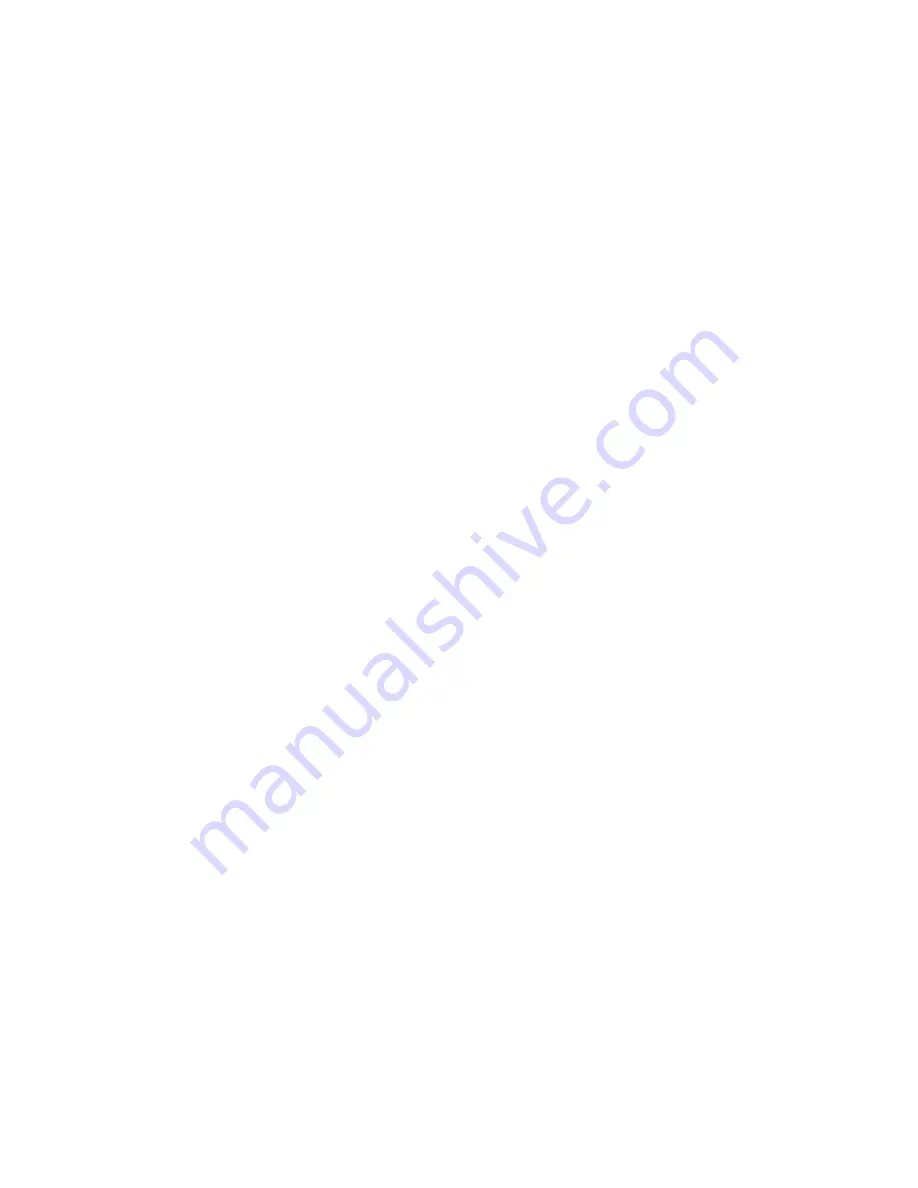
P/N 0013-1027-005 Rev A
Product Notice
Use of IQ 2000/5000 Positioning Drive Modules
IQ 2000/5000 Positioning Drive Modules (PDM) are intended for use as transistorized electronic amplifiers
powering servo motors in machinery. As such, they must be part of a controlled system that includes a
controlling device. They are not intended to independently control a motor. Instructions in the motor and
control system manuals must be observed; this document does not replace those instructions.
Unless specified otherwise, IQ 2000/5000 PDM are intended for use in a normal industrial environment,
installed in a suitable electrical cabinet without exposure to excessive or corrosive moisture or abnormal
ambient temperatures. The exact operating conditions may be established by referring to the data for the
PDM. The connection and control of PDMs in machinery is a skilled operation, disassembly or repair must
not be attempted. In the event that a PDM fails to operate correctly, contact the place of purchase for return
instructions.
Safety Notes
There are some possible hazards associated with the use of Positioning Drive Modules. The following
precautions should be observed. Specific Warnings and Cautions are listed on the back of the Title Page
to the manual.
