDM 67 97 599 76 11 68 Rev 01 13 DIAGRAMS 13 1 EWM09312 Operating Circuit Diagram ...
Страница 69: ...Technical Support MDM 69 97 599 76 11 68 Rev 01 13 3 EWX13611 Operating Circuit Diagram ...