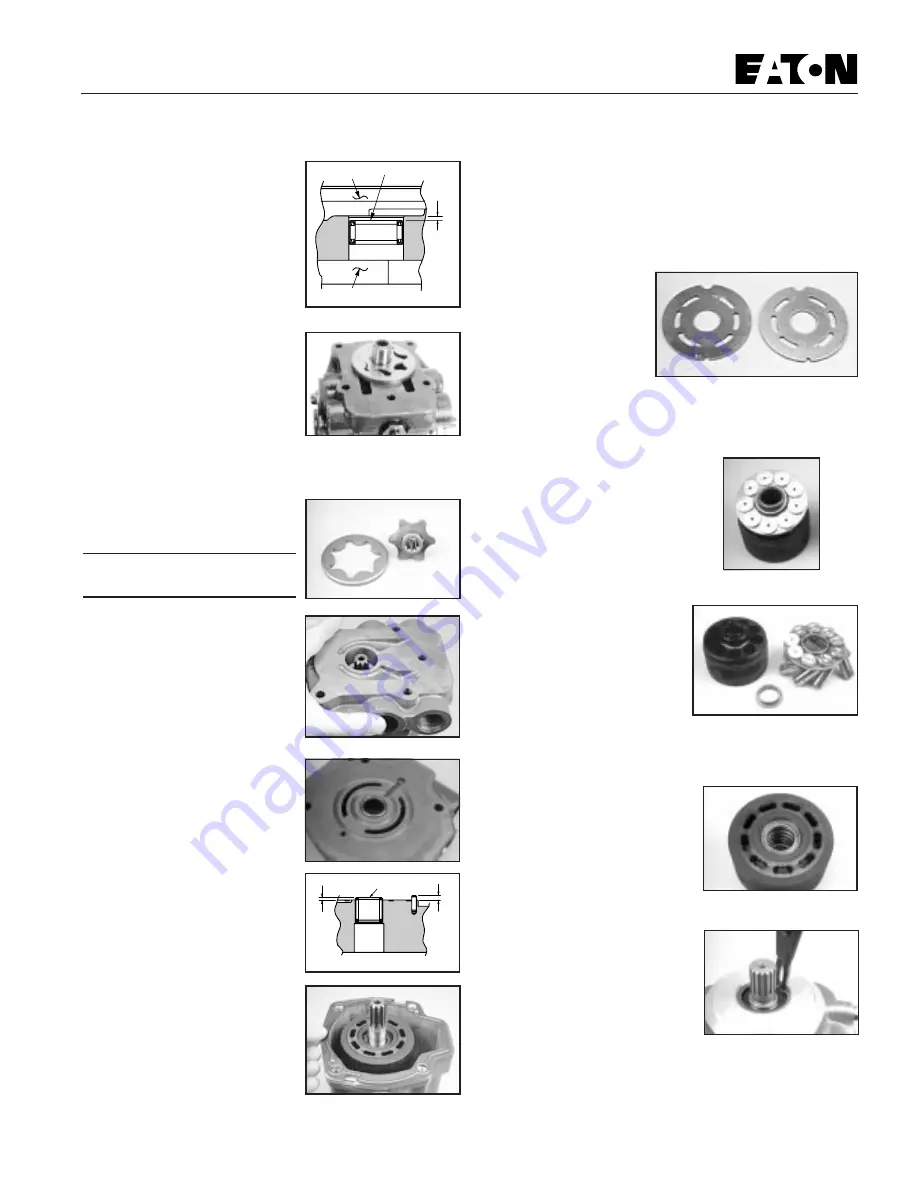
9
Model 70160
13 When the needle bearing
assembly is replaced, the
numbered end of the bearing must
face toward the flange side of the
adapter to the dimension as shown
(see Figure 13).
14 With the charge pump adapter
removed, remove the charge pump
outerring and inner gerotor ring
assembly (see Figure 14 and 15).
15 Charge pumps are available in
two different displacements Charge
pump displacements are based on
the thickness of the gerotor
assembly and the depth of the
pocket located in the charge pump adapter. To determine the
displacement, refer to the table below.
Gerotor Pocket Depth
Displacement
Depth of Pocket
cm
3
/r [in
3
/r]
mm [in.]
6.9 [.42]
6.35 [.25]
13.8 [.84]
12.7 [.50]
16 To separate the endcover
assembly from the dowel pins in
the pump housing assembly, insert
two screwdrivers between
endcover and housing assembly
and pry upward (see Figure 16).
17 After separation, remove the
endcover from the housing
assembly.
18 Turn the endcover assembly
over and inspect the needle
bearing. The needles in the needle
bearing must remain intact in the
bearing cage (see Figure 17).
19 When the needle bearing
assembly is replaced, the
numbered end of the bearing must
face the valve plate side of the
endcover to the dimension as
shown (see Figure 18).
20 With the endcover removed,
remove the gasket from the pump
housing assembly and discard (see
Figure 19).
21 Remove the valve plate from the piston block assembly.
Note: This valve plate may have stuck to the endcover
assembly that was previously removed.
22 Valveplate directional rotation (CW or CCW) is identified
by the location of the metering slots located on the face of the
valve plates. Pump input
rotation should always turn
into the metering slots (see
Figure 20). A clockwise
valve plate is shown on the
left and a counter clockwise
valveplate is on the right.
Note: Whenever pump
input rotation is changed, the valve plate must be replaced
along with the desired rotation charge pump adapter.
23 Remove the rotating kit assembly
by carefully retaining it in the housing
assembly (see Figure 21). Lift the
housing and rotating kit assembly and
turn over assemblies allowing the
rotating kit assembly to slide down the
input shaft and out of the pump
housing.
24 With the rotating kit
assembly removed, remove the
piston assemblies, spider and
spider pivot from the piston
barrel.(see Figure 22).
25 Inspect the piston
assemblies, spider, spider pivot
and piston block. The piston block assembly usually requires
no further disassembly unless the pins or block spring are
damaged.
26 When any excessive wear or
scratches are noted on the face of
the piston block, the block
assembly must be replaced (see
Figure 23).
DO NOT LAP THE FACE OF PISTON
BLOCK ASSEMBLY.
27 To remove the input shaft
assembly, use a pair of internal
snap ring pliers and remove the
shaft seal retaining ring from the
housing assembly (see Figure 24).
Numbered End
Gerotor Pocket
2.41 mm
[.095 in.]
Flange
Figure 13
Figure 17
2.79 mm
[.110 in.]
1.91 mm
[.075 in.]
Numbered End
Figure 18
Figure 20
Figure 22
Figure 23
Figure 24
Figure 15
Figure 16
Figure 14
Figure 19
Figure 21
Repair Information
- Disassembly