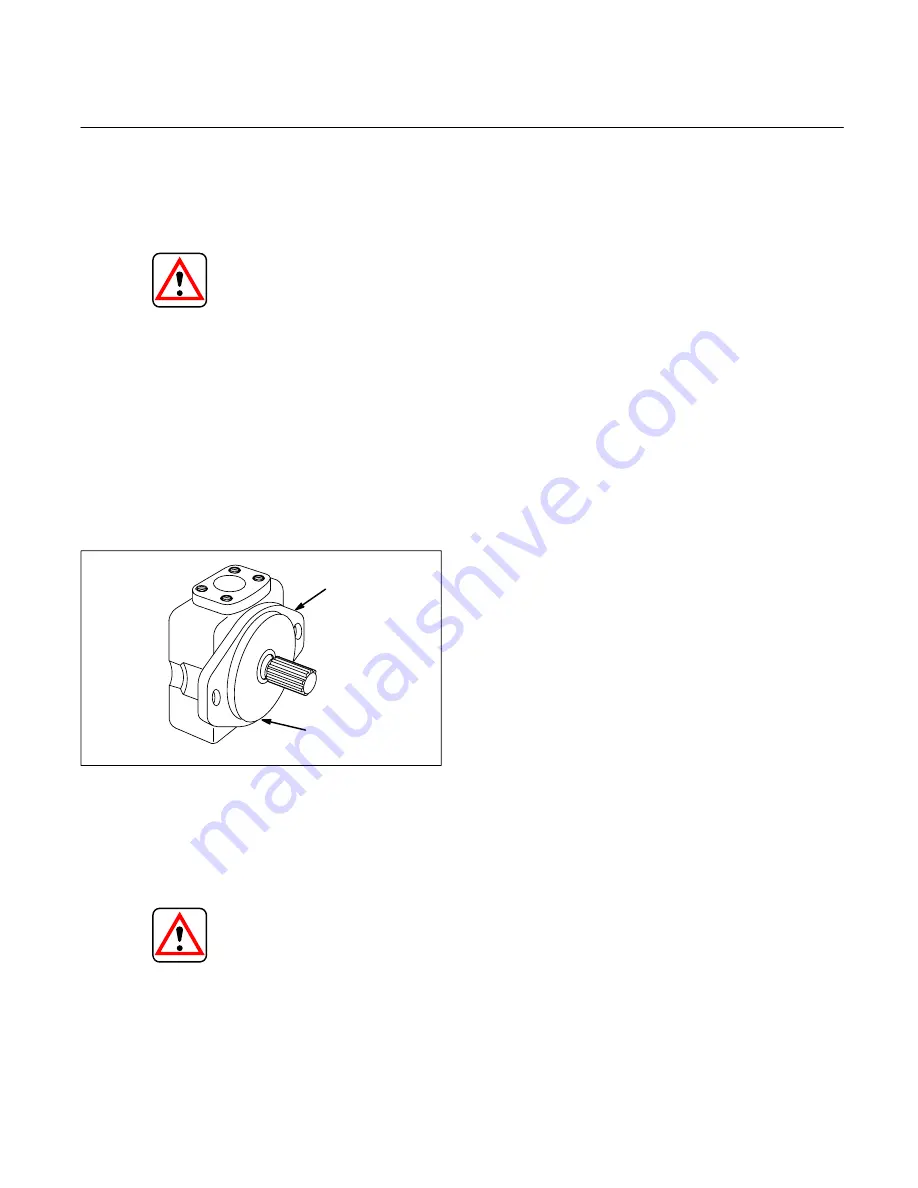
5
Section IV – Installation and Operating Instructions
A. Installation Drawings
The installation drawings listed in Table 1 show operating
characteristics, installation dimensions and port locations.
B. Mounting and Drive Connections
CAUTION
Pump shafts are designed to be installed in
couplings with a slip fit. Pounding can injure the
bearings. Shaft tolerances are shown on the
installation drawing (Table 1).
1. Direct Mounting – A pilot on the pump mounting
flange (Figure 3) assures correct mounting and shaft
alignment. Make sure the pilot is firmly seated in the
accessory pad of the power source. Care should be
exercised in tightening the mounting screws to prevent
misalignment.
2. Indirect drive is not recommended for these pumps
without Vickers engineering approval.
Pilot
Flange
Figure 3. Mounting flange and pilot
C. Shaft Rotation
Pumps are assembled for either right hand (clockwise) or left
hand (counterclockwise) shaft rotation as viewed from the
shaft end.
CAUTION
Never drive a pump in the wrong direction of
rotation. Seizure will result, necessitating
expensive repairs.
D. Piping and Tubing
1. All pipes and tubing must be thoroughly cleaned
before installation. Recommended methods of cleaning are
sand blasting, wire brushing, pickling and power flushing
with clean solvent to remove loose particles.
NOTE
For information on pickling, refer to instruction
sheet 1221-S.
2. To minimize flow resistance and the possibility of
leakage, only as many fittings and connections as are
necessary for proper installation should be used.
3. The number of bends in tubing should be kept to a
minimum to prevent excessive turbulence and friction of oil
flow. Tubing must not be bent too sharply. The
recommended minimum radius for bends is three times the
inside diameter of the tube.
E. Hydraulic Fluid Recommendations
General Data
Fluid in a hydraulic system performs the dual function of
lubrication and transmission of power. It constitutes a vital
factor in a hydraulic system and careful selection of it should
be made with the assistance of a reputable supplier. Proper
selection of fluid assures satisfactory life and operation of
system components with particular emphasis on hydraulic
pumps. Any fluid selected for use with pumps is acceptable
for use with valves or motors.
Data sheet I-286 for fluid selection is available from Vickers
Technical Publications, Troy, Michigan 48084.
Fluid recommendations noted in the data sheet are based on
our experience in industry as a hydraulic component
manufacturer. Where special considerations indicate a need
to depart from the recommended fluids or operating
conditions, see your Vickers sales engineer.
Cleanliness
Thorough precautions should always be observed to insure
that hydraulic system is clean.
1. Clean (flush) entire new system to remove paint,
metal chips, welding shot, etc.
2. Filter each change of fluid to prevent introduction of
contaminants into the system.
3. Provide continuous filtration of fluid to remove sludge
and products of wear and corrosion generated during the life
of the system.
4. Provide continuous protection of system from entry of
airborne contamination by sealing the system and/or by
proper filtration of the air.
5. During usage, proper fluid filling and servicing of
filters, breathers, reservoirs, etc., cannot be over
emphasized.
6. Thorough precautions should be taken by proper
system and reservoir design to insure that aeration of the
fluid will be kept to a minimum.