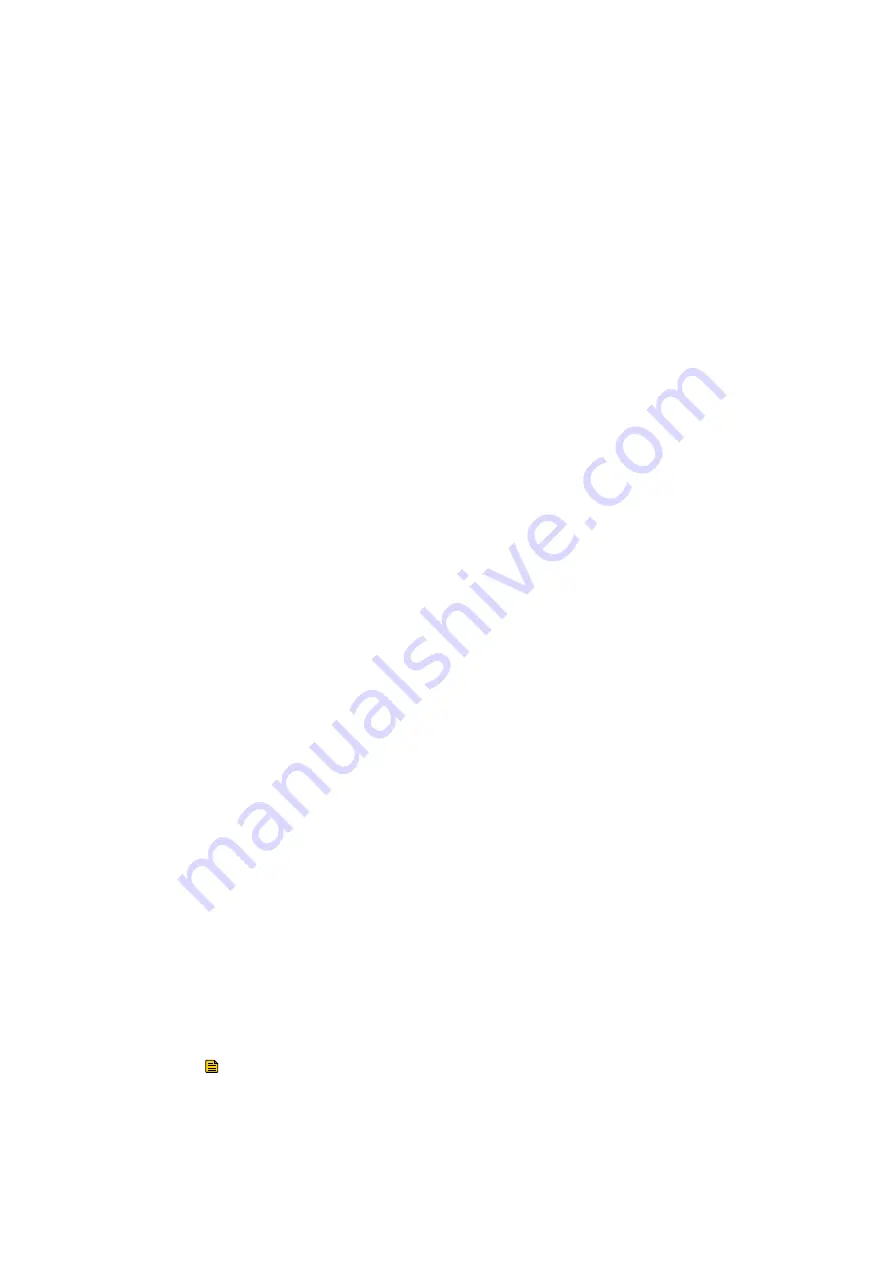
5.
A warning sign bearing a legend such as "Work in progress; do not start" shall be
attached to the starting equipment.
6.
Persons switching on remotely controlled machines shall take adequate
precautions to ensure that there is no one checking or working on the machine. To
this end, a suitable notice shall be affixed to the remote start equipment.
7.
Before removing any component, effectively isolate the machine from all sources
of under and/or overpressure and make sure that the pump system is at
atmospheric pressure level.
8.
Never use flammable solvents or carbon tetrachloride for cleaning parts. Take
safety precautions against toxic vapours of cleaning liquids.
9.
Scrupulously observe cleanliness during maintenance and repair. Keep dirt away by
covering the parts and exposed openings with a clean cloth, paper or tape.
10.
Never weld or perform any operation involving heat near the oil system. Oil tanks
must be completely purged, for example, by steam cleaning, before carrying out
such operations. Never weld on, or in any way modify, pressure vessels.
11.
Whenever there is an indication or any suspicion that an internal part of a machine
is overheated, the machine shall be stopped but no inspection covers shall be
opened before sufficient cooling time has elapsed. This will avoid the risk of
spontaneous ignition of the oil vapour when air is admitted.
12.
Never use a light source with an open flame for inspecting the interior of a
machine, pressure vessel, and so forth.
13.
Make sure that no tools, loose parts or rags are left in or on the machine.
14.
All regulating and safety devices shall be maintained with due care to ensure that
they function properly. They may not be put out of action.
15.
Before clearing the machine for use after maintenance or overhaul, check that
operating pressures, temperatures and time settings are correct. Check that all
control and shut-down devices are fitted and that they function correctly. If
removed, check that the coupling guard of the vacuum pump drive shaft has been
reinstalled.
16.
Every time the separator element is renewed, examine the discharge and the
inside of the oil separator vessel for carbon deposits. If there are excessive
deposits, remove it.
17.
Protect the motor, air filter, electrical and regulating components, and so forth, to
prevent moisture from entering them, for example, when steam cleaning.
18.
Make sure that all sound damping material and vibration dampers, for example,
damping material on the bodywork and in the air inlet and outlet systems of the
vacuum pump are in good condition. If damaged, replace it with genuine material
from the manufacturer to prevent the sound pressure level from increasing.
19.
Never use caustic solvents which can damage materials of the air net, for example,
polycarbonate bowls.
20.
Faults or wearing of seals may cause oil lubricant leaks. Avoid dispersion in soil and
pollution of other materials.
Note:
Refer to Safety precautions during installation on page 10
on page 8 and Safety precautions during operation on page 12
Safety precautions during operation
07/2020 - Page 11
A35104880_B - Safety and compliance
Содержание nES Series
Страница 5: ...This page has been intentionally left blank...
Страница 6: ...This page has been intentionally left blank...
Страница 55: ......
Страница 56: ...edwardsvacuum com...