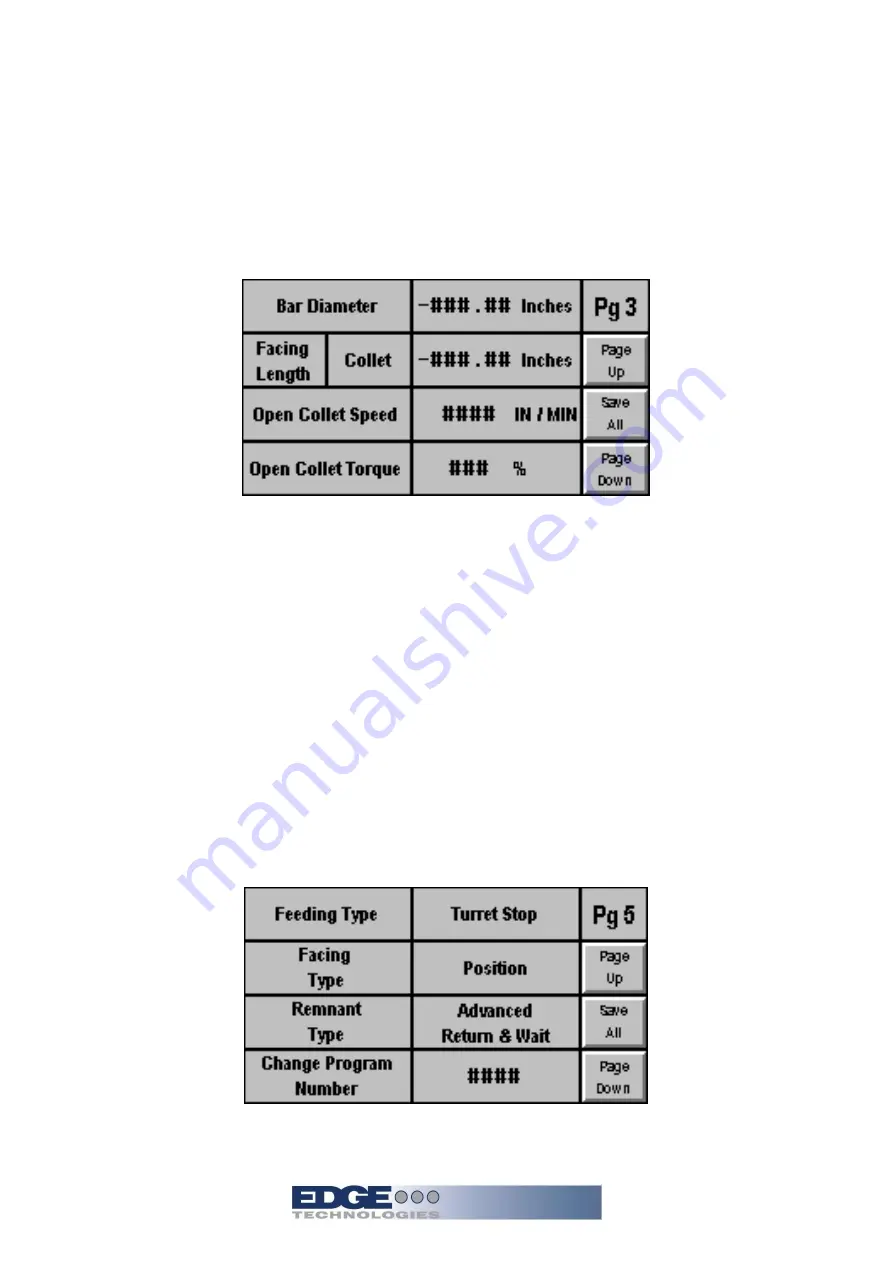
PATRIOT
338/551
112
REV 10:2019
Check 1st Part:
This parameter allows the long and short feed safety values to be disabled on
the first part after switching the bar feeder to Automatic mode or for the first part after a bar
change.
