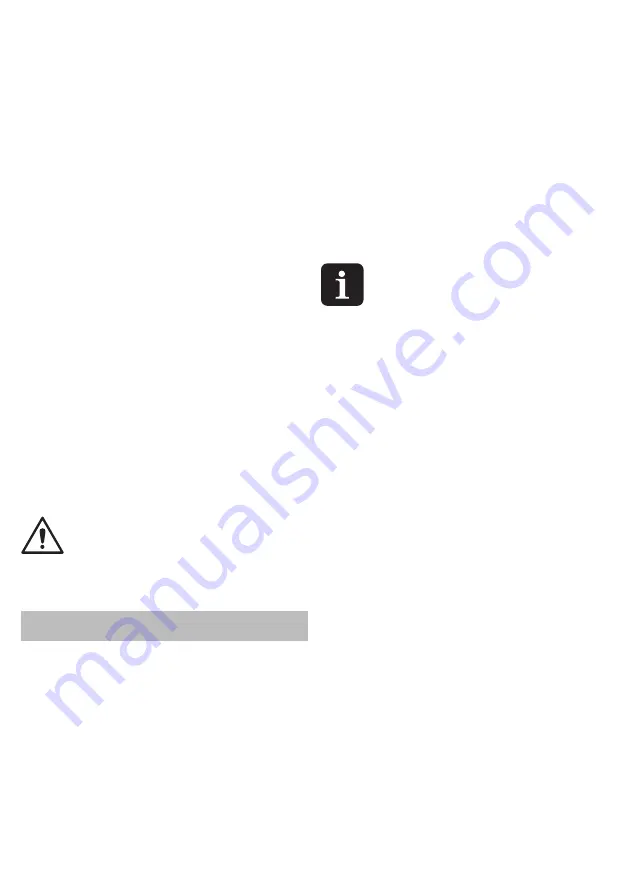
25
English
When reducing the distance between the electrode
and the piece to be welded, the welding current is
increased for a short time which allows the metal of the
electrode and a work piece to be fused immediately,
thus increasing the arc gap�
Control
7
can change the arc dynamics - lesser values
provide for smaller metal splashing while bigger values
provide for deeper fusion penetration�
Hot start
[MMA-400 T]
The hot start function increases the set welding current
for a short time at the moment of the welding arc
lighting� It facilitates the lighting up of the welding arc�
Easy start
The easy start function (increased voltage of idle run-
ning) facilitates the lighting up of the welding arc�
Voltage reduction device (switch "VRD")
[MMA-200 MINI]
The function of voltage reduction of idle running in-
creases the safety of the welding works performance�
In the case of arc extinction the voltage on the elec-
trode decreases below 15 V and the electric shock
probability for a worker is considerably reduced which
is especially convenient when working in cramped
spaces, metal boxes, etc�)�
•
To switch on push the switch
16
� Indicator
17
will
light up where the system of voltage reduction of idle
running is on�
•
To switch off push the switch
16
again� Indicator
17
will go off�
Note: this system does not provide for
the full protection against electric shock
(for example, where an electrode end
touches the ground item the voltage
supply to electrode is continued). That is why all
safety procedures must be strictly observed as
well as protective clothes must be worn.
Recommendations on the
machine operation
Preliminary works (see fig. 4)
•
Finish the edges of work pieces to be welded is
recommended�
•
Angle of flare (a, see fig. 4.1)
- is carried out
when metal is more than 3 mm thick� Absence of
grooving can result in spilling on section of weld,
and also in overheating and burning of metal;
atabsence of grooving, for maintenance of weld
penetration always try to increase size of a welding
current�
•
Backlash (b, see fig. 4.2)
- correctly fixed before
welding, allows full weld penetration on section of
weld at imposing the priming layer of a seam�
•
The length of a sheet bevel (c, see fig. 4.3)
-
adjusts smooth transition from thicker welded detail
to more thin, thus stress concentrators in welded
structures are eliminated�
•
Clean welding surfaces from rust and paint coatings�
•
Please remember that a large quantity of heat
is released during welding which can damage the
surrounding items, therefore, carefully choose the site
and take appropriate actions to prevent fire.
Electrodes
The right choice of electrodes, to a great extent, pre-
determines the welding seam quality and the operation
speed� Before purchasing electrodes, carefully
examine the recommendations of their use� Consult a
specialist if necessary� It is also important to observe
the electrode storage conditions�
General operation recommendations (see. fig. 4-5)
The recommendations below apply to all
machines connected through a socket
connector. In the case of stationary con-
nection the machine assembly and net-
work connection will be done beforehand.
•
Place the machine in an even, dry, not vibrating
surface observing all above-mentioned safety
procedures�
•
Connect the ground wire�
•
Connect the welding cables to the machine� Welding
can be performed with direct and reverse polarity�
The selection of polarity depends on the materials to
be welded and the recommendations on how to use
electrodes�
•
Direct polarity
- connect electrode holder
13
to
socket "-"
9
, connect earth clamp
12
to socket "+"
10
�
In such a mode the electrode heats less than the ba-
sic metal, the electrodes get fused slower, the weld-
ing joint is completed with a deeper penetration�
•
Reverse polarity
- connect electrode holder
13
to socket "+"
10
, connect earth clamp
12
to sock-
et "-"
9
� In such a mode the work piece is heated
less than the electrode which can be used for weld-
ing high-carbon, alloy and special steels sensitive to
overheat as well as for welding sheet metal�
•
Press the lever of the electrode holder
13
and install
the electrode end (the end free from coating) into
electrode holder
13
and then release the lever�
•
Fix earth clamp
12
on one of the parts to be welded�
•
Connect the machine to the mains and switch it on�
•
Set the welding current value using control
8
� The
selection of welding current depends on the electrode
to be used, thickness of material to be welded, spatial
position of a seam etc�
•
Choose additional welding parameters (arc force
etc), if your machine has these functions�
•
Ignite the welding arc in one of two ways: ignition by
touching (see fig. 4.4); ignition by scratching (see fig. 4.5).
•
The main practices of welding electrode handling
are described below:
•
usually welding is carried out with vertically
positioned electrode or at its inclination concerning a
seam, in a corner forward or back� When welding by
a corner back, it is provided better fusion and smaller
width of a seam (but performance of work in this case
demands the certain skill);
•
progressive motion of an electrode (see fig. 5.1)
on a direction of an axis of the electrode, for main-
Содержание MMA-180 I
Страница 1: ......
Страница 5: ...5 ...
Страница 6: ...6 ...
Страница 7: ...7 ...
Страница 8: ...8 ...
Страница 9: ...9 ...
Страница 10: ...10 ...
Страница 11: ...11 ...
Страница 140: ...140 ...
Страница 141: ...141 ...
Страница 142: ...142 ...
Страница 143: ...143 ...
Страница 144: ...144 ...
Страница 145: ...145 ...
Страница 146: ...146 ...
Страница 147: ...147 ...
Страница 148: ...148 ...
Страница 149: ...149 ...
Страница 150: ...150 ...
Страница 151: ...151 ...
Страница 152: ...152 ...
Страница 153: ...153 ...
Страница 171: ...171 ...
Страница 172: ...172 ...
Страница 173: ...173 ...
Страница 174: ...174 ...
Страница 175: ...175 ...
Страница 176: ......