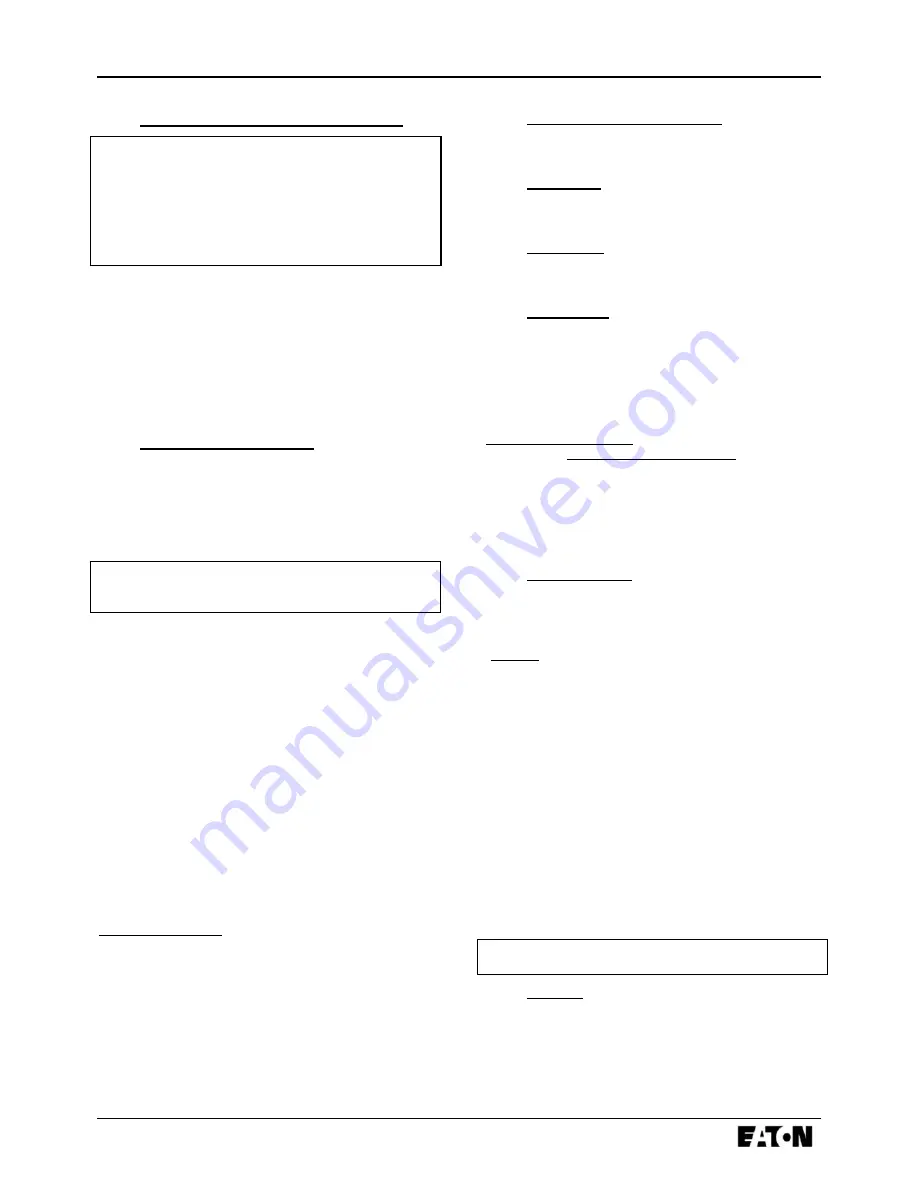
IM05805001K
9
Effective November 2003
6.
Programming of the Main Controller
NOTE:
The controller can NOT be programmed when the
motor is running. When programming, the
LMR
does not
control the system. If the programming of the unit is ignored
for one (1) minute, the controller will return to the automatic
mode and will start the motor should it detect a start signal.
Otherwise, the programming mode can be exited by selecting
“Return to Auto Mode” on the LCD display or pushing the
RESET key at any time.
The LCD display will prompt the programmer with data
and allow the operator to modify the program using a
combination of the ‘UP ARROW’, ‘DOWN ARROW’,
‘ACK/ALARM’ and ‘MENU’ keys.
See Figure 4.
The displayed parameter value indicates the present setting
|of the controller. Located above the UP ARROW, DOWN
ARROW and ACK./ALARM keys are designated symbols
and/or words describing their function. These keys are used
to increase, decrease or accept programmed values.
6.1 To Program the Controller
Ensure that the pump is NOT running. Press and hold the
‘MENU’ key, located on the bottom right hand corner of the
membrane faceplate, for 3 to 5 seconds. Once the “MENU
MODE CATEGORIES” message appears, press the
‘ACK./ALARM’ key. You are now ready to program
the controller.
NOTE:
While programming the
LMR
, pressing the RESET
button at any time will return you to the normal running
mode of the controller.
