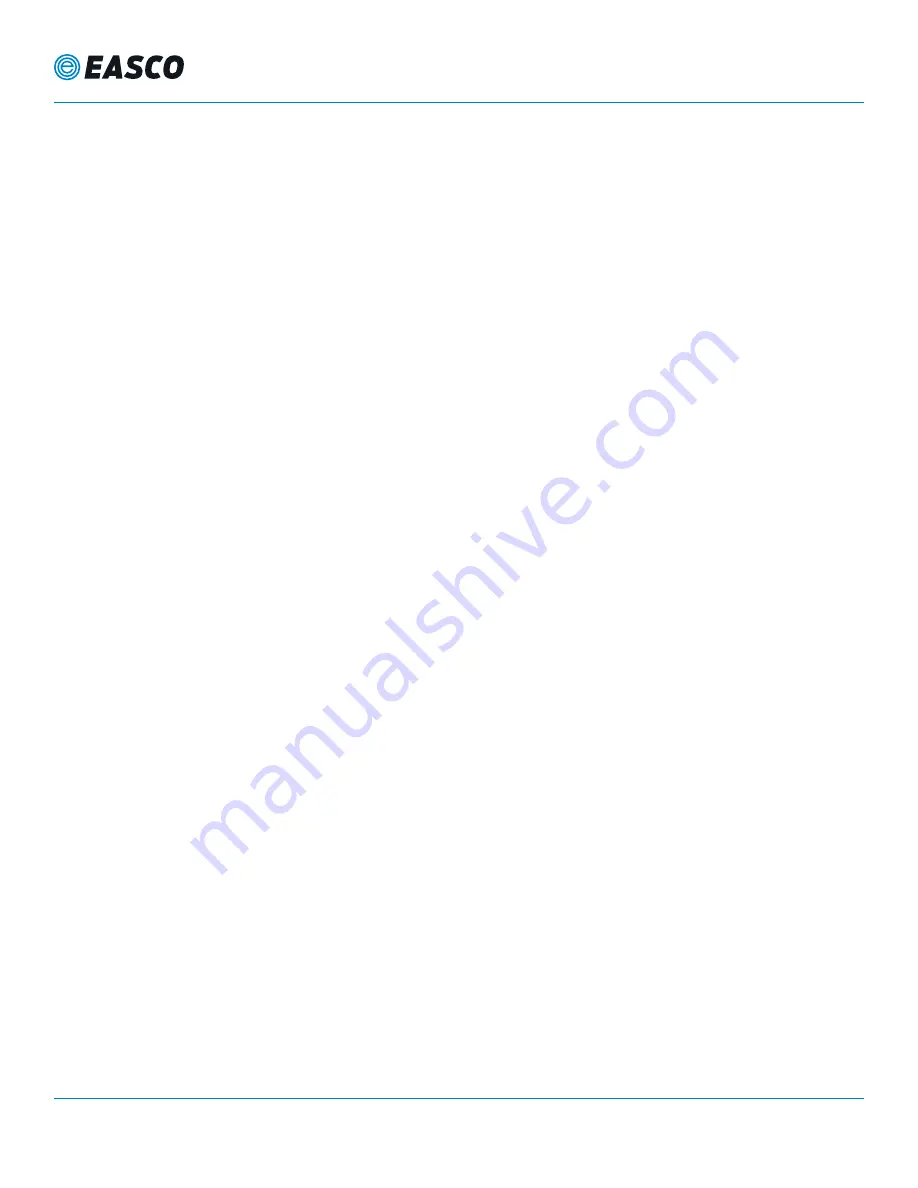
INSTALLATION, OPERATION AND MAINTENANCE MANUAL
Easco Boiler Corp 1175 Leggett Ave Bronx, NY 1047 T: 718.378.3000 F: 718.378.4560 [email protected] easco.com
Page 40 of 46
7.9 Maintain Drip Tight Connections
Repair all minor leaks promptly. If serious leaks occur shut the Boiler down immediately
and cool gradually. All piping connections must be maintained leak proof as even minor
leaks, if neglected, may become serious. This applies especially to water column, gage
glass, water level control piping, man hole and hand holes. Pipe nipples should be
replaced if there is evidence of leaking. Leaky plugs in boiler shell should be replaced with
new plugs or nipples and caps. Tube joints must be inspected periodically to ensure they
are leak free. All support systems and auxiliary equipment must be maintained in top
condition to ensure long and trouble free operation of the boiler room system.
7.10 Foaming and Priming
Foaming and priming in the steam Boiler will cause large quantities of water to be
carried over into the steam main. It will be detected by violent fluctuations of the water
in the glass or by sudden dropping of the water level from the glass. Impurities will show
as tiny specks or flakes floating in the boiler water. The following reasons may be the
cause of the trouble:
•
Dirt or oil in boiler water,
•
Over-dose of water treatment,
•
Carrying too high a water level in Boiler,
•
Load demand exceeds boiler rating,
•
Sudden increases in load (sudden pressure drop).
In case of serious trouble, stop the burner and decrease the load on the Boiler until the
true level can be determined. Then alternately blow down and feed fresh water several
times. If trouble continues, it will be necessary to wash out the Boiler and refill with
fresh water. Test safety valve and connections of pressure gauge, water column and
gage glass to make sure that they are clear and unobstructed by the impurities, which
are responsible for priming.
A practical check to determine if impurities are causing foam is to place samples of boiler
water in a beaker and brings it to a boil. If contaminants exist, it will foam. A similar test in
a second beaker filled with tap water will determine how bad the boiler water is.
7.11 Corrosion and Pitting
Corrosion of the Boiler on either the waterside or the fireside can be of very serious
consequence and should be guarded against. Waterside corrosion is generally caused
by an unfavorable water condition or oxygen, which attacks the metal and forms
pit marks or holes in the tubes. Control of the boiler water alkalinity and desertion is
considered the best means of preventing waterside corrosion. The proper alkalinity for
boiler operation is recommended as a minimum pH value of 9.0. The Boiler should be
examined regularly for corrosion.
7.12 Periodic Inspecting of Existing Boilers
The main purposes for re-inspection include protection against loss or damage to the
pressure vessel because of corrosion, pitting, etc. protection against unsafe operating
conditions possibly caused by changes in piping or controls or lack of testing of safety