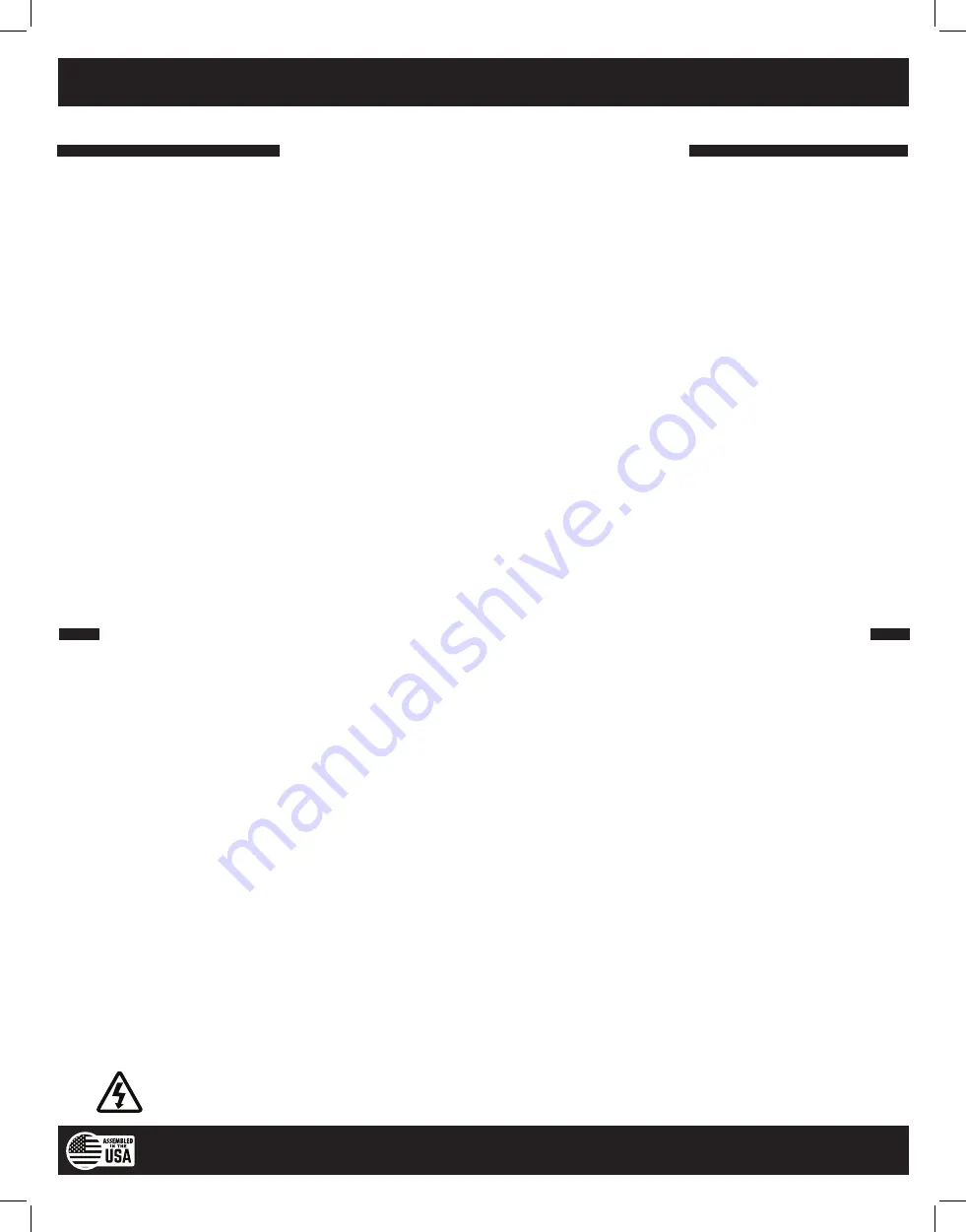
SELF-PRIMING EXTERNAL PUMPS
The All-In-One Pump
© 2023 EasyPro, Inc
Pg. 5
PUMP DISASSEMBLY
Disassembly and repair of the motor sub-assembly can be made as follows:
1. Disconnect the pump from the power source by unplugging or turn off at the circuit breaker.
2. Close all necessary valves on inlet and discharge lines and drain the pump by removing both drain plugs.
3. Loosen and remove the six (6) 1-1/8” hex bolts that hold the volute and the bracket together.
4. Pull the rear sub-assembly away from the volute. The volute may remain attached to the plumbing.
5. Loosen and remove the two (2) diffuser set screws that hold the diffuser to the bracket.
6. Remove the set screw from the impeller eye, if present. To remove, hold the impeller stationary and turn the set screw clockwise
to loosen (screw is left-hand threaded).
7. Hold the motor shaft stationary by removing the cap on the opposite end of the motor and inserting a screw driver in the slot,
or a wrench on the flat spot on the motor shaft depending on the motor design and unscrew the impeller by turning it counter clockwise.
8. Loosen and remove the four (4) 7/8” hex-bolts that hold the bracket to the motor face.
9. To remove the shaft seal, place the bracket face down on a flat surface and press out the
carbon/spring seal from the back side. Never pry it out from the front. Carefully remove the ceramic seal from the back of the impeller hub
by carefully prying up with a small flathead screw driver.
10. Clean the bracket, seal bore housing and the motor shaft as necessary. Remove slinger if replacing bearings.
All moving parts are located in the rear sub-assembly of this pump. Tools required:
3/32" Allen wrench • 7/16" open end wrench • 9/16" open end wrench • Small and large flathead screwdrivers • #3 Phillips screw driver
PUMP ASSEMBLY / PARTS REPLACEMENT
1. To install a new shaft seal, clean or replace the bracket bore O-ring. Moisten bracket bore O-ring with water prior to installing to prevent rolling.
2. Press the seal into the bore without touching or putting pressure on the delicate carbon face by pushing on the stainless steel collar.
(A large socket or pipe nipple may be used to facilitate installation.)
3. Clean as necessary the impeller hub and press in the ceramic part, making sure the polished white ceramic face is sitting flat and is facing out
and not the rubber boot.
NOTE:
Handle the mechanical seal with care to protect the polished and lapped faces of the seam from damage.
Tip: Moistening the rubber boot with water prior to installation aids in proper seating.
4. Install the slinger rubber washer on the motor shaft. Install the bracket to the motor. Install and tighten the four (4) 7/8” hex bolts.
5. Screw the impeller clockwise onto the motor shaft while holding the motor shaft stationary until it makes firm contact.
6. Mount the diffuser onto the bracket fitting the plastic pins into the holes in the bracket, then tighten both diffuser set screws.
7. Make sure the diffuser O-ring and bracket gasket are clean and properly seated.
8. Assemble the motor sub-assembly to the volute using the six (6) 1-1/8” hex bolts. Do not tighten until all six (6) hex bolts are in place
and hand tightened, then tighten all six (6) bolts uniformly in an alternating opposing sides pattern.
9. Insert both drain plugs with O-rings installed and tighten. Install strainer basket and fill the volute (strainer pot) with water.
10. Reinstall the lid and clamp ring, turning clockwise until snug.
11. Open all valves on the system, if present, and reconnect the power to start. Wait for the pump to prime. Monitor water level in the volute basket
area to ensure water is always present. If the pump has been running with no incoming water flow for more than 15 minutes, shut the system off
immediately and call 800-448-3873 or email [email protected] for technical assistance.
WARNING:
DO NOT RUN THE PUMP DRY. The pump must be filled with water and sealed before it is turned on.