Refer to Figure 5, page 17, for the programming menu.
By following the drawing on page 217, you can move from
one parameter to the next by pressing the ‘MENU’ key.
Note that this does not affect the value of the parameter
currently displayed.
To change a parameter, press the ‘ACK/ALARM’ key.
The value can be increased, decreased or modified by use
of the UP ARROW and DOWN ARROW keys. Once set,
press ‘ACK/ALARM again to enter the displayed data
into memory.
For example, if the parameter displayed is ‘CHANGE
DATE’, press ‘MENU’ key three times to access the ‘RUN
PERIOD TIMER’ parameter. Press ‘ACK/ALARM’ to
change the RPT time and UP ARROW or DOWN ARROW
to increase or decrease the value. Pressing ‘ACK/ALARM’
again will enter the selected value into memory and proceeds
to the next parameter.
Programmable Ranges
Pressure (Stop/Start):
0-600 PSI
Pressure Deviation:
0-50 PSI
Run Period Timer:
0-45 minutes
Sequential Start Timer:
0-300 seconds
Acceleration Timer:
0-15 seconds
Weekly Test Timer
1-52 weeks
Overvoltage: 5-20
%
Undervoltage: 5-30
%
Low Suction Shutdown
Enabled or Disabled
6.2 PROGRAM DESCRIPTIONS
Refer to the ‘
LMR
PROGRAMMING MENU’ affixed inside
the enclosure door and/or Figure 5, page 17.
6.2.1 Change
Date
Factory set, however, this parameter allows the user to set
the current date.
6.2.2 Change
Time
Factory set, however, this parameter allows the user to set
the current time.
6.2.3 Weekly
Timer
For software versions up to and including V2.4, this function
allows the user to set the controller to automatically start
and stop the engine once per week. Select the day and time
(24-hour clock) for this parameter to function. Once selected,
choose the run time desired, in minutes. The pump will now
start once per week as programmed.
For software versions V2.5 and greater, the weekly timer is
selected as the number of weeks between tests.
You can view the status of the Weekly Test date by depress-
ing the TIME/PRINT button twice. If an ‘*’ appears on the
display, the test will take place that week.
If you wish NOT to exercise the motor, change the “Day”
setting to ‘NONE’.
6.2.4 Run Period Timer
(Not available on Foam Pump Controllers – see section 15.2
of this manual)
To activate the RPT, the MANUAL STOP function must be
‘Disabled’ (see below in this section). When the motor is
started in response to the pressure switch, it will continue to
run for the duration of the RPT, in minutes. Once timed out,
if no further starting causes prevail, the motor will
automatically stop.
If the STOP pushbutton is depressed at any time during the
timing of the RPT, the motor will stop and the RPT will reset
to zero. Upon releasing the STOP pushbutton, if a starting
cause is prevalent, the motor will restart.
If the motor is started manually, either by the start push-
button or emergency handle, the RPT has no affect and the
motor must be stopped manually.
If the MANUAL STOP function is ‘Enabled’, the RPT
does not affect the operation of the controller and
becomes inoperative.
The timing range for the RPT is:
0-45 minutes
NOTE:
The RPT timer must be reset to ten (10) minutes
when the controller is placed in service.
6.2.5 Language
The language can be selected for English, French or Spanish.
Future Enhanced versions will include additional languages.
Содержание Cutler-Hammer LMR
Страница 2: ...Effective November 2003 ...
Страница 6: ......
Страница 20: ...14 IM05805001K Effective November 2003 8 FIGURE 1 MAIN TERMINAL BLOCK TB1 9 FIGURE 2 RELAY CARD ...
Страница 21: ...IM05805001K 15 Effective November 2003 10 FIGURE 3 TYPICAL SCHEMATIC ...
Страница 22: ...16 IM05805001K Effective November 2003 11 FIGURE 4 MAIN DISPLAY PANEL 12 TABLE 1 POWER WIRE CABLE REFERENCE ...
Страница 23: ...IM05805001K 17 Effective November 2003 13 FIGURE 5 LMR PROGRAMMING MENU ...
Страница 27: ...IM05805001K 21 Effective November 2003 18 FIGURE 7 FDF SCHEMATIC ...
Страница 28: ...22 IM05805001K Effective November 2003 19 FIGURE 8 FDF MAIN TERMINAL BLOCK TB1 20 FIGURE 9 FDF RELAY CARD ...
Страница 30: ...24 IM05805001K Effective November 2003 22 FIGURE 10 FDM MEDIUM VOLTAGE DIMENSIONS ...
Страница 31: ...IM05805001K 25 Effective November 2003 23 FIGURE 11 FDM SCHEMATIC ...
Страница 32: ...26 IM05805001K Effective November 2003 24 FIGURE 12 FDM MAIN TERMINAL BLOCK TB1 25 FIGURE 13 FDM RELAY CARD ...
Страница 37: ...IM05805001K 31 Effective November 2003 ...