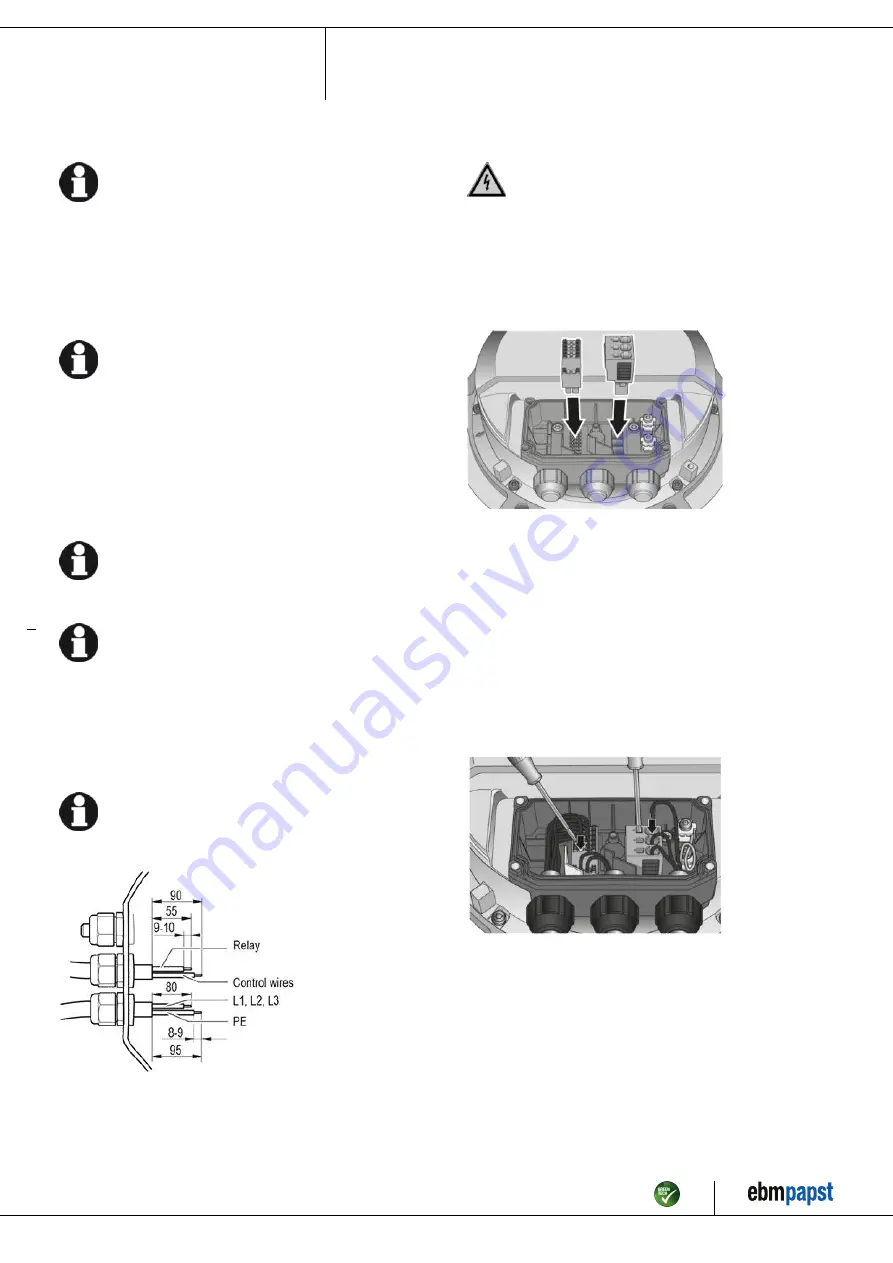
Operating instructions
K3G560-PB31-61
Translation of the original operating instructions
4.2.3 Reactive currents
Because of the EMC filter integrated for compliance with EMC
limits (interference emission and immunity to interference),
reactive currents can be measured in the supply line even
when the motor is at a standstill and the line voltage is switched
on.
●
The values are typically in the range < 500 mA.
●
At the same time, the effective power in this operating state
(operational readiness) is typically < 6 W.
4.2.4 Residual current circuit breaker (RCCB)
If the use of a residual current device (RCD) is required in your
installation, only AC/DC-sensitive residual current devices
(type B or B+) are permissible. As with variable frequency
drives, residual current devices cannot provide personal safety
while operating the device. When the device power supply is
switched on, pulsed charging currents from the capacitors in the
integrated EMC filter can lead to the instant tripping of residual
current devices. We recommend the use of residual current
circuit breakers (RCCB) with a trip threshold of 300 mA and
delayed tripping (super-resistant, characteristic K).
4.2.5 Leakage current
For asymmetrical power systems or if a phase fails, the
leakage current can increase to a multiple of the nominal value.
4.2.6 Locked-rotor protection
Due to the locked-rotor protection, the starting current (LRA) is
equal to or less than the nominal current (FLA).
4.3 Connection in terminal box
4.3.1 Preparing cables for connection
Only strip the cable as far as necessary, ensuring that the cable gland is
sealed and there is no strain on the connections. For tightening torques,
see Chapter 3.1 Product drawing.
NOTE
Tightness and strain relief are dependent on the cable
used.
→ This must be checked by the user.
Fig. 2: Recommended stripped lengths in mm (inside terminal box)
4.3.2 Connect cables to terminals
WARNING
Live terminals and connections even with device
switched off
Electric shock
→ Wait five minutes after disconnecting the voltage at all poles
before opening the device.
;
Open the terminal box.
;
Remove the cap from the cable gland.
;
Only remove caps where cables are fed in.
Fig. 3: Fit the connectors in the terminal box
;
Fit the cable glands with the seals provided in the terminal box.
;
Route the cable(s) (not included in the scope of delivery) into the
terminal box.
;
Ensure separate routing of the supply cable(s) and the cables for
status contact and control interface. Depending on the requirements for
the end device, the physical separation of these cables in the terminal
box may be mandatory. Use the partitions inside the terminal box as
an aid to routing for this purpose.
;
First connect the protective earth "PE".
;
Connect the cables to the corresponding terminals. Use a
screwdriver to do so. When connecting, make sure the wires do not
splay out. Insert the strands until they meet with resistance.
Fig. 4: Connection of cables at terminals
;
There must not be any tensile stress between the terminal and the
cable gland. The cable must be provided with strain relief.
;
The cable glands must be tight.
;
Fit the terminal box cover, making sure that the sealing surfaces are
clean.
;
Screw in the four screws (for tightening torque, see Chapter 3.1
Product drawing).
Item no. 56891-5-9970 · ENU · Change 200264 · Approved 2019-02-08 · Page 8 / 16
ebm-papst Mulfingen GmbH & Co. KG · Bachmühle 2 · D-74673 Mulfingen · Phone +49 (0) 7938 81-0 · Fax +49 (0) 7938 81-110 · [email protected] · www.ebmpapst.com