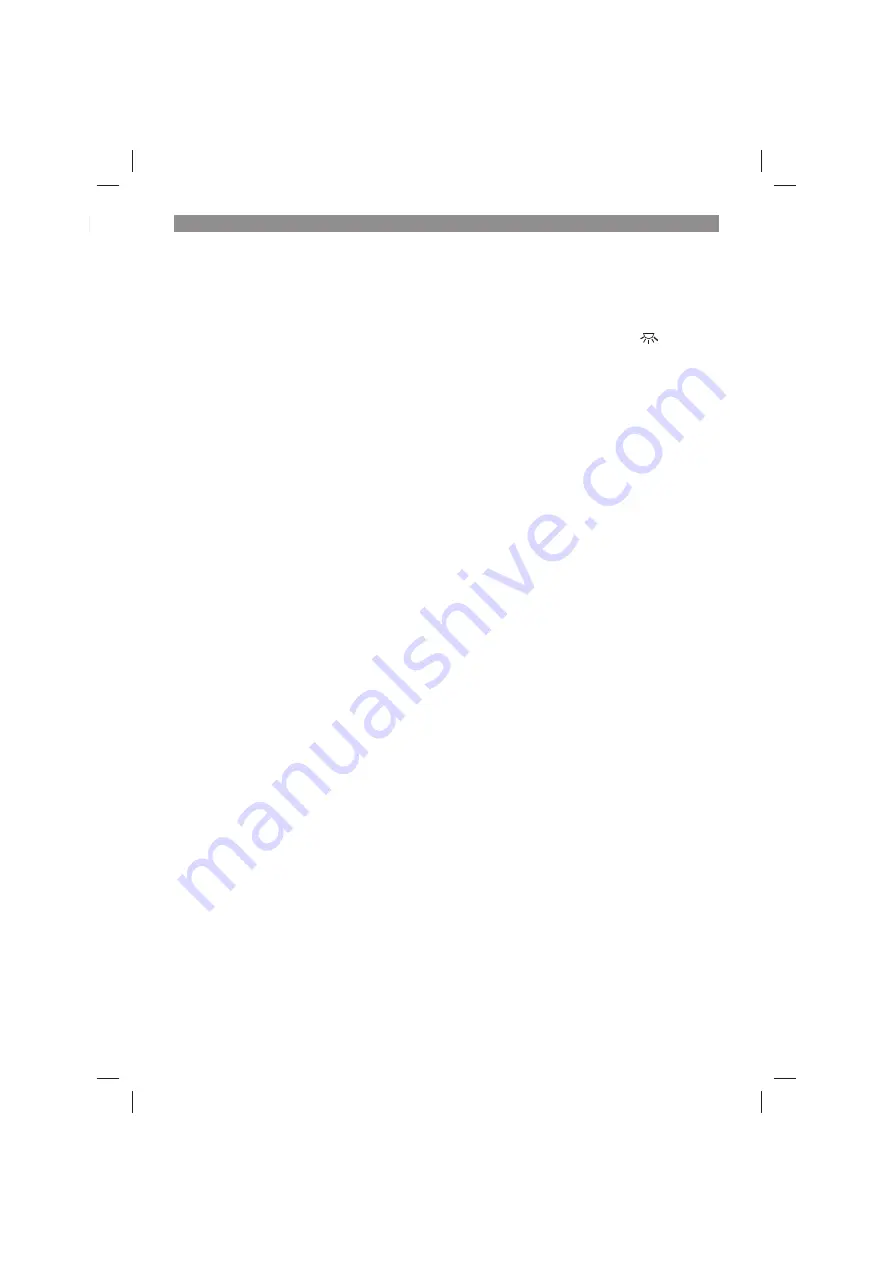
GB
- 29 -
saw again.
5.9 Changing the rubber tires on the blade
pulleys (Fig. 14)
After a certain time the rubber tires (3) on the bla-
de pulleys (7, 8) will get worn by the sharp teeth
of the blades and must be replaced.
•
Remove the blade (26) (see 5.8).
