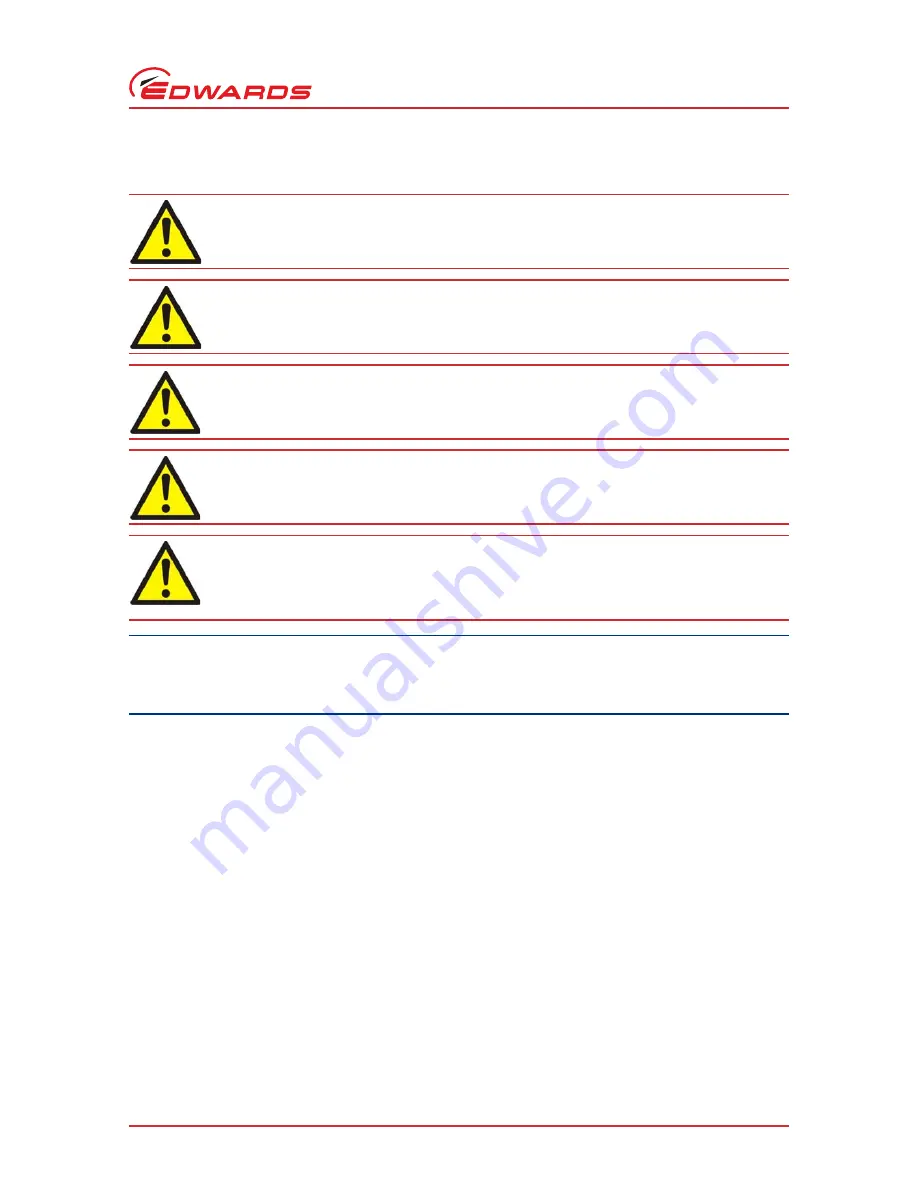
© Edwards Limited 2011. All rights reserved.
Page 17
Edwards and the Edwards logo are trademarks of Edwards Limited.
Installation
S149-01-880 Issue F
3.6
Exhaust piping
CAUTION
Do not place a valve in the exhaust line. If a valve must be installed in the line, a relief valve must also be
inserted between the reservoir and the valve. The relief valve should be equal in size to the line, and set to
open at 138 mbar (2 psig).
The pumps emit tiny oil droplets into the exhaust of the pump. Edwards recommends the use of exhaust filters to
prevent these droplets from accumulating in the exhaust piping of the system or where the piping terminates. The
oil and condensables will coalesce inside the piping and return to the pump reservoir or be collected inside the filter
housing.
For all 149-H/149-HS and those 212-J and 412-J pumps that do not use an exhaust filter, it is recommended that the
exhaust be piped horizontally a short distance and tied into a vertical exhaust pipe. The lower vertical exhaust pipe
must be at least 305 mm (12 inch) long and terminated with a plug or drain cock to allow removal of moisture and/
or contaminated oil before it can sufficiently accumulate and drain back into the pump oil reservoir (See
Figure 10
).
For 212-J and 412-J pumps with an exhaust filter, the vertical collection pipe is not required. These filters collect
the coalesced oil and condensables inside the filter housing. The housing must be drained of fluids using the drain
cocks. Failure to drain the oil from exhaust filters will result in decreased pump performance and significantly
increased back pressure.
The exhaust pipe should be no smaller than the pump exhaust outlet and sized as short as possible. Pump exhaust
will contain a small amount of oil and should be handled in a manner consistent with applicable federal and local
regulations. If exhausted outside the building, point the end of the exhaust pipe downward to prevent the entrance
of rain water.
Oil mist separators are available from Edwards which can eliminate oil fog in the majority of applications. The
separator will not remove noxious or toxic gases and must be run to a suitable trap. Consult Edwards for
recommendations.
WARNING
Do not block the exhaust of the pump. If this happens, damage to the equipment and injury to
personnel can result.
WARNING
Vacuum piping should be adequately supported. Ensure the piping is secured and will not cause a
trip hazard.
WARNING
The pump exhaust pressure must not exceed 483 mbar (7 psig). If this happens, damage to
equipment and injury to personnel can result.
WARNING
Remove the plastic plug from the exhaust port prior to operating the pump. The pump must not
be operated unless it is installed in an appropriate vacuum system.
WARNING
Exhaust filters fitted to 212-J and 412-J pumps must be drained to prevent hazardous back
pressure from developing. Increased back pressure can result in damage to the pump and injury
to people.