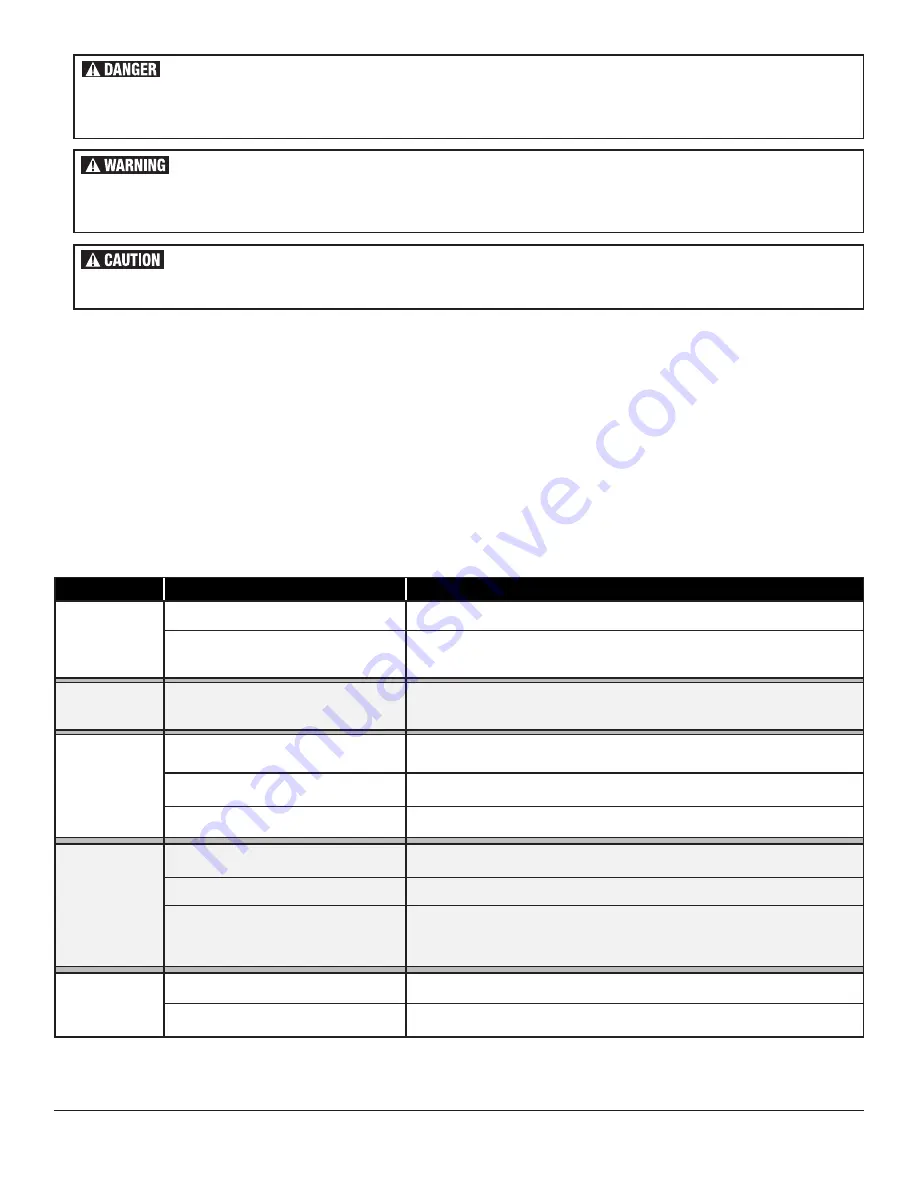
To order parts and supplies: 800.345.1178 >> eastwood.com
7
1.
While wearing a properly functioning Auto Darkening Welding Helmet, lightly
drag the tip of the Welding Rod along the workpiece surface to start an arc.
2.
Feed the Welding Rod into the workpiece joint at a 15° angle.
3.
Lift rod from workpiece when weld bead is completed.
4.
Turn off Welder power switch.
5.
Set the Electrode or “Stick” Holder on a safe, non-flammable, surface.
6.
In order to disable the “Hot Start” and “Anti-Stick” features of this welder while you are ARC welding, switch the Stick/TIG switch to TIG. This will keep
amperage at a steady rate and will help prevent blow-through when welding thinner material.
WELDING SPARKS CAN CAUSE FIRE OR EXPLOSION!
Electric welding produces sparks which can be discharged considerable distances at high velocity igniting flammable or exploding vapors
and materials. Remove all flammable items within 35 feet of the welding area. Always keep a fire extinguisher nearby while welding.
FUMES AND WELDING GASES CAN BE A HEALTH HAZARD!
Fumes and gasses released during welding are hazardous. Do not breathe fumes that are produced by the welding operation. Wear an OSHA-
approved respirator when welding. Always work in a properly ventilated area.
HOT METAL AND TOOLS WILL BURN!
Electric welding heats metal and tools to temperatures that will cause severe burns! Use protective, heat resistant gloves and clothing.
TROUBLESHOOTING
PROBLEM
CAUSE
CORRECTION
Contamination
in weld bead
Contaminated Electrode Rod
Make sure that Electrodes are clean and dry before use.
Contaminated Base Metal
Clean base metal of any oil, debris, coatings, or moisture. If base metal is cold
rolled steel make sure to remove any mill scale.
Poor Weld
Appearance
Incorrect positioning
The angle of the electrode should be at 45° and drug away from the weld arc.
Failing to do so may cause poor weld appearance.
Weld Bead is
Cracking
Too much heat in material
Reduce heat & allow more time between passes.
Base Metal is absorbing too much heat
Preheat base metal (consult welding codes for requirements)
Incorrect Filler Wire
Use correct filler wire type & diameter for the joint being welded.
Material is
Warping
Insufficient Clamping
Clamp work piece tightly & weld while clamps are in place.
Insufficient Tack Welds
Add more tack welds until rigidity and stiffness is developed.
Too Much Heat in Material
To reduce heat it is best to spread the welding out around the area. This can be
done by using stitch welding techniques, alternating sides, and/or taking your
time and allowing the pieces to cool between passes.
Porosity in
weld bead
Contaminated Electrode Rod
Make sure that Electrodes are clean and dry before use.
Contaminated base metal
Clean base metal making sure to remove any oil, debris, coatings, or moisture.