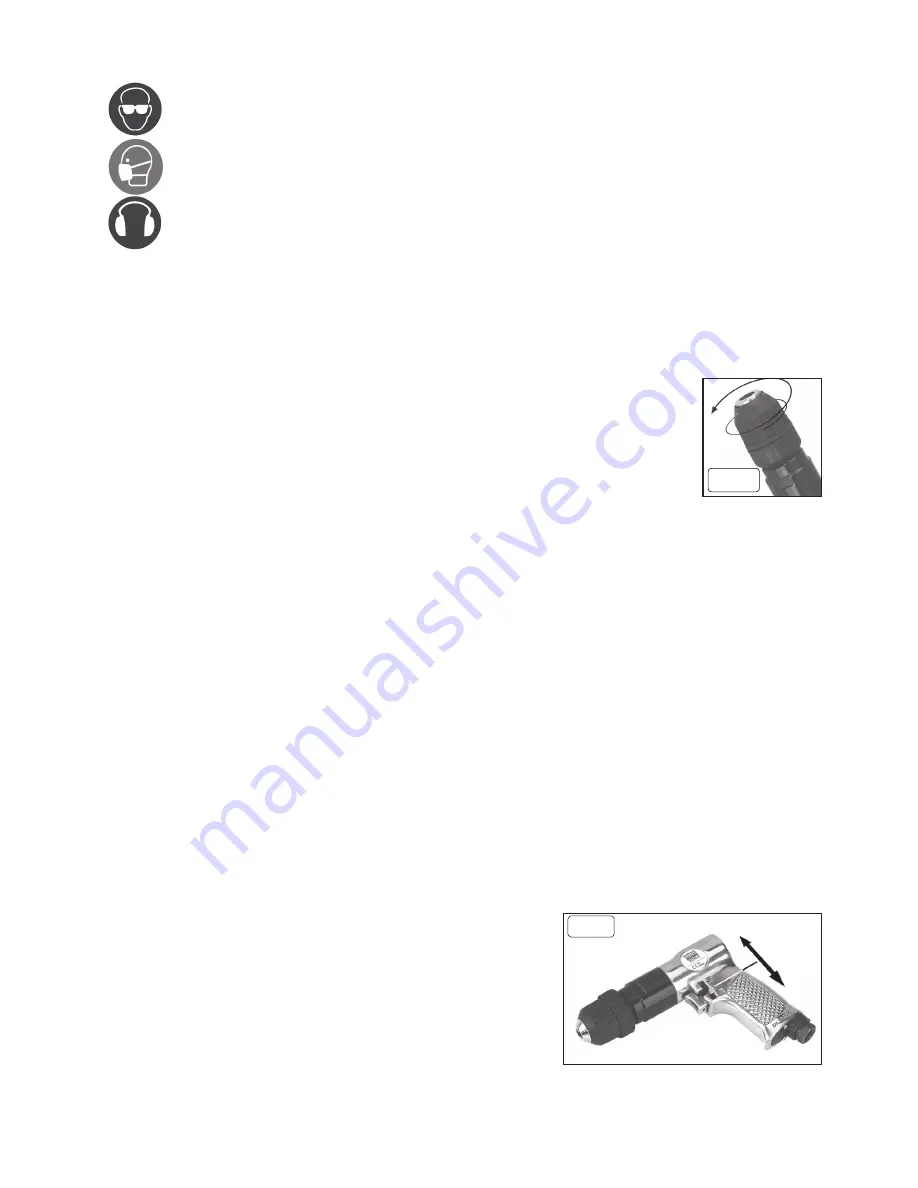
Eye and Breathing Protection
The sanding process will create dust and other airborne particles. There is no dust
extraction function on this machine so it is essential that approved eye and breathing
protection is worn.
Noise and Ear Protection
Depending on the material being worked on and the type of sanding disc used, noise
levels may cause hearing damage including temporary or even permanent hearing loss.
It is recommended that Ear Protection is worn at all times when using the sander.
Repetitive Strain Injury (RSI)
All products of this nature can cause RSI if used for long period, particulary in an
awkward operating position. Adequate rest periods and working conditions should be
considered for prolonged use.
General Safety Information
1
Ensure the sanding pad is equal to or greater than 120% of the stated RPM of the
sander.
2
Keep the workplace clean and tidy.
3
Use the tool in a well ventilated area.
4
Air hoses can present a trip hazard, always keep hoses in a way that minimises trip
hazards.
5
DO NOT hold the workpiece by hand, always make sure the workpiece is clamped
securely.
6
Keep all flammable and combustible materials away from the work area.
7
Children and other unauthorised persons should be kept away from the work area.
8
NEVER use the sander whilst the floor underfoot is wet or slippery.
9
NEVER use the sander when standing on an unstable surface.
10
Keep the sander out of reach of children.
11
Analyse the material you are sanding. Be aware of the dangers of sanding lead based
paints. Historically, paint contained lead and sanding such paint will cause toxic dust. If
you suspect that lead could be in the paint the following actions must be observed;
- Alert any other persons in the nearby and keep them away from the working
area.
