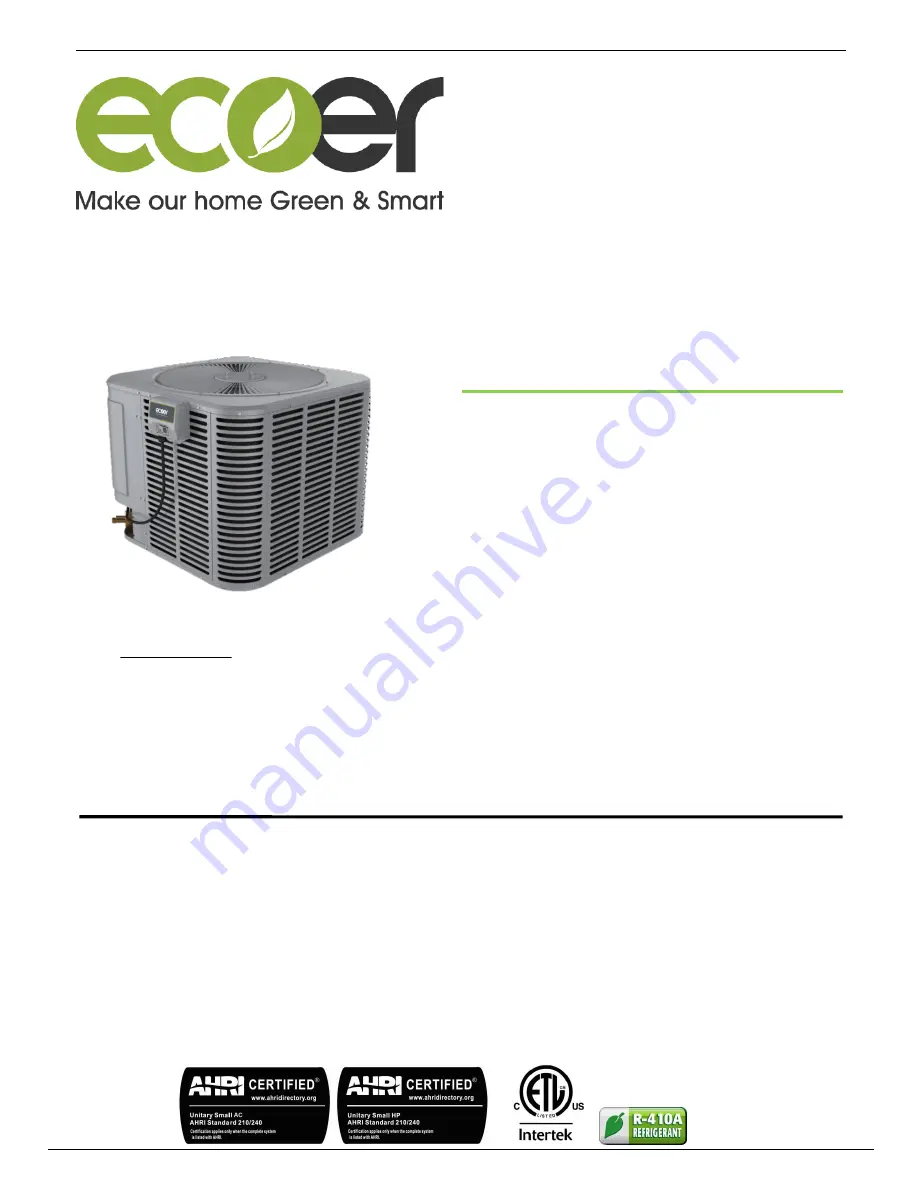
1/61
ESI Outdoor Unit Installation Instruction
05.2018
Manufacturer reserves the right to change at any time for specifications or designs without notice and incurring obligations.
NOTE: Appearance of unit may vary.
The IoT gateway does not ship with outdoor unit.
Visit www.ecoer.com to obtain the documents for
IoT installation instructions.
Installation must be performed in accordance with
the requirements of NEC and CEC by authorized
personnel only.
Installation Instructions
Split System Heat Pump
Up to 20 SEER
2-3-4-5Ton Capacity
R410A
Contents
1. Safety--------------------------------------------------
2. Unit Location Considerations--------------------
3. Position the Unit--------------------------------------
4. Refrigerant Pipe Considerations-----------------
5. Refrigerant Pipe Routing--------------------------
6. Refrigerant Pipe Brazing---------------------------
7. Refrigerant System Leak Check-----------------
8. Evacuation--------------------------------------------
9. Service Valves---------------------------------------
10. Electrical - Low Voltage----------------------------
11. Electrical - High Voltage---------------------------
12. Start Up------------------------------------------------
13. System Charge Adjustment----------------------
14. System Operation----------------------------------
15. Troubleshooting-----------------------------------------
2
4
6
7
9
10
11
11
12
13
14
15
16
20
29
All phases of this installation must comply with National, State and Local Codes.
IMPORTANT
This document is customer’s property and is to remain with this unit. Please return it to customer
with service information upon completion of work.
These instructions do not cover all variations in systems or provide for every possible contingency
to be met in connection with the installation.
Should further information be desired or should particular problems arise which are not covered
sufficiently for the purchaser’s purposes, the matter should be referred to your installing dealer or
local distributor.