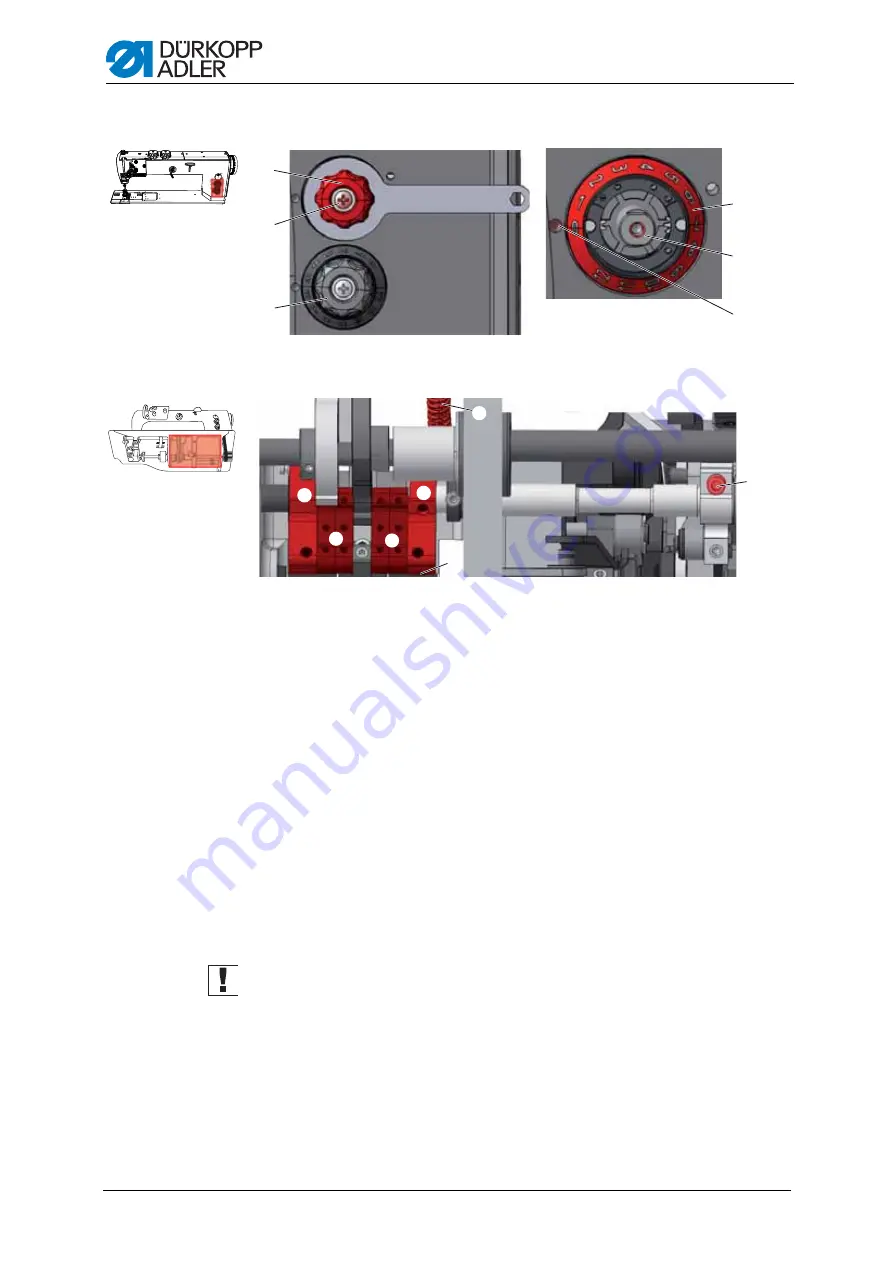
Setting the stitch length adjusting wheels
26
Service manual H867 Version 00.0 - 08/2013
Figure 18: Setting the upper stitch length adjusting wheel - Part 2
6. Check whether the frame (7) for the stitch regulator gear can be moved.
Tip
: In machines that have a stitch adjustment lever, you can check
this by pressing the stitch adjustment lever.
In machines that do not have a stitch adjustment lever, you can insert
the locking peg or a hex key into the opening (9) and use it to try and
move the frame (7) up and down.
7. As soon as the frame (7) no longer moves:
Remove the wrench from the shaft (5).
8. Turn the scale (6) for the upper stitch length adjusting wheel (1) such
that the 0 is exactly next to the adjusting mark (4).
9. Place the upper stitch length adjusting wheel (1) onto the shaft (5).
10.Hold the upper stitch length adjusting wheel (1) using a star key.
11.Tighten the upper stitch length adjusting wheel (1) on the shaft (5) using
the screw (2).
12.
Important:
Check whether the plates for the stitch regulator gear (8)
are parallel to one another in this position.
If the plates (8) are not parallel to one another:
13.Remove the tension spring (10).
14.Loosen the clamping screw (11).
15.Manually position the plates (8) so that they are parallel.
16.Tighten the clamping screw (11).
17.Attach the tension spring (10).
2
3
5
6
4
1
0
^
7
7
8
8
9
(7) - Frame for the stitch regulator gear
(8) - Plates for the stitch regulator gear
(9) - Opening
(10) - Tension spring
(11) - Clamping screw
(1) - Upper stitch length adjusting wheel
(2) - Screw
(3) - Lower stitch length adjusting wheel
(4) - Adjusting mark
(5) - Shaft
(6) - Scale
Содержание M-TYPE H867
Страница 1: ...H867 Service manual...
Страница 91: ......