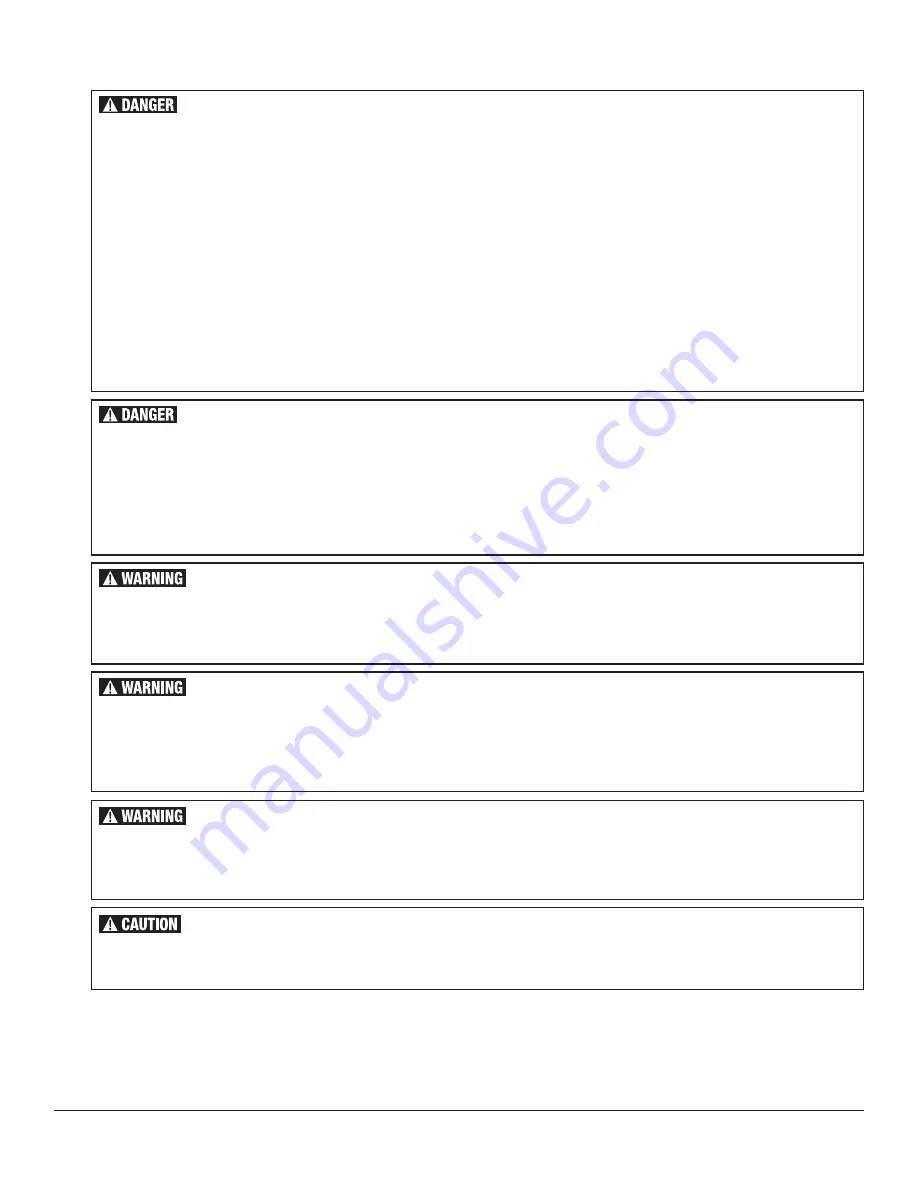
To order parts and supplies: 800.343.9353 >> eastwood.com
11
OPERATION
ELECTRIC SHOCK CAN CAUSE INJURY OR DEATH!
• Improper use of an electric Welder can cause electric shock, injury and death! Read all precautions described in the Welder
Manual to reduce the possibility of electric shock.
• Disconnect Welder from power supply before assembly, disassembly or maintenance of the torch, contact tip and when
installing or removing nozzles.
• Always wear dry, protective clothing and leather welding gloves and insulated footwear. Use suitable clothing made from
durable flame-resistant material to protect your skin.
• If other persons or pets are in the area of welding, use welding screens to protect bystanders from sparks.
• Always operate the Welder in a clean, dry, well ventilated area. Do not operate the Welder in humid, wet, rainy or poorly
ventilated areas.
• The electrode and work (or ground) circuits are electrically “hot” when the Welder is on. Do not allow these “hot” parts to come
in contact with your bare skin or wet clothing.
• Separate yourself from the welding circuit by using insulating mats to prevent contact from the work surface.
• Be sure that the work piece is properly supported and grounded prior to beginning an electric welding operation.
• Always attach the ground clamp to the piece to be welded and as close to the weld area as possible. This will give the least
resistance and best weld.
WELDING SPARKS CAN CAUSE FIRE OR EXPLOSION!
• Electric welding produces sparks which can be discharged considerable distances at high velocity igniting flammable
or exploding vapors and materials.
• Do not operate electric arc Welder in areas where flammable or explosive vapors are present.
• Do not use near combustible surfaces. Remove all flammable items within 35 feet of the welding area.
• Always keep a fire extinguisher nearby while welding.
• Use welding blankets to protect painted and or flammable surfaces; rubber weather-stripping, dash boards, engines, etc.
• Ensure power supply has properly rated wiring to handle power usage.
ELECTROMAGNETIC FIELDS CAN BE A HEALTH HAZARD!
• The electromagnetic field that is generated during arc welding may interfere with various electrical and electronic devices
such as cardiac pacemakers. Anyone using such devices should consult with their physician prior to performing any
electric welding operations.
• Exposure to electromagnetic fields while welding may have other health effects which are not known.
ARC RAYS CAN BURN!
• Arc rays produce intense ultraviolet radiation which can burn exposed skin and cause eye damage. Use a shield with the proper
filter (a minimum of #11) to protect your eyes from sparks and the rays of the arc when welding or when observing open arc
welding (see ANSI Z49.1 and Z87.1 for safety standards).
• Use suitable clothing made from durable flame-resistant material to protect your skin.
• If other persons or pets are in the area of welding, use welding screens to protect bystanders from sparks and arc rays.
FUMES AND WELDING GASES CAN BE A HEALTH HAZARD!
• Fumes and gasses released during welding are hazardous. Do not breathe fumes that are produced by the welding operation.
Wear an OSHA-approved respirator when welding.
• Always work in a properly ventilated area.
• Never weld coated materials including but not limited to: cadmium plated, galvanized, lead based paints.
HOT METAL AND TOOLS WILL BURN!
• Electric welding heats metal and tools to temperatures that will cause severe burns!
• Use protective, heat resistant gloves and clothing when using Eastwood or any other welding equipment.
Never touch welded work surface, torch tip or nozzle until they have completely cooled
Содержание MIG 175
Страница 1: ...MIG175 WELDER SERVICE MANUAL Item 12012...
Страница 16: ...16 Eastwood Technical Assistance 800 343 9353 tech eastwood com EXPLODED VIEW WITH PARTS LIST...
Страница 18: ...18 Eastwood Technical Assistance 800 343 9353 tech eastwood com NOTES...
Страница 19: ...To order parts and supplies 800 343 9353 eastwood com 19 NOTES...