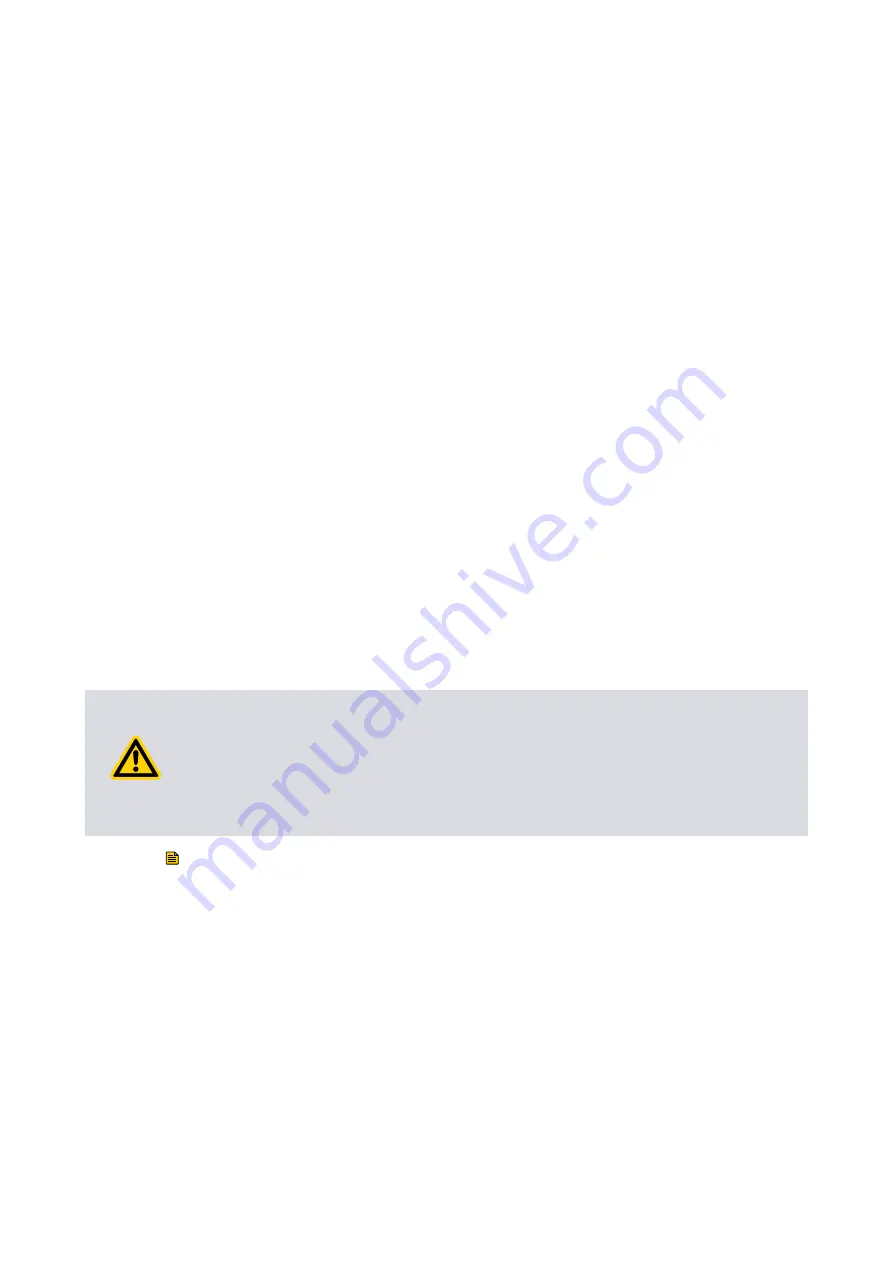
▪
When pumping condensible vapours and particulates, more frequent fluid changes
are required to maintain pump life. Contact us about types and styles of filtration
units.
▪
Make sure there is no backpressure in the exhaust line of the vacuum pump.
Vacuum pumps are not specifically designed to compress exhaust gas above
atmospheric pressure. Significant back pressure can overheat the pump and cause
motor overloading. Backpressure on the pump should not exceed 0.15 bar(e)
under normal operating conditions.
▪
Maintain system seals regularly. Damaged O-rings and gaskets must be replaced
immediately. All flange faces must be free of dirt, lubricant and scratches.
▪
Do not use collapsible tubing to plumb the vacuum system. Any restrictions in line
diameter caused by tube collapse will reduce available pumping capacity.
▪
In multiple pump installations, check valves should be installed in the inlet piping.
This will prevent fluid from being drawn from an 'off' unit into an operating unit.
Check valves should be properly sized so as not to "chatter" during operation.
Spring
‑
loaded, elastomer seated check valves are recommended. These should be
mounted in a horizontal flow orientation. Using properly sized actuated valves is
even a better solution. This generally results in a lower pressure drop when open
and a better sealing when closed.
▪
Vacuum gauge ports and gauges should be installed in each leg of central vacuum
piping. This provides a diagnostic tool for troubleshooting both the application and
any pump
‑
related problems.
▪
Make sure that no temperature-sensitive parts (plastic, wood, cardboard, paper,
and electronics) will touch the surface of the vacuum pumps.
▪
Ambient and inlet temperature may never exceed the limits of the pump's working
range. Make sure that the installation location is vented such that enough cooling
of the vacuum pumps are available.
WARNING: CONTAMINATION TO PARTS
Risk of damage to equipment. Touch the inner sections of the pumps only while
wearing clean gloves. Use clean tools to do the necessary work in a clean and dry
room.
Clean the bearings before re-greasing.
Note:
The grease of the bearings must be changed once a year for an operating time higher
than 5000 hours/year or every 5000 hours for an operating time less than 5000 hours/
year.
4.3 Electrical connections
▪
Always use a protection system, including an over-current protection and an
electrical disconnecting device, between the pump and the electric power supply.
Motor currents can be found on the motor data plate. The pump is normally
delivered without an electrical cable or switch. For the electrical connection, check
the diagram inside the terminal box or on the motor data plate.
▪
For pumps with a three-phase motor, check the diagram inside the terminal box or
on the motor data plate.
Page 30 - 07/2020
A35104880_B - Installation
Содержание nES Series
Страница 5: ...This page has been intentionally left blank...
Страница 6: ...This page has been intentionally left blank...
Страница 55: ......
Страница 56: ...edwardsvacuum com...