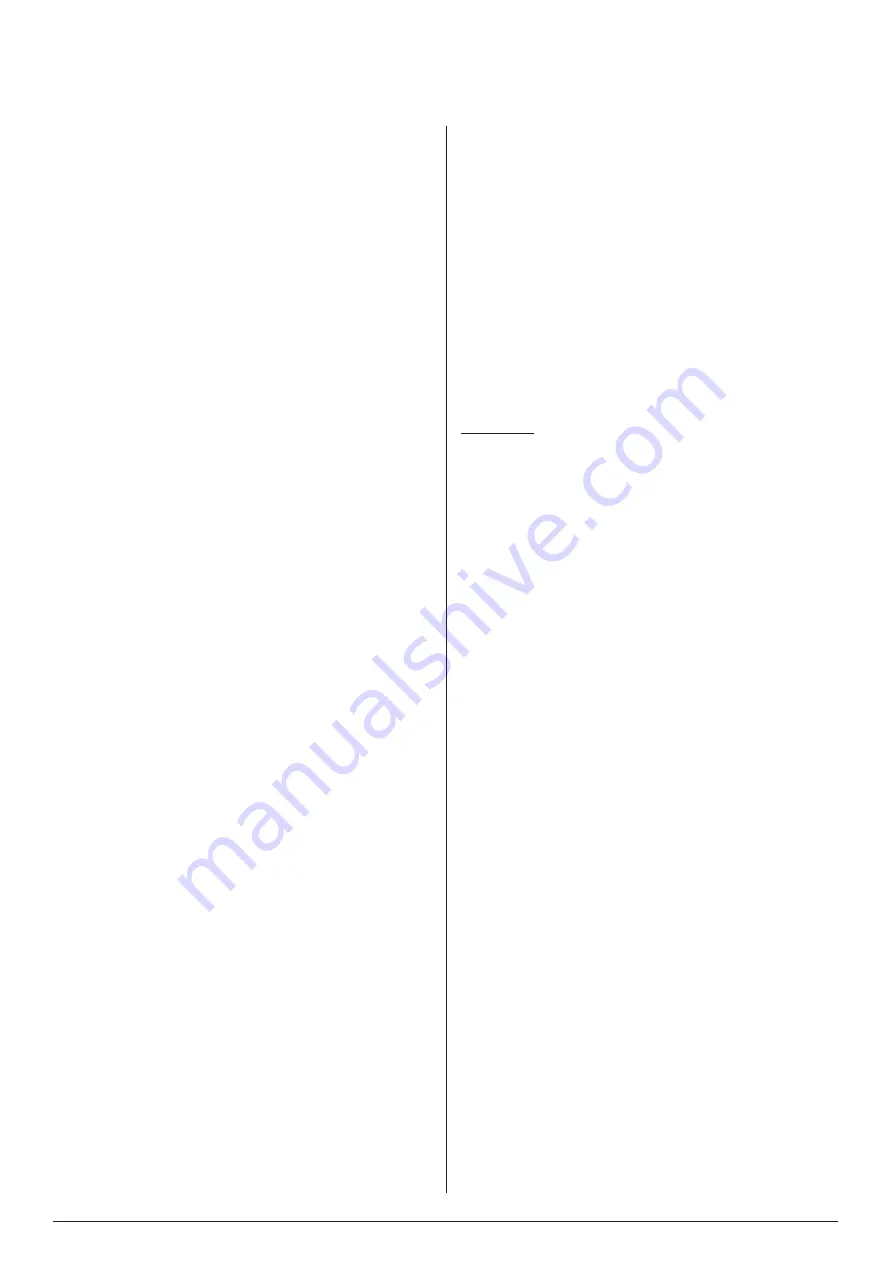
4
GB-031C_f
InsTallaTIOn
1. General
The boiler must be installed by a professional plumber or heating
engineer and must be connected to the public low voltage
network by a competent person. For systems that require a three
phase electrical supply we strongly recommend this is installed
by a 17th Edition certified Electrician.
The Electric heating Company ltd will not be held responsible
for faulty installations which are performed by unqualified
tradespersons.
2. Pipe Connections
All Fusion Electric Boilers have a 22mm compression connection
at the boiler’s flow and return pipes. Please note that the boilers
are supplied with blank washers fitted for transit purposes. These
must be removed before connections to pipe-work can be made.
The flow (red) and return (blue) are clearly marked on the external
case and under no circumstances should these connections be
reversed. Hot connections are not recommended at the boiler for
future maintenance and boiler disconnection. Lockshield valves
are recommended.
3. Case Removal
Remove outer screws at the bottom of the boiler and pull the front
cover outwards taking care to remove internal earth connections.