4. Press the Back button to return to the previous page when finished with this page.
5. Press the page down button to access parameter Page 3.
Bar Diameter:
Enter the diameter of the bar stock to be run. For hexagonal and square stock
enter the diameter as measured across the points of the material.
Facing Length:
This parameter allows adjustment to the stopping position of the new bar at the
completion of a bar change. See section 8 for the complete description of the parameter.
Open Collet Speed:
This parameter allows adjustment to the feeding speed of the bar stock in
Automatic mode.
Open Collet Torque:
This parameter allows adjustment of the pushing force of the bar pusher
in the Automatic mode. The range is plus or minus 50% of the setting selected through the Bar
Diameter parameter.
6. Press the Page Down button to continue.
Feeding Type Selects the method of feeding. Selections allow feeding to a hard stop on the
lathe or feeding to a distance set by the Feedout parameters on parameter page 1.1.
Содержание Patriot 338
Страница 1: ...Patriot 338 551 OPERATIONS MANUAL OPERATIONS MANUAL Version 10...
Страница 52: ...PATRIOT 338 551 46 REV 10 2019...
Страница 56: ...PATRIOT 338 551 50 REV 10 2019...
Страница 69: ...PATRIOT 338 551 63 REV 10 2019 5 Systems and Adjustments 5 1 Bar feeder Component Locations...
Страница 92: ...PATRIOT 338 551 86 REV 10 2019 Channel set has been removed...
Страница 94: ...PATRIOT 338 551 88 REV 10 2019 The gripper assembly is designed to function with out any adjustments...
Страница 103: ...PATRIOT 338 551 97 REV 10 2019 5 18 Vibration Troubleshooting Check List...
Страница 172: ...PATRIOT 338 551 166 REV 10 2019...
Страница 179: ......
Страница 180: ......
Страница 181: ......
Страница 182: ......
Страница 183: ......
Страница 184: ......
Страница 185: ......
Страница 186: ......
Страница 187: ......
Страница 188: ......
Страница 189: ......
Страница 190: ......
Страница 191: ......
Страница 192: ......
Страница 193: ......
Страница 194: ......
Страница 195: ......
Страница 196: ......
Страница 197: ......
Страница 198: ......
Страница 199: ......
Страница 200: ......
Страница 201: ......
Страница 202: ......
Страница 203: ......
Страница 204: ......
Страница 205: ......
Страница 206: ......
Страница 207: ......
Страница 208: ......
Страница 209: ......
Страница 210: ......
Страница 211: ......
Страница 212: ......
Страница 213: ......
Страница 214: ......
Страница 215: ......
Страница 216: ......
Страница 217: ......
Страница 218: ......
Страница 219: ......
Страница 220: ......
Страница 221: ......
Страница 222: ......
Страница 223: ......
Страница 224: ......
Страница 225: ......
Страница 226: ......
Страница 227: ......
Страница 228: ......
Страница 229: ......
Страница 230: ......
Страница 231: ......
Страница 232: ......
Страница 233: ......
Страница 234: ......
Страница 235: ......
Страница 236: ......
Страница 237: ......
Страница 238: ......
Страница 239: ......
Страница 240: ......
Страница 241: ......
Страница 242: ......
Страница 243: ......
Страница 244: ......
Страница 245: ......
Страница 246: ......
Страница 247: ......
Страница 248: ......
Страница 249: ......
Страница 250: ......
Страница 251: ......
Страница 252: ......
Страница 253: ......
Страница 254: ......
Страница 255: ......
Страница 256: ......
Страница 257: ......
Страница 258: ......
Страница 259: ......
Страница 260: ......
Страница 261: ......
Страница 262: ......
Страница 263: ......
Страница 264: ......
Страница 265: ......
Страница 266: ......
Страница 267: ......
Страница 268: ......
Страница 269: ......
Страница 270: ......
Страница 271: ......