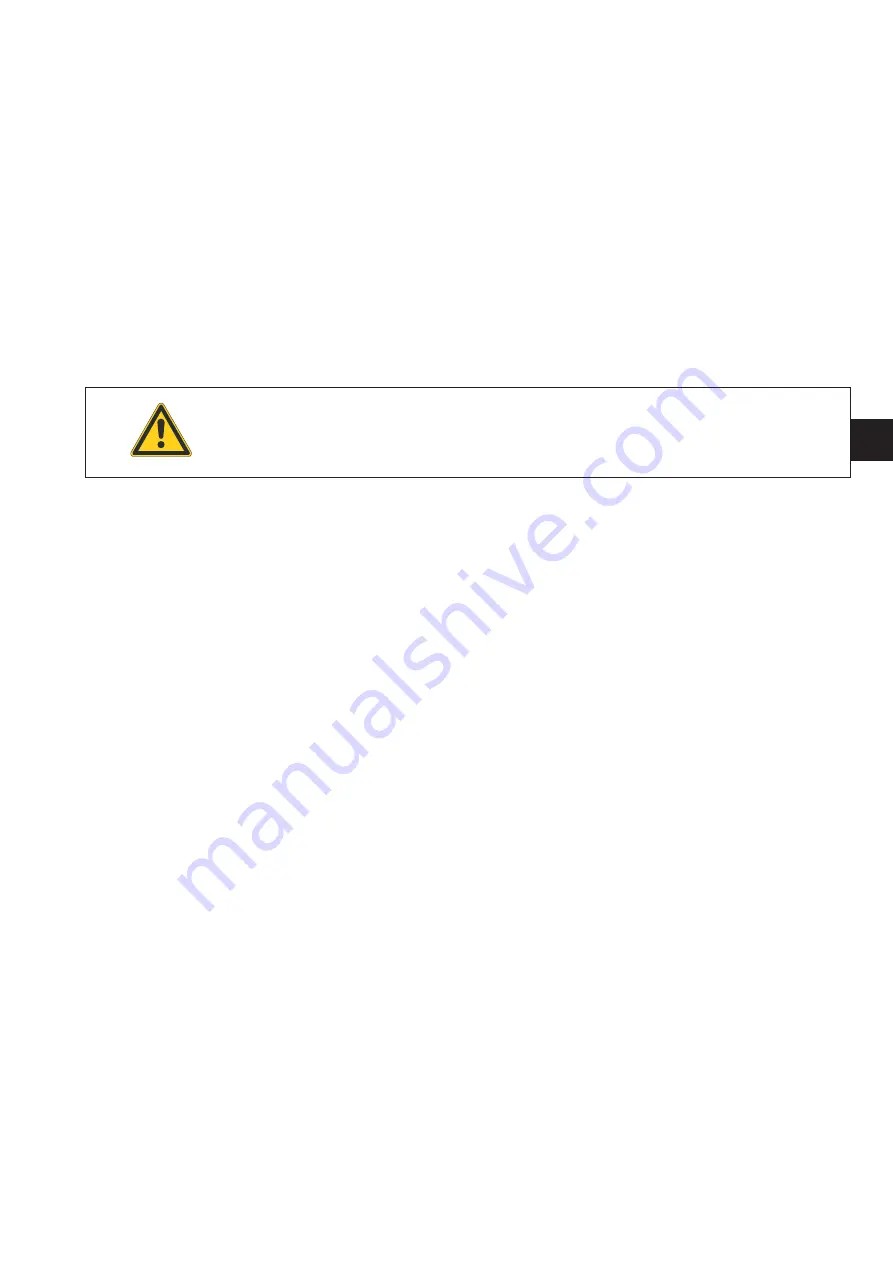
7
Electronic control and sewing machine drive - positioning motor
All operating instructions and parameter sheets are available at the
manufacturers´ websites (see
www.efka.net,
www.duerkopp-adler.com, www.hohsing.com,
etc.).
Selected instructions concerning the control and drive setting needed
for the operators are included in the Operating instructions.
Selected instructions needed for the technician to set the drive are
included in the Operating instructions.
Important notes concerning electrostatic discharges (ESD)
Caution!
Before effectuating any works on electronic components: Turn off the
main switch. Remove the plug from the socket.
Electrostatic discharges can cause damage to PCBs and other
components. You can obtain a certain protection by wearing anti-static
gloves or wrist-wraps that you can connect for grounding on the mass
of any unpainted metal piece of the machine head or on the switch
cabinet.
Handle the PCBs with utmost caution. They are very sensitive towards
electrostatic discharges. Hold the PCBs only at their edges.
Put the PCBs after unwrapping or after dismounting with their
components upside onto a grounded statically discharged surface.
We recommend to use a conductive foam underlay but not as the
protective cover of the PCB.
Pay attention not to pull the PCBs over any surface.
35
EN
Содержание 884-xxx-M series
Страница 1: ...884 Service Instructions ...
Страница 34: ...32 4 3 5 ...