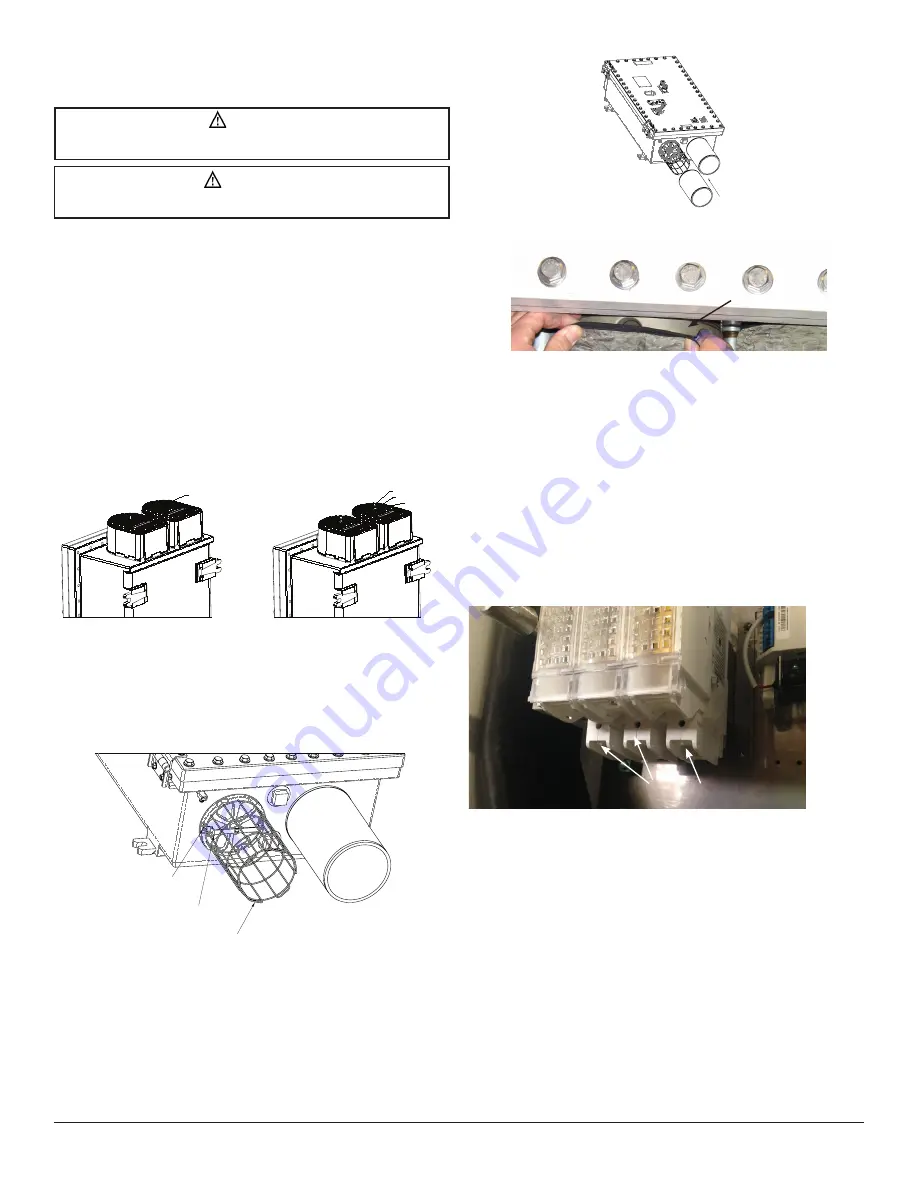
IF 1619 • 05/18 Copyright
©
2018, Eaton’s Crouse-Hinds Division Page 6
3. ELECTRICAL INSTALLATION
3.1 ENCLOSURE GROUNDING - INTERNAL/EXTERNAL
Grounding and bonding of the conduit and equipment is required by the National
Electrical Code. A grounding conductor must be connected to the grounding lug(s)
furnished.
Determine the type of distribution systems to be used that will comply with NEC
requirements and ensure grounding continuity.
All conductive equipment that enclose the electrical conductors or attached
equipment or forming part of such equipment must be grounded. A permanent
connection must be made between all such equipment and the earth. Refer to
Section 5.3 for the torque requirements of all terminations within this device.
This equipment is designed for line connection directly to the integral disconnect
switch. Factory wiring transmits power to the variable frequency drive.
1. Attach line conductors with phase A on the left, B center and C to the right
(see torque table on page 9).
3.3 LOAD FEED AND SHIELD GROUNDING TO DRIVE
This equipment is designed for load connection directly from the variable frequency
drive, although, in the case of an oversized VFD for the given motor, use the VFD
and motor manufacturer’s recommendations for proper motor overload protection.
In certain cases, it is required to include additional motor overload protection
between the VFD and the motor for proper motor overload protection. Always be
sure to shield load wiring from line and control wiring to reduce noise. Refer to the
drive manufacturer’s manual for further details.
1.
Remove VFD terminal shroud.
2.
Attach load conductors with phase A to U2, B to V2, and C to W2 (see torque
table on page 9).
3.
Attach motor cable shielding to VFD ground (see recommendations by drive
manufacturer).
4.
Remove terminal knockouts and reinstall VFD terminal shroud. Refer to
the drive manufacturer’s manual for further information regarding drive
installation.
2.7 PRE-FILTER INSTALLATION
3.2 LINE FEED
2.5 MOUNTING
1. Select a mounting location that will provide suitable strength, rigidity and space
(per Section 2.1) for supporting the ACE system and all contained wiring.
2. Refer to Section 2.2 for approximate weights and Section 2.4 for dimensions.
3. Install two (2) 5/8” bolts on left side.
4. Tap each of the four (4) mounting feet with a mallet to ensure tight assembly.
5. Align enclosure with the two (2) left side mounting feet engaged with the
mounting bolts on selected mounting surface.
6. Tighten two (2) bolts on left side.
7. Install two (2) 5/8” bolts on right side and tighten.
8. After enclosure is positioned and secured in its permanent location, pull wires
into the ACE system, making sure that they are long enough to make the
required connections.
CAUTION
To avoid cooling system malfunction, cooling system failure and personnel
injury, be sure to mount the enclosure as depicted in Section 2.4.
Disconnect terminal shrouds
1. Remove rubber caps from explosionproof filters.
2. Install wire guard using the bracket, screw and lock washer provided to the
bottom filter(s).
3. Align guard with notches within the bracket as shown.
4. Tighten screw.
5. Slip pre-filter mesh over guard.
CAUTION
To avoid cooling system malfunction, cooling system failure and personnel
injury, be sure to mount the enclosure in a shaded area to avoid direct sunlight.
2.6 SHROUD INSTALLATION
Explosionproof
filter
1. Remove rubber caps from explosionproof filters.
2. Insert threaded rods into the explosionproof filters. Leave 3-5/8 of threaded
rod exposed.
3. Place shroud over explosionproof filters and threaded rod, with shroud opening
facing back of enclosure. See Figure 2.
4. Insert washer and nuts onto end of threaded rod and tighten securely until
shroud is firmly contacting the top wall of the enclosure. See Figure 3.
6. Be sure to stretch pre-filter elastic band completely around the explosionproof
filter and seat the elastic band on the filter’s threads. This will ensure all air
flow to the bottom filters passes through the pre-filters.
THREADED STUD
Figure 2
ACORN NUT
LOCKING NUT
WASHER
Figure 3
NOTCH
BRACKET
GUARD
Detailed view