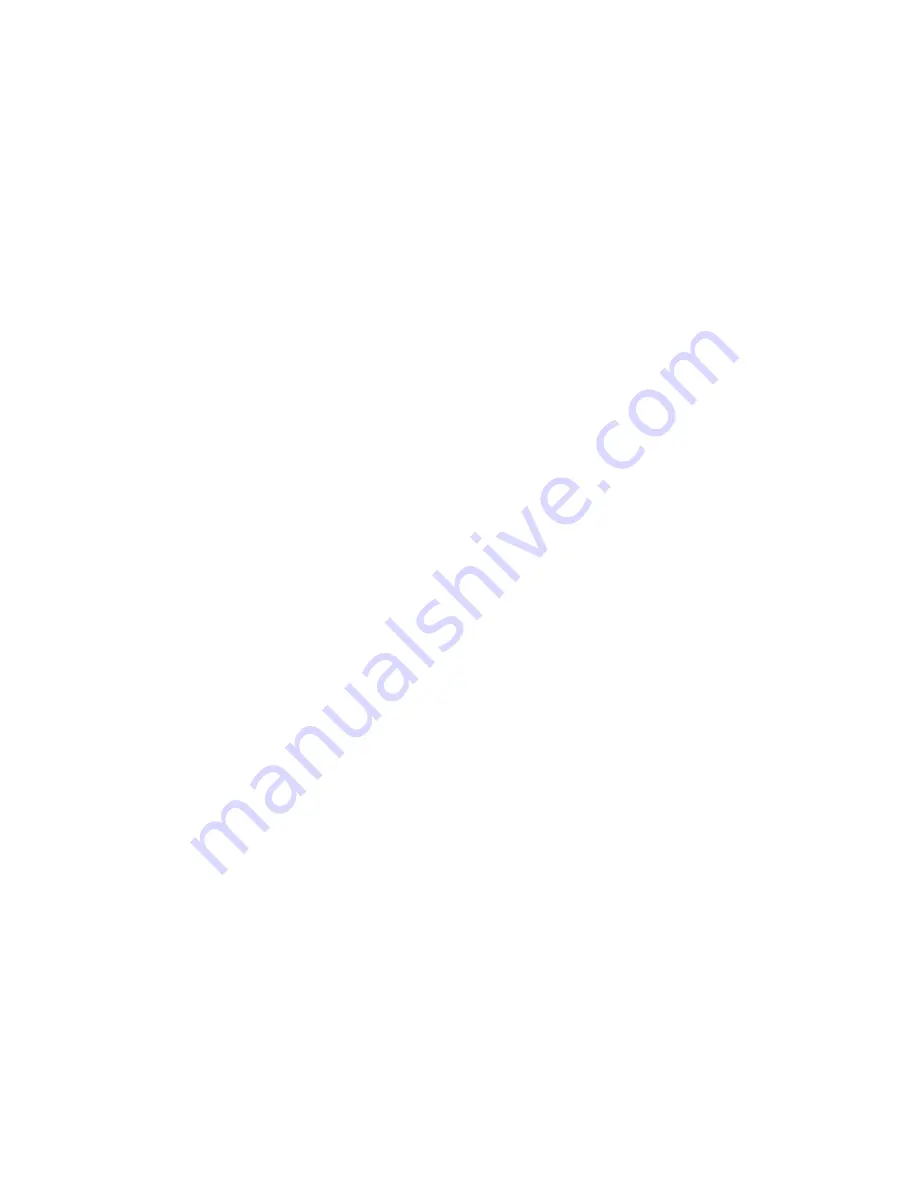
Disassembly/Assembly Instructions - .4 hp Dynafine
®
Tools (Cont.)
6.
Use a .001"(0.3mm) thick feeler gauge to check the clearance between the front bearing plate and the face of the rotor.
7.
The clearance should be .001"-.0015" (0.3-0.4mm).
Note:
If the clearance needs adjustment, repeat steps 2-5 adding or removing shims as required.
8.
Lubricate the
01480
Vanes with the
95842
Dynabrade
®
Air Lube 10W/NR (or equivalent) and install these into the rotor.
9.
Install the
01476
Cylinder over the rotor so that the air inlet opening of the cylinder will line up with the air inlet opening in the
02673
Rear Bearing Plate.
10.
Use the raised outer diameter of the
96216
Bearing Press Tool and the arbor press to install the
02696
Bearing into the
02673
Rear Bearing Plate.
11.
Use the raised inner diameter of the
96216
Bearing Press Tool and the arbor press to install the bearing/plate onto the rotor.
Note:
Carefully press the bearing/plate down until it just touches the cylinder. This will establish a snug fit between the bearing plates and the cylinder.
12.
Apply a small amount of light grease to the seal of the
02696
Bearing and adhere the
02679
Shield against the bearing.
13.
Carefully slide the motor assembly into the
01546/57779
Housing.
14.
Apply a small amount of the Loctite
®
#567 (or equivalent) to the threads of the
01546/57779
Housing.
15.
Use a 3mm adjustable pin spanner wrench or the
50971
Lock Ring Tool to tighten the exhaust cover onto the
01546/57779
Housing.
(Torque to 28N•m/250 in. lbs.)
16.
Install the
57975
Clamp onto the boot assembly.
17.
Install the boot assembly with the clamp, aligning them on the
57962
Exhaust Cover. Tighten the clamp. (Torque to 7N•m/6 in. lbs.)
18.
Use the
95266
Hex Key (3mm) to install the sanding attachment.
Motor Assembly Complete.
Tool Assembly Complete. Please allow 30 minutes for adhesives to cure before operating tool.
Important:
Before operating , place 2-3 drops of Dynabrade Air Lube (P/N
95842
) directly into inlet with throttle lever depressed. Operate tool for 30
seconds to allow air lube to properly lubricate internal motor components. Motor should now be tested for proper operation at 90 PSIG (6.2 Bar, g) max.
If tool operates at a higher RPM than marked on the tool or if vibration and sound levels seem abnormal, the tool should be serviced to correct
the cause before use.
Throttle Positioning Procedure:
Important: Carefully perform this procedure so as not to entirely separate the 01546 Housing from the valve housing. Loosen the 01461 Lock Nut
only enough to make the desired throttle lever adjustment.
1.
Place the
52296
Repair Collar around the valve housing and hold it in a vise so that the
01546/57779
Housing is pointing up.
2.
Slip the
01558
Collar down onto the valve housing to expose the
01461
Lock Nut.
3.
With a firm hold on the
01546/57779
Housing use a 34mm or an adjustable wrench to turn the lock nut clockwise to loosen the
01546/57779
Housing
from the valve housing.
4.
Orient the throttle lever to the operators desired grip and positioning.
Note:
Allow for additional rotation of the
01546/57779
Housing as the
01461
Lock Nut is tightened.
5.
Grasp the
01546/57779
Housing firmly to reduce its rotation. Use a 34mm or an adjustable wrench to tighten the
01461
Lock Nut.
Torque to 45 N•m/400 lbs. in.
6.
Slip the
01558
Collar back over the
01461
Lock Nut.
Throttle Positioning Procedure Complete.
6
Loctite
®
is a registered trademark of Loctite Corp.