- Use specific air fed respirator, PE coated coveralls and latex gloves.
- Dispose of any dust and paint waste correctly and thoroughly clean the
workpiece and working area after the sanding has finished.
12
NEVER attempt to sand materials containing asbestos.
13
VIBRATION. Hand held air tools may produce vibration. Vibration from sanders can
cause disease. The use of gloves will help reduce the risk and can help prevent injury.
14
Disconnect the air supply before changing disc or pad.
15
Ensure the sander has stopped rotating before putting it down or handling the pad or
disc.
16
NEVER carry the sander by the air hose.
17
NEVER point the sander at other persons.
18
NEVER operate the sander whilst under the influence or drugs, alcohol or intoxicating
medication.
19
Check you have no loose clothing, hair, jewellery or any other items of a personal nature
that might become entangled with the rotating parts.
20
Check you have a maximum inlet air pressure of 90PSI/6.3BAR.
PLEASE KEEP THIS MANUAL SAFE FOR FUTURE REFERENCE
Duren Tools
T: 01582 484875 E: [email protected]
www.duren.co.uk
625624_Product Instructions 27/03/2014 08:30 Page 3
Eye and Breathing Protection
The sanding process will create dust and other airborne particles. There is no dust
extraction function on this machine so it is essential that approved eye and breathing
protection is worn.
Noise and Ear Protection
Depending on the material being worked on and the type of sanding disc used, noise
levels may cause hearing damage including temporary or even permanent hearing loss.
It is recommended that Ear Protection is worn at all times when using the sander.
Repetitive Strain Injury (RSI)
All products of this nature can cause RSI if used for long period, particulary in an
awkward operating position. Adequate rest periods and working conditions should be
considered for prolonged use.
General Safety Information
1
Ensure the sanding pad is equal to or greater than 120% of the stated RPM of the
sander.
2
Keep the workplace clean and tidy.
3
Use the tool in a well ventilated area.
4
Air hoses can present a trip hazard, always keep hoses in a way that minimises trip
hazards.
5
DO NOT hold the workpiece by hand, always make sure the workpiece is clamped
securely.
6
Keep all flammable and combustible materials away from the work area.
7
Children and other unauthorised persons should be kept away from the work area.
8
NEVER use the sander whilst the floor underfoot is wet or slippery.
9
NEVER use the sander when standing on an unstable surface.
10
Keep the sander out of reach of children.
11
Analyse the material you are sanding. Be aware of the dangers of sanding lead based
paints. Historically, paint contained lead and sanding such paint will cause toxic dust. If
you suspect that lead could be in the paint the following actions must be observed;
- Alert any other persons in the nearby and keep them away from the working
area.
- Use specific air fed respirator, PE coated coveralls and latex gloves.
- Dispose of any dust and paint waste correctly and thoroughly clean the
workpiece and working area after the sanding has finished.
12
NEVER attempt to sand materials containing asbestos.
13
VIBRATION. Hand held air tools may produce vibration. Vibration from sanders can
cause disease. The use of gloves will help reduce the risk and can help prevent injury.
14
Disconnect the air supply before changing disc or pad.
15
Ensure the sander has stopped rotating before putting it down or handling the pad or
disc.
16
NEVER carry the sander by the air hose.
17
NEVER point the sander at other persons.
18
NEVER operate the sander whilst under the influence or drugs, alcohol or intoxicating
medication.
19
Check you have no loose clothing, hair, jewellery or any other items of a personal nature
that might become entangled with the rotating parts.
20
Check you have a maximum inlet air pressure of 90PSI/6.3BAR.
PLEASE KEEP THIS MANUAL SAFE FOR FUTURE REFERENCE
Duren Tools
T: 01582 484875 E: [email protected]
www.duren.co.uk
625624_Product Instructions 27/03/2014 08:30 Page 3
PLEASE KEEP THIS MANUAL SAFE FOR FUTURE REFERENCE
Duren Tools
T: 01582 484875 E: [email protected]
www.duren.co.uk
4
It is strongly advised that you always use a Whip Hose/Leader Hose in combination with
Quick Release Couplings. See
Fig. 2
for recommended setup.
5
Water in the air supply will cause the internal bearing of the tool to rust and eventually
seize.
6
Make sure that your airline is free from water at all times.
7
Always select the correct sanding disc grit for the job.
Tools Included with your Sander
1 x High Flow Male Air Fitting
Maintenance
1
If the air supply is not lubricated sufficiently it will be necessary to lubricate the tool
directly. This can be done by disconnecting the air hose and pouring in 5ml of air tool oil
into the Air Inlet. Read safety data sheet or instructions on use of oil to ensure safe
usage. These can be obtained from your supplier.
2
Replace worn or damaged parts using genuine parts only.
3
Store tool in a dry area, do not allow tool to be immerse in water or used/stored in wet
conditions.
