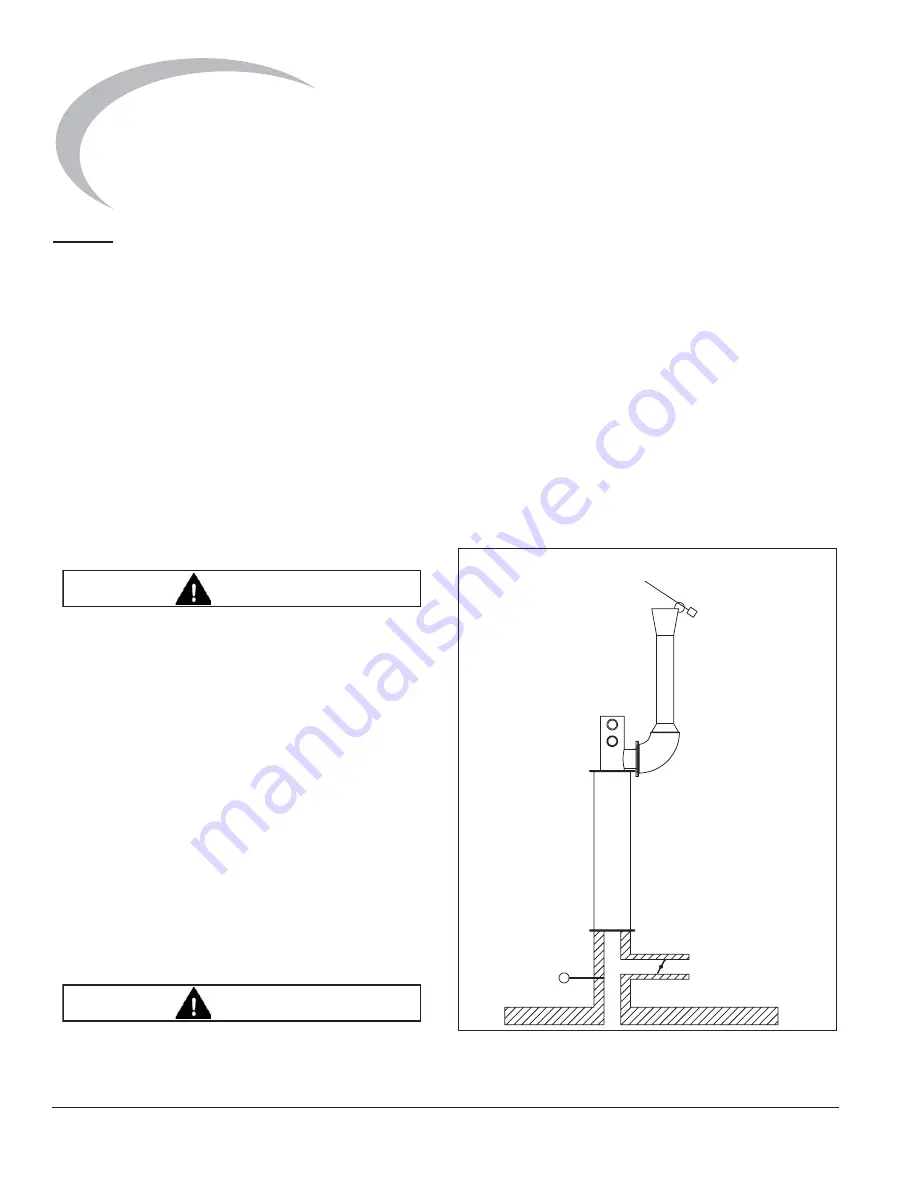
Eclipse Extern-A-Therm Recuperators, Design Guide 540, 3/9/2009
6
Design
Furnace Temperature Limits
Up to 1800°F -
No special safeguards are required to
protect the recuperator. See “Special Precautions for
Aluminum Melting or Holding” on this page, for aluminum
applications.
1800°F - 2100°F -
To ensure that the safe operating
temperature of the recuperator tubes is not exceeded, air
flow must not fall below the following limits:
• Model 300 MA - 90 scfh
• Model 600 MA - 180 scfh
• Model 1500 MA - 450 scfh
• Model 2500 MA - 750 scfh
The recuperator must be positioned so that it will not be
exposed to direct radiation from the furnace. This is to
protect the recuperator during shut down or power failure.
Ŷ
When shutting a process down, air must be
supplied to the exchanger until the exhaust inlet
temperature falls below 1800°F.
2100°F - 2400°F -
Dilution air must be introduced to the air
stream to maintain exhaust temperature below 2100°F.
(See Figure 3.4.) The amount of dilution air can be
determined from the “Dilution Air” section, page 7. When
using dilution air do not operate with excess fuel, either
gas or oil. The resulting fire would destroy the recuperator.
A high temperature protection limit switch must be fitted to
ensure flue temperatures do not exceed 2100°F.
The recuperator must be positioned so that it will not be
exposed to direct radiation from the furnace. This is to
protect the recuperator during shutdown or power failure.
The low flow air requirements listed above must be
observed.
Ŷ
When shutting a process down, air must be
supplied to the exchanger until the exhaust inlet
temperature falls below 1800°F.
Flue Gas Restrictions
The recuperator must not be used with any chloride,
sulfide, potassium, sodium or lithium salts in the flue gas.
Special Precautions for Aluminum Melting or
Holding
If the recuperator is to be used on aluminum melting
furnaces where flux is used, special precautions must be
taken to protect the recuperator during the fluxing cycle.
When flux is being used, the exit of the eductor should be
closed off and a by-pass duct opened until the fluxing is
complete and no fluxing agents are present in the
exhaust. Closing the damper on the eductor will force the
eductor air back through the recuperator ensuring that no
contaminated exhaust gases enter the recuperator. See
Figure 3.1.
Figure 3.1.
CAUTION
CAUTION
Eductor d
am
per
to be closed
w
hen
f
luxin
g
Byp
a
ss d
am
per
to be open
w
hen
f
luxin
g
System Design
3