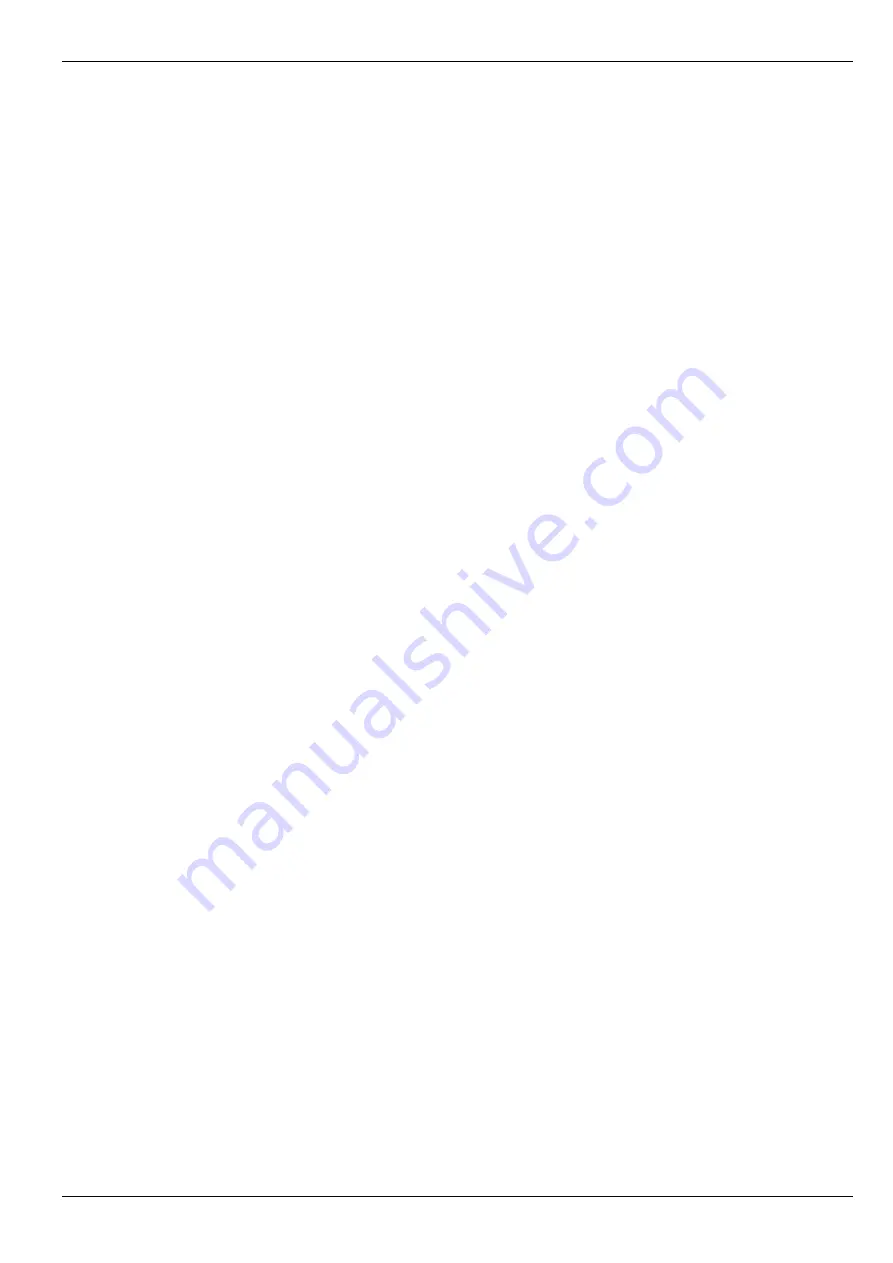
Manual SCA-B4-70-10
V 1.6
01/01 page 10
ElectroCraft GmbH, Vor dem Lauch 19, D-70567 Stuttgart, Germany
Tel.:+49-(0)711-727205-0, Fax.:+49-(0)711-727205-44 E-mail:[email protected]
8. versions of text
V1.2 (07/99)expanded version
V1.5 (06.00) additional description of input and output signals encoder, set value, error, enable,
monitor. supplementary information of EMC. changed description of function of J2.
V1.6 (01/01) changed description of the error output.