Earth connections must be re-connected before the boiler case is
re-installed.
4. Isolation Valves
We recommend that lockshield isolation valves are fitted on the
flow and return pipework. Such valves must be „full bore” and not
„standard ball valves”. The installation of „standard ball valves” in
the flow and return pipework will reduce the recommended flow
rate through the boiler and promote premature boiler shutdown.
5. auto air vents
An auto air vent is integral within the boiler however an additional
auto air vent must be fitted at the cylinder coil if the boiler is being
used for central heating and domestic hot water.
6. Boiler sizing
Calculate the „space heating” requirements in accordance with BS
EN 12831 and BS EN 14336. If the boiler is to heat the domestic
hot water, an additional allowance of 3kW (10,239 Btu’s) should
be made to the ‘space heating’ calculation.
7. Insulation
Where practical, and if at all possible, we recommend that all
pipe-work be insulated, in particular the primary pipe-work
within a boiler cupboard. This is to reduce heat loss and reduce
high cupboard temperatures from exposed pipe-work. (BS 6700).
8. system Design
The boiler has an integral automatic bypass valve fitted which
should be set to the relevant settings to allow the minimum
flow rates to pass through the boiler (8 l/min) when all radiator
thermostats and zone valves are closed.
Allowance should be made for a radiator to be installed within
the heating circuit and locked open. This will be located in the
room that has the room thermostat installed.
To comply with building regulations, Part L and Part J (in Scot-
land), room and cylinder stats must be fitted.
9. Water Connections
Provisions must be made for the replacement of water lost from
the heating system (sealed systems). Reference should be made
to BS EN 14336 for the method of filling and make up of water.
There must be no direct connection between the boilers central
heating system and the main water supply. When mains water is
required to fill the system directly, all local water bylaws must be
observed, and any connection made must be disconnected after
use.
10. Flushing
The system
must be flushed
to within 10% of mains water PPM to
ensure that no debris is trapped in the system as this may result in
boiler failure. Where existing radiators and pipe-work are utilized
a power flush must be carried out to remove debris. For further
guidance please see section - Flushing & System Protection.
11. system pressures
All boilers are tested to 4.0 bar. The normal working pressure
of the boiler should be set to approx 1.0 / 1.5 bar. All sealed
systems should comply with the relevant building regulations and
standards, including BS EN 13831 – Specification for Expansion
Vessels.
Please note:
In order to protect the Flow Sensor located within the boiler, it is
imperative that the pre-installed magnetic filter is removed and
cleaned at least annually. Failure to carry out this action will
increase contamination of the boiler by system residue.
12. system types
The Fusion Comet range of boilers can be used in various system
designs. Please refer to The Electric Heating Company for more
details on our Fusion Boiler for under floor heating. We are able
to supply a heat pack that contains the relevant control valves,
cylinder and room thermostats required to configure an „S” plan
heating system. The heat pack has all the necessary components
that you need to connect the systems controls and plumbing
configurations for „S” Plan design.
We recommend the use of thermostatic radiator valves on all
radiators except in the room that has the wall thermostat fitted.
This radiator should be fitted with lock shield valves and left in
the fully open position.
The boiler has an integral automatic bypass valve fitted which
should be set to the relevant settings to allow the minimum
flow rates to pass through the boiler (8 l/min) when all radiator
thermostats and „zone valves are closed”.
Systems should be designed to meet the current building
regulations in force at the current time.
13. hanging the Boiler
1. Hang the boiler in a vertical position on the fixing points and
screws provided, with the flow and return connections to the
bottom of the boiler, maintaining the clearances as per Figure
12 of this manual.
2. Connect the boiler to a heating system that is equipped with
isolation valves (see Figures 4 & 5).
3. Fill the heating system with treated water, which will
substantially extend the life of the heating coils. See item 14
„System Protection” below.
4. Connect the boiler to the „mains” electrical system as per
Figures 6, 8, 9 & 11
5. Connect the room thermostat / Programmer using the two
control conductors marked RP as in Figure 7 & 10.
6. For all other electrical connections refer to the ELECTICAL
CONNECTIONS & CONTROL section of this manual.
Содержание Fusion Comet EHCCOM12KW
Страница 8: ...8 GB 031C_f Temporary Filling Loop Mains Water Supply INSTALLATION Figure 4 ...
Страница 9: ...9 GB 031C_f Figure 5 Temporary Filling Loop Mains Water Supply ...
Страница 18: ...18 GB 031C_f EXTERNAL BOILER WIRING BOILER DIMENSIONS Figure 11 Figure 12 Return Inlet Flow Outlet 710 ...
Страница 23: ...23 GB 031C_f ...