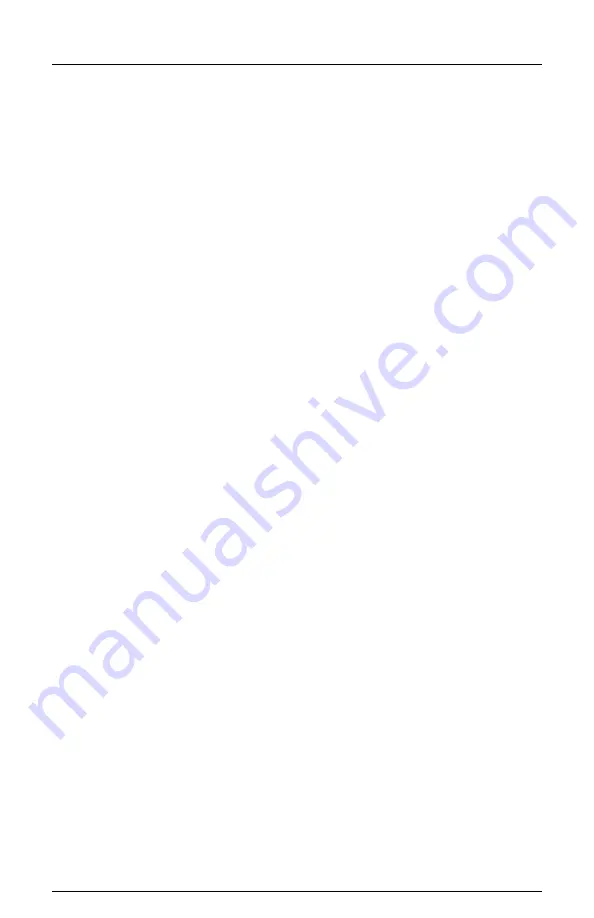
2018KCL(ip) SERIES SIGNAL MONITOR
OPERATIONS MANUAL
Eberle Design Inc.
Page 3
Section 2
EXTENDED FEATURES
The following extended features are provided on the Signal Monitor to provide additional
fault monitoring functions, to increase the reliability of the monitor operation, and enhance
the diagnostic capabilities offered to the service technician.
2.1 HARDWARE FEATURES
The 2018KCL is a dual microprocessor based unit. All monitoring functions and features
are firmware programmable that permits upgrades or modifications by simply replacing the
EPROM device containing the firmware with the upgraded version. Thus, most changes to
the Signal Monitor specifications may be accommodated without modifying the hardware.
Since all critical timing functions are accomplished by the microprocessor, the quartz
crystal based accuracy results in very precise and repeatable measurements. This
accuracy is maintained on functions from timing fault conditions to implementing a unique
firmware based digital sampling and filtering algorithm. This algorithm is applied to all AC
field signals to help eliminate false detection in a "noisy" AC line environment.
Input voltages are measured using a true Root Mean Squared (RMS) technique. A
dedicated microprocessor RMS- Engine controls the analog to digital (A/D) hardware which
samples each AC input voltage 32 times per cycle. The RMS-Engine then calculates the
true RMS voltage value producing accurate results which are very insensitive to changes in
frequency, phase, wave shape, and distortion. Voltage references are temperature
compensated for constant voltage levels within the operating temperature range.
A nonvolatile EEPROM device is utilized to retain fault status information and event logs in
the event of an AC Line power interruption. The correct fault indications will be displayed
upon restoration of AC Line power. This EEPROM device requires no battery back-up. The
time of day in the model 2018KCL unit is stored in a battery-backed real time clock circuit.
Should this battery fail, only current time of day and date information will be lost. No
monitor configuration programming is stored under battery power.
2.2 RED FAILURE MONITORING
The 2018KCL is designed to adapt Red Failure Monitoring to a conventional controller
cabinet assembly. The simultaneous absence of active Green, Yellow, and Red field signal
voltages on a channel places the 2018KCL into the fault mode illuminating the RED FAIL
indicator, transferring the Output relay contacts to the fault position and enabling the Stop-
Time output to the controller. Sixteen Red signal inputs, a Red Enable input, and two
Special Function preemption inputs (SF1,2) are connected to the monitor via a front panel
connector (P1) and ribbon cable assembly. Channel 17 and 18 Red signal inputs are
connected to the monitor via the main connector (P6). Chassis Ground may also be
connected to the unit through pin P1-4. Jumper E1 must then be inserted to complete the
connection.
The Red Fail fault timing value is selected by the Red Fail Timing Short Option. See section
4.2.3.11.
The Red Failure monitoring function is enabled by applying AC+ to the Red Enable input
(P1-20). Each channel is enabled for Red Failure monitoring via Red Fail Enable
programming in the Datakey. Red Failure monitoring is disabled for all channels when the
Red Enable input is not active, a Preemption input (SF1,2) is active, or the pin #EE input
(MC Coil) is active.