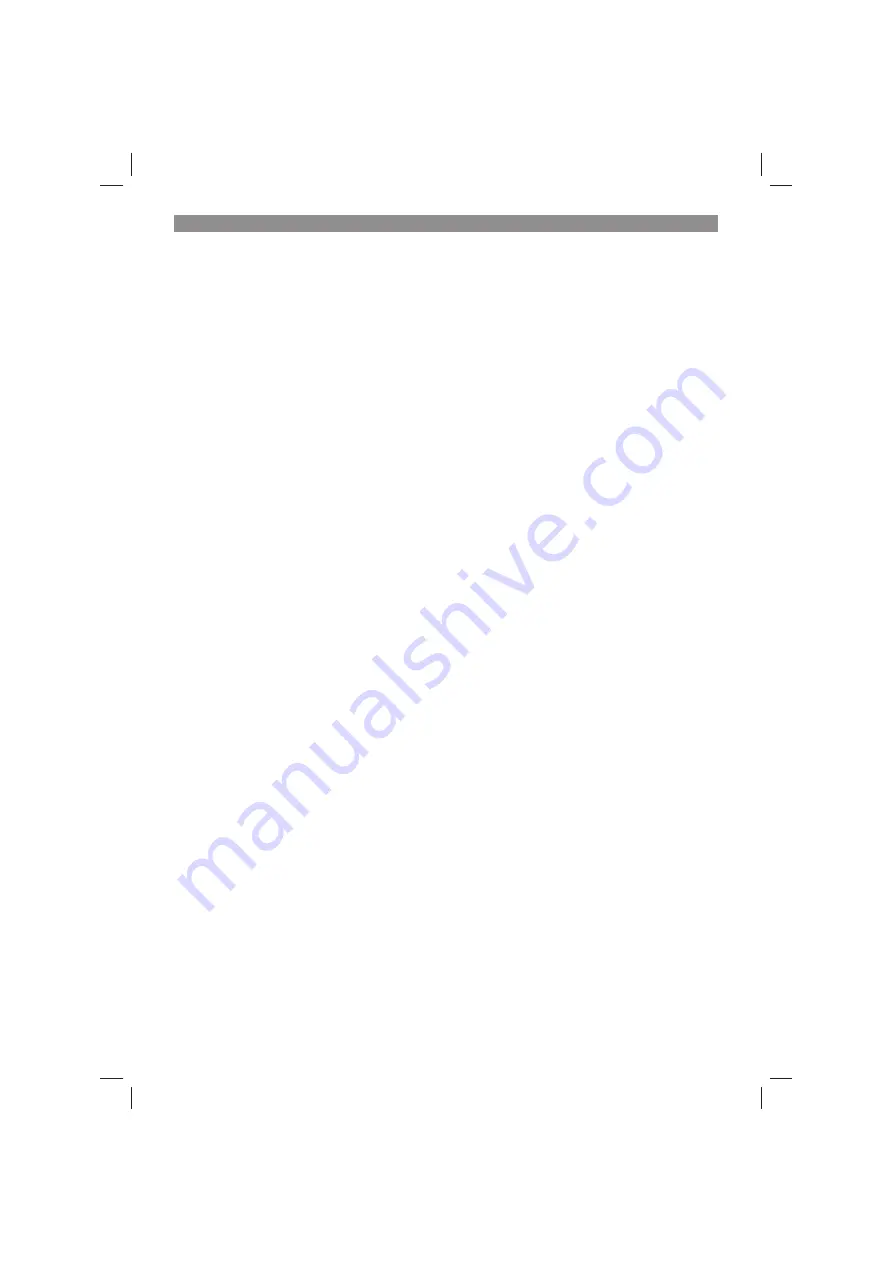
GB
- 18 -
5.2 Setting the guard (Fig. 3)
Warning!
•
Switch off the tool. Pull the power plug.
•
Adjust the guard (4) to protect your hands
so that the material being ground is directed
away from your body.
