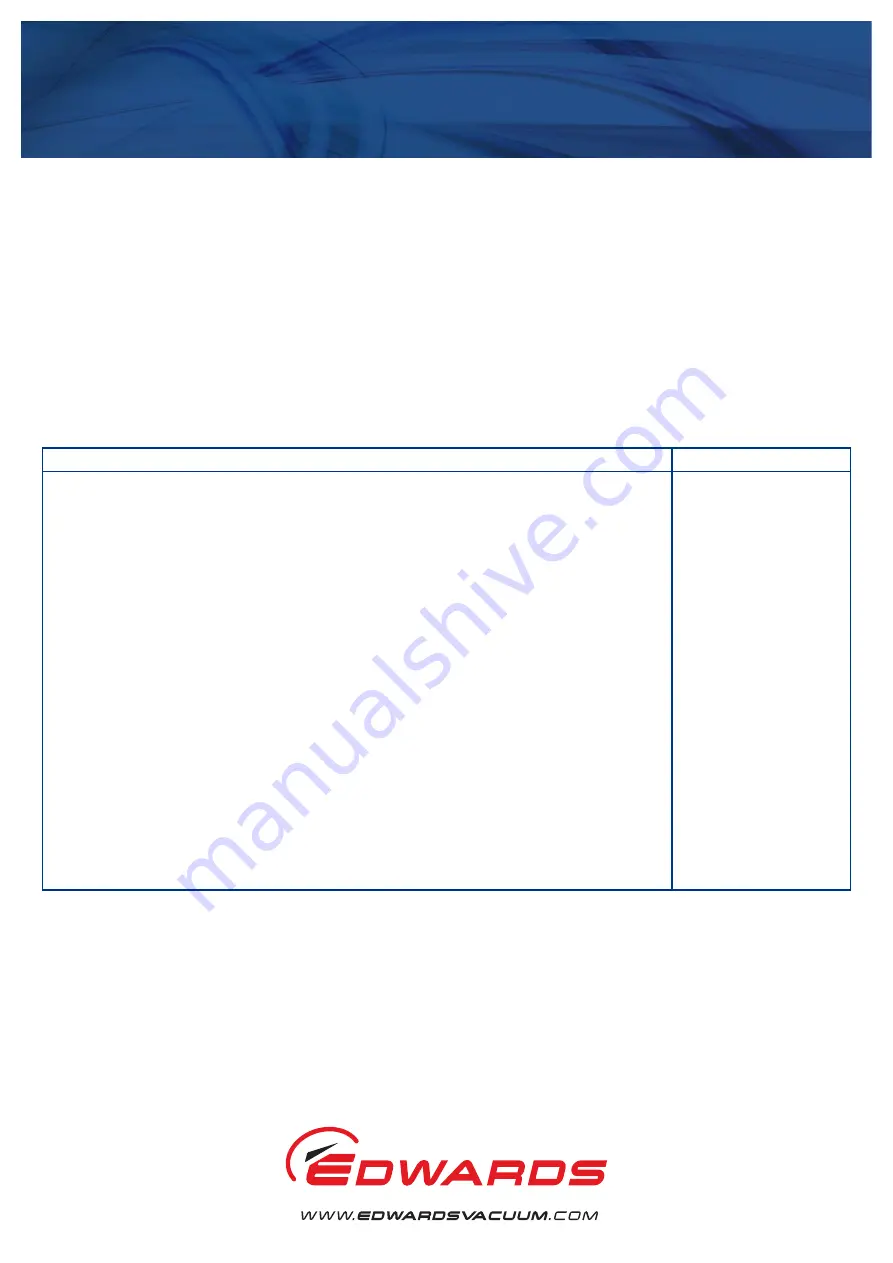
B064-04-880
Issue F Original
Instruction Manual
30B5M Vapour Booster Pumps
Description
Item Number
Unconfigured 30B5M Vapour Booster Pumps:
200 V, 50/60 Hz, 3-phase
B064-07-200
220 V, 50/60 Hz, 3-phase
B064-07-220
380 V, 50/60 Hz, 3-phase
B064-07-380
400 V, 50/60 Hz, 3-phase
B064-07-400
415 V, 50/60 Hz, 3-phase
B064-07-415
440 V, 50/60 Hz, 3-phase
B064-07-440
460 V, 50/60 Hz, 3-phase
B064-07-460
480 V, 50/60 Hz, 3-phase
B064-07-480
Control Configured 30B5M Vapour Booster Pumps:
200 V, 50/60 Hz, 3-phase
B064-08-200
220 V, 50/60 Hz, 3-phase
B064-08-220
380 V, 50/60 Hz, 3-phase
B064-08-380
400 V, 50/60 Hz, 3-phase
B064-08-400
415 V, 50/60 Hz, 3-phase
B064-08-415
440 V, 50/60 Hz, 3-phase
B064-08-440
460 V, 50/60 Hz, 3-phase
B064-08-460
480 V, 50/60 Hz, 3-phase
B064-08-480
Содержание 30B5M
Страница 4: ...This page intentionally blank ...