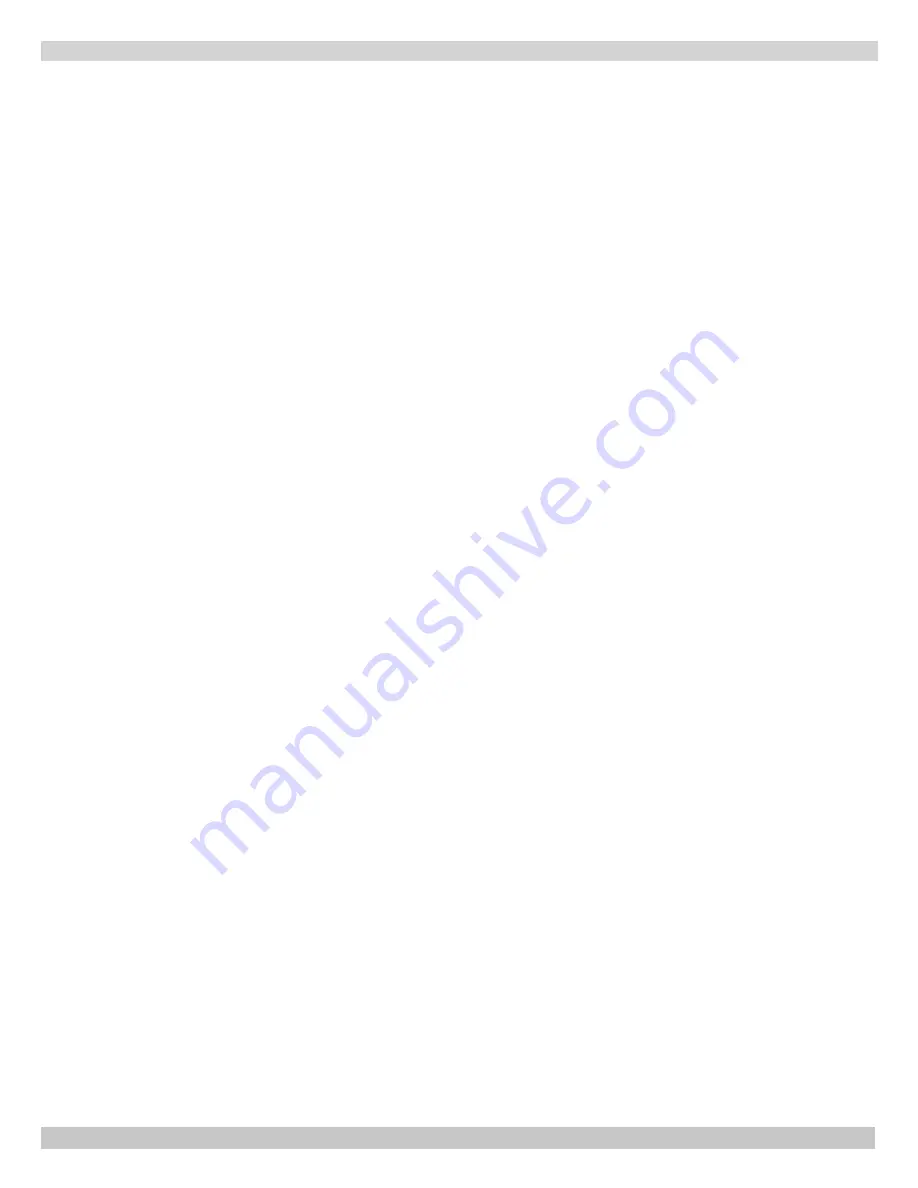
22
GENERAL MAINTENANCE
Low Water Cut-Off
Low Water Cut-Off interrupts electrical current to burner
when water line in boiler drops to low level.
Check Low Water Cut-Off monthly to verify it is providing
proper protection. See “Checking and Adjusting” on page
21.
Remove Low Water Cut-Off probes beginning of each
heating season for inspection and cleaning. More cleaning
may be required on boilers requiring frequent additions of
make up water.
Boiler Flue Passages and Burners
Beginning of heating season visually check pilot and main
burner flames. See page 19.
Recommend you have flue passages, burner adjustment,
and operation of controls checked once each year by
trained Service Technician.
Before start of each season or whenever system has been
shut down for some time, check system, boiler and vent
pipe for leaks.
Vent Pipe
Check vent piping at lease once a season. Verify vent pipe
connections to chimney are secure and no obstructions
are present. If vent piping shows sign of leaking, replace it
immediately.
Safety Valve
See Manufacturer's Instructions.
Cleaning Boiler Flue Passages and Burners
1. Remove burners, pilot, vent pipe, top and front jacket
panels. Remove hold-down nuts and bolts from flue
collector.
2. Use putty knife to cut through silicone. Lift flue collector
off boiler sections. Remove old silicone material.
3. Clean passageways between sections with flue brush.
Remove dirt from bottom of boiler and from between
sections by vacuuming.
4. Verify all flame ports in burners are open and clear.
Shake or blow out loose dirt in burners.
5. Apply generous bead of 400°F RTV silicone to four
mounting surface flanges of flue collector. Mount flue
collector on heat exchanger. Tighten nuts and bolts.
6. Seal front edge and four corners of flue collector to
heat exchanger with silicone sealant.
7. Use flashlight to verify there are no gaps in silicone
seal.
8. Install draft diverter, vent damper, vent pipe, and
jacket top and front cover.
9. Reassemble all parts.
10. Check tightness of pilot connections and condition of
burner flames after reassembly. See Figures 14 and 15.
Boiler Water Treatment Other Than Cleaners
In steam systems where system is tight, free from leaks,
and all steam is returned to boiler as condensate, amount
of make up water is small. Water treatment is generally not
required.
In steam systems with less than 90% of steam being
returned as condensate, or with very hard or corrosive
make up water, treatment may be desirable. Follow
recommendations of your local boiler water treatment
specialist.
Foaming, Priming, or Surging
These terms are used to describe a fluctuating water line
when water leaves boiler with steam. It is caused by any
combination of following:
1. Threading oil and organic matter in boiler water. Follow
instructions under “Start-up Cleaning.”
2.
Faulty quick vents that do not release air until sizeable
pressure is built up - if old style, replace - if dirty, clean
until you can easily blow through valve.
3.
Adjustment of steam limit control to wide differential
increases difficulty if quick vents are old style, slow-
releasing type or dirty. Always set steam limit control
differential as low as possible.
4.
Soap and chemicals in boiler water cause extreme
surging. Boiler cleaners and chemical cleaning additives
are not recommended. If used and not rinsed properly,
may be harmful to the system.
Содержание Dunkirk Plymouth Steam PSB-3D
Страница 9: ...9 Figure 4 Recommended Near Boiler Piping Using One Supply Tapping SYSTEM PIPING ...
Страница 27: ...27 REPAIR PARTS ...
Страница 28: ...28 REPAIR PARTS ...
Страница 29: ...29 REPAIR PARTS ...
Страница 30: ...30 REPAIR PARTS Safety Relief Valve 14 11 NPT X 4 Nipple PF 033 02 ...
Страница 31: ...31 Date Service Performed Company Name Tech Initials Company Address Phone ...
Страница 32: ...DUNKIRK BOILERS 2201 Dwyer Avenue Utica NY 13501 web site www ecrinternational com ...