•
The position of the guard (4) can be adjusted
to any specific working conditions. Undo the
screw (a) and turn the cover (4) into the requi-
red position.
•
Ensure that the guard (4) correctly covers the
gear wheel casing.
•
Retighten the screw (a).
•
Ensure that the guard (4) is secure.
Take care that the safety device is secure.
Never use the angle grinder without the
guard.
5.3 Test run for new grinding Wheels
Allow the right-angle grinder to run in idle for at
least 1 minute with the grinding or cutting wheel
fi
tted in place. Vibrating wheels are to be replaced
immediately.
6. Operation
6.1 Switch (Fig. 4)
The angle grinder comes with a safety switch
which is designed to prevent accidents. To switch
on, press down the On/O
ff
switch (2) at the back,
push it forwards and then press it down at the
front. To switch o
ff
the angle grinder, depress the
On/O
ff
switch (2) at the back. The On/O
ff
switch
(2) will jump back into its starting position.
Restart safeguard
If the mains power supply is interrupted when the
switch is locked in the On position, the electric
tool will not run after the power supply is restored.
For the equipment to run, the switch must be tur-
ned o
ff
and then on again.
Wait until the machine has reached its top
speed. You can then position the angle grin-
der on the workpiece and machine it.
6.2 Changing the grinding wheels (Fig. 5)
Use the face spanner (5) supplied to change the
grinding wheels. The face spanner (5) is stored in
the additional handle (3). Pull the face spanner (5)
out of the additional handle (3) when you need it.
Important!
For safety reasons, the angle grinder
must not be operated with the face spanner (5)
inserted in it.
Warning!
Pull out the power plug.
•
Simple wheel change by spindle lock:
•
Press the spindle lock and allow the grinding
wheel to latch in place.
•
Open the flange nut with the face spanner.
•
(Fig. 5)
•
Change the grinding or cutting wheel and
tighten the flange nut with the face spanner.
Notice!
Only ever press the spindle lock when the
motor and grinding spindle are at a stand-
still! You must keep the spindle lock pressed
while you change the wheel!
For grinding or cutting wheels up to approx. 3 mm
thick, screw on the
fl
ange nut with the
fl
at side
facing the grinding or cutting wheel.
6.3 Flange arrangements when using grin-
ding wheels and cutting wheels (Fig. 6-9)
•
Flange arrangement when using a de-
pressed-centre or straight grinding wheel
(Fig. 7)
•
a) Clamping flange
•
b) Flange nut
•
Flange arrangement when using a de-
pressed-centre cutting wheel (Fig. 8)
•
a) Clamping flange
•
b) Flange nut
•
Flange arrangement when using a straight
cutting wheel (Fig. 9)
•
a) Clamping flange
•
b) Flange nut
6.4 Motor
It is vital for the motor to be well ventilated during
operation. Be sure, therefore, to keep the ventilati-
on holes clean at all times.
Anl_TC_AG_115_750_SPK9.indb 18
Anl_TC_AG_115_750_SPK9.indb 18
15.01.2019 07:30:06
15.01.2019 07:30:06
Содержание 44.309.60
Страница 4: ...4 Anl_TC_AG_115_750_SPK9 indb 4 Anl_TC_AG_115_750_SPK9 indb 4 15 01 2019 07 30 03 15 01 2019 07 30 03...
Страница 105: ...RUS 105 Anl_TC_AG_115_750_SPK9 indb 105 Anl_TC_AG_115_750_SPK9 indb 105 15 01 2019 07 30 20 15 01 2019 07 30 20...
Страница 142: ...GR 142 A A Anl_TC_AG_115_750_SPK9 indb 142 Anl_TC_AG_115_750_SPK9 indb 142 15 01 2019 07 30 25 15 01 2019 07 30 25...
Страница 152: ...EH 01 2019 02 Anl_TC_AG_115_750_SPK9 indb 152 Anl_TC_AG_115_750_SPK9 indb 152 15 01 2019 07 30 26 15 01 2019 07 30 26...