Installation and Maintenance:
Installation and maintenance or replacement must be carried out by suit-
ably qualified service personnel, paying particular attention to possible electrical and mechanical hazards.
Weight:
PDMs are heavy, the center of gravity may be offset and removable covers shield internal com-
ponents. When handling, take appropriate precautions and lift the equipment using permanent, fixed
surfaces, such as the base; avoid lifting the device using protective cover shields that may be loose. Beware
of sharp edges; use protective gloves when handling such assemblies.
Flying Leads and Loose Cables:
Ensure that flying leads or loose cables are suitably restrained, to prevent
snagging or entanglement, or are disconnected before carrying PDMs with such leads or cables.
Generation:
If a motor is driven mechanically, it may generate hazardous voltages which are conducted
from its power input terminals to the PDM. The power connector must be suitably guarded to prevent a
possible shock hazard.
Loose
PDMs: When running an unmounted PDM, ensure that the cooling fan is adequately guarded and
sufficient airflow is provided around the PDM to ensure adequate cooling. The mounting surface of the
PDM is a heatsink and its surface temperature may increase when the PDM is operating. If a motor is
connected to the PDM, remove the key which otherwise could fly out and restrain the motor before apply-
ing power to the PDM.
Damaged cables:
Damage to cables or connectors may cause an electrical hazard. Ensure there is no
damage before energizing the system.
Supply:
PDMs connect to a permanent main power source; not a portable power source. Suitable fusing
and circuit protection devices are required. Consult the instructions and adhere to local and national
regulations before connecting and energizing the PDM.
Safety Logic Signals:
Logic signals from the PDM are interruptible signals; they are removed when power
is removed from the PDM. Consult the manual for information on auxiliary power connections that may
be employed when these signals are used for safety purposes.
Safety Requirements:
The safe incorporation of IQ 2000/5000 Positioning Drive Moduless into a machine
system is the responsibility of the machine designer, who should comply with the local safety requirements
at the place where the machine is to be used. In Europe this is likely to be the Machinery Directive, the
ElectroMagnetic Compatibility Directive and the Low Voltage Directive. In the United States this is likely
to be the National Electrical Code.
Mechanical Connection:
PDMs must be installed inside an electrical cabinet that provides environmental
controls and protection. Installation information for the PDM is provided in the manual and list the min-
imum installation requirements for the PDM are provided in the manual. Motors and controlling devices
that connect to the PDM should have specifications that complement the capabilities of the PDM.
Motors:
Motors controlled by the PDM should only connect to the PDM; they should not connect directly
to the AC line. Use of custom motors requires the entering of a valid thermal time constant, otherwise the
motor overload protection will not function properly.
Содержание IQ 2000
Страница 8: ...Intro 6 Contents P N 0013 1027 005 Rev A ...
Страница 48: ...2 30 Installation P N 0013 1027 005 Rev A FIGURE 2 23 IQ 5000 Transformer Load Regulation Curve ...
Страница 49: ...Installation 2 31 IQ 2000 5000 Installation Manual FIGURE 2 24 PSM AUX Outline and Connection Diagram ...
Страница 51: ...Installation 2 33 IQ 2000 5000 Installation Manual FIGURE 2 26 IQ 2000 Transformer Load Regulation Curve ...
Страница 53: ...Installation 2 35 IQ 2000 5000 Installation Manual FIGURE 2 29 24V Sourcing I O Conversion Card ...
Страница 54: ...2 36 Installation P N 0013 1027 005 Rev A ...
Страница 79: ...Wiring 3 25 IQ 2000 5000 Installation Manual 3Wiring FIGURE 3 25 IQ 5000 Power Wiring ...
Страница 80: ...3 26 Wiring P N 0013 1027 005 Rev A FIGURE 3 26 PSM AUX Connections ...
Страница 81: ...Wiring 3 27 IQ 2000 5000 Installation Manual FIGURE 3 27 IQ 2000 Power Wiring for PDM 10 20 and 30 ...
Страница 82: ...3 28 Wiring P N 0013 1027 005 Rev A FIGURE 3 28 IQ 2000 Power Wiring for PDM 75 ...
Страница 88: ...3 34 Wiring P N 0013 1027 005 Rev A ...
Страница 94: ...4 6 Applying Power for the First Time P N 0013 1027 005 Rev A ...
Страница 104: ...6 4 Specifications P N 0013 1027 005 Rev A ...
Страница 114: ...Help 6 EU Directives P N 0013 1027 005 Rev A ...