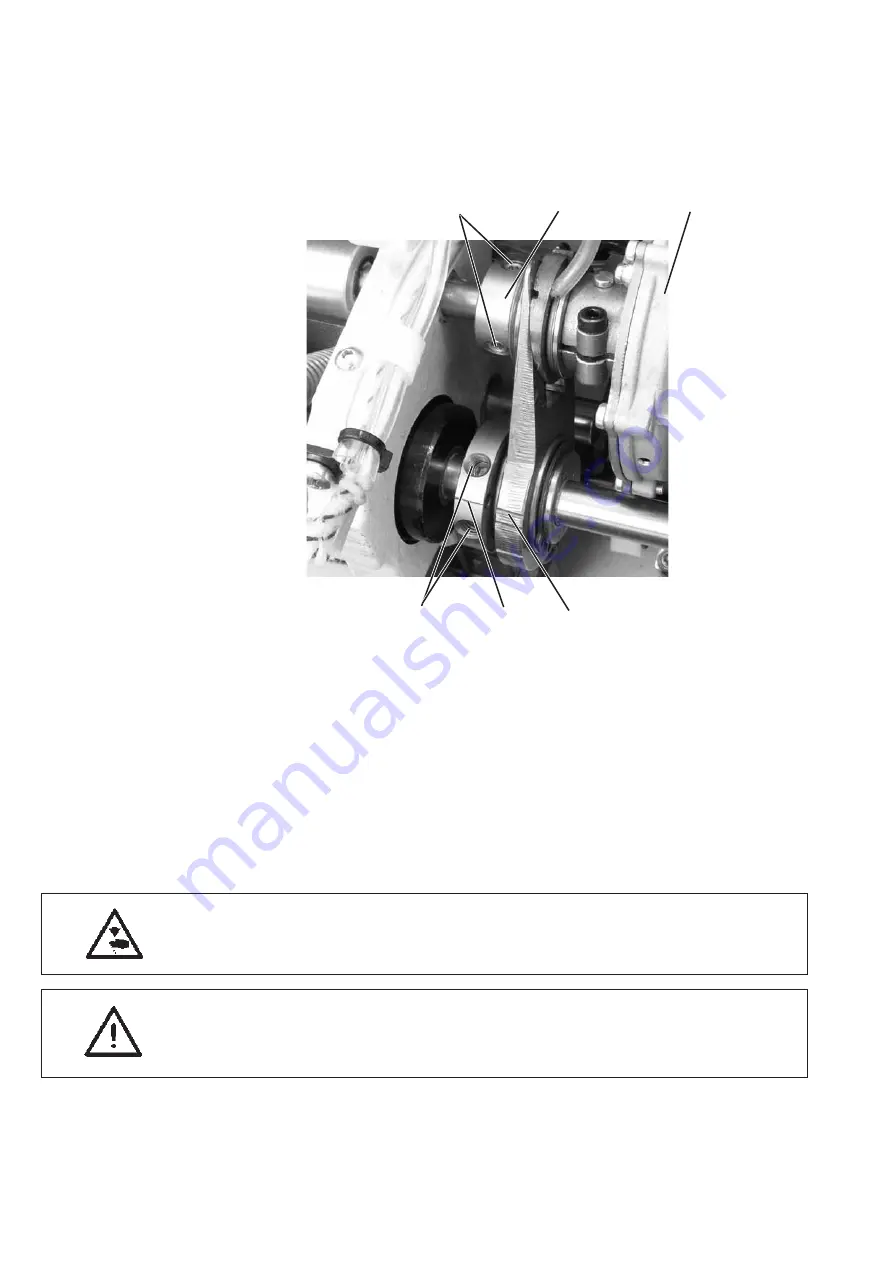
2.6
Switching over the feed clutch
Rule:
The clutch should be switched over when it is motionless (i.e., when it
is in the dead centre point of its pendulum motion).
–
Loosen the screws (1) on the eccentric tappet (2).
–
Turn the eccentric tappet so that the dash (2) is aligned with the
other dash (3).
–
Loosen the three screws (4). Loosen the adjusting nut (5).
–
Tighten the adjusting nut (5) until you feel it strike (the tightening
increases in jumps).
Push the clutch (6) to the right until the end stop is reached.
Tighten the screws (4).
–
Verify the adjustment. Turn the eccentric tappet with your hand in
the other direction. The resistance during the rotation of the
eccentric tappet should increase significantly when the two dashes
are lined up.
Caution: Risk of Injury!
Turn the main switch off.
Only carry out this adjustment when the machine is turned off.
ATTENTION: Danger of breakage!
Imprecise settings can shorten the lifespan of the machine.
10
4
5
2
1
3
6