625624_Product Instructions 27/03/2014 08:30 Page 5
Operation
Ensure you read, understand and apply safety instructions before use.
n
WARNING! Unplug from the air supply before placing bit into chuck.
1.1.
DRILL BIT FITTING
. Regularly check the drill bit and always change if worn, cracked
or otherwise damaged.
1.1.2. Open or close the chuck jaws to a point where the opening is slightly larger than the
drill or tool bit to be used by unscrewing the chuck (fig 3). Insert the drill bit into the
chuck as far as it will go. Tighten the chuck securely.
1.2. Connect air supply to drill. Squeeze the trigger to check that the drill is working correctly before starting work.
1.2.1.
DO NOT
allow drill to run freely for an extended period of time as this will shorten the life of bearings.
n
WARNING! Ensure you wear approved safety goggles and any other safety items required for the job.
1.3.
USING THE DRILL
1.3.1. Ensure the drill is turning in the forward direction by checking that the lever adjacent to the trigger is next to
the forward symbol “F” (fig 4). If not, push the lever over to the forward position.
1.3.2. Hold tool firmly and place the bit tip to the point to be drilled.
1.3.3. Depress the trigger to start drill. Move the drill bit into the work piece applying only enough pressure to keep
the bit cutting. DO NOT force or apply side pressure to elongate the hole.
1.3.4. If the material to be drilled is free standing it should be secured in a vice or with clamps to keep it from
turning as the drill bit rotates.
1.3.5. When drilling metals, use a light oil on the drill bit to keep it from overheating. Oil will prolong life of bit and
improve the drilling action.
1.3.6 For hard smooth surfaces use a centre punch to mark desired hole location. This will prevent bit from
slipping as your start to drill.
1.3.7 A pilot hole may be necessary to assist the final drill size through the work piece. Lock a pilot drill (smaller
size drill than the finished hole size) into the chuck. Follow steps 1.3.1. to 1.3.3. above and drill a pilot hole
in the middle of the centre punch mark where final hole is to be drilled. Insert the final sized bit in chuck.
Hold drill firmly, place the bit at the entrance of the pilot hole and depress the trigger.
n
WARNING! Be prepared for drill binding on break through. When these situations occur the
drill has a tendency to grab and kick in the opposite direction which could cause loss of control. If you are
not prepared, this loss of control can result in damage and/or personal injury.
1.3.8 If the bit jams in the workpiece or if the drill stalls, release the
trigger switch immediately. Remove the bit from the workpiece
and determine the reason for jamming. It may be necessary to
reverse the direction of rotation by moving the lever adjacent to
the trigger to the reverse “R” position (fig 4).
fig.3
4.1.3.
WARNING!
ensure the air supply is clean and does not exceed 90 psi while operating the tool. too high an air
pressure and unclean air will shorten the product life due to excessive wear, and may be dangerous causing
damage and/or personal injury.
4.1.4. drain the air tank daily. Water in the air line will damage the tool.
4.1.5. clean air inlet filter weekly.
4.1.6. line pressure should be increased to compensate for unusually long air hoses (over 8 metres). the minimum
hose diameter should be 1/4” i.d. and fittings must have the same inside dimensions.
4.1.7. Keep hose away from heat, oil and sharp edges. check hose for wear, and make certain that all connections are
secure.
4.2. Couplings.
Vibration may cause failure if a quick change coupling is connected directly to the tool.
to overcome this, connect a leader hose to the tool. A quick change coupling may then be used to connect the
leader hose to the air line recoil hose. see fig 1 & 2.
fig.2
5. OPERATION
Ensure you read, understand and apply safety instructions before use.
WARNING! Unplug from the air supply before placing bit into chuck.
5.1. DRILL bIT FITTING.
regularly check the drill bit and always change if worn, cracked or otherwise damaged.
5.1.2. open or close the chuck jaws to a point where the opening is slightly larger than the drill or tool bit to be used
by unscrewing the chuck (fig 3). insert the drill bit into the chuck as far as it will go. tighten the chuck securely.
5.2.
connect air supply to drill. squeeze the trigger to check that the drill is working correctly before starting work.
5.2.1.
DO NOT
allow drill to run freely for an extended period of time as this will shorten the life of bearings.
WARNING! Ensure you wear approved safety goggles and any other safety items required for the job.
5.3.
USING THE DRILL
5.3.1. ensure the drill is turning in the forward direction by checking that the lever adjacent to the trigger is next to
the forward symbol “f” (fig 4). if not, push the lever over to the forward position.
5.3.2. Hold tool firmly and place the bit tip to the point to be drilled.
5.3.3. depress the trigger to start drill. move the drill bit into the workpiece applying only enough pressure to keep the bit cutting.
DO NOT
force
or apply side pressure to elongate the hole.
5.3.4. if the material to be drilled is free standing it should be secured in a vice or with clamps to keep it from turning as the drill bit rotates.
5.3.5. When drilling metals, use a light oil on the