•
Lift the edge of the rubber tire (3) with a small
screwdriver (b) and then pull it off the upper
blade pulley (8). (This product does not come
with a screwdriver (b))
•
Repeat for the lower blade pulley (7).
•
Fit the new rubber tire (3) and re-fit the blade
(26).
•
Tension and adjust the blade (26), and adjust
the upper and lower support bearings (see
5.2, 5.3, 5.4).
5.10 Changing the table insert (Fig. 15)
To prevent increased risk of injury, the table insert
(17) must be replaced whenever it becomes worn
or damaged.
•
Undo the fastening screw of the table insert
(17) with a cross-head screwdriver (c). (This
product does not come with a cross-head
screwdriver (c))
•
Lift the worn table insert (17) up and out.
•
Fit the replacement table insert in reverse
order.
5.11 Extractor socket (Fig. 2)
The bandsaw is equipped with an extractor so-
cket (6) for extracting sawdust and chips. Connect
the bandsaw to a chip extraction system (not in-
cluded in delivery) by connecting the hose of the
extraction system to the extractor socket (6).
5.12 Push stick holder (Fig. 16)
When not in use, the push stick (35) must always
be kept in the holder (36).
6. Operation
6.1 On/O
ff
switch (Fig. 17)
•
To turn the saw on, press the green button „I“.
•
To turn the saw off again, press the red button
„0“.
•
This bandsaw has a switch with undervoltage
release. After a power failure you must switch
on the bandsaw again.
6.2 LED lamp (Fig. 4/17)
•
For good illumination of the work area you
can use the LED lamp (28) in addition to the
room lighting. The On/Off switch for the LED
lamp (56) is directly above the On/Off switch
(1).
•
Switching on: Switch position “
”
•
Switching off: Switch position “OFF”
6.3 Parallel stop (Fig. 18)
•
The parallel stop (24) can be mounted on the
saw table (15) to the left and right of the blade
(26).
•
The parallel stop (24) must be inserted in the
guide rail (37) on the saw table (15).
•
The parallel stop (24) can be set to the requi-
red dimension with the help of the scale (23)
on the guide rail (37).
•
You can clamp the parallel stop in the requi-
red position by pressing the eccentric lever
(21).
•
Important! If the clamping force of the parallel
stop (24) is too low, you can increase it with
the adjusting nut (22) at the rear end of the
parallel stop (24).
6.4 Angular cuts (Fig. 4)
To enable you to perform angular cuts parallel to
the blade (26), the table (15) can be tilted from
0° - 45°.
•
Slacken the wing handle (18).
•
Tilt the saw table (15) until the required angle
value is set on the angle scale (16).
•
Re-tighten the wing handle (18).
•
Important: With the saw table (15) tilted, place
the parallel stop (24) to the right of the blade
(26) looking in the direction in which you are
working, on the side pointing downwards
(provided the workpiece is wide enough) in
order to stop the workpiece from slipping off.
6.5 Cross stop (Fig. 1)
•
Push the cross stop (10) into the groove in
the saw table (15).
•
You can use the cross stop (10) to perform
angle cuts transverse to the blade (26).
•
Undo the locking screw (52).
•
Set the cross stop to the desired angle.
•
Re-tighten the fastening screw (52).
Danger!
Never use the cross stop (10) and the parallel
stop (24) simultaneously. If you use the parallel
stop (24) and the cross stop (10) simultaneously
to guide the workpiece there will be a greater risk
Anl_TC-SB_245_L_SPK9.indb 29
19.11.2020 08:10:09
Содержание 43.080.35
Страница 8: ... 8 21b 22 23 24 54 54 2 7 53 55 11 Anl_TC SB_245_L_SPK9 indb 8 19 11 2020 08 09 38 ...
Страница 164: ... 164 Anl_TC SB_245_L_SPK9 indb 164 19 11 2020 08 10 31 ...
Страница 165: ... 165 Anl_TC SB_245_L_SPK9 indb 165 19 11 2020 08 10 31 ...
Страница 166: ...EH 11 2020 01 Anl_TC SB_245_L_SPK9 indb 166 19 11 2020 08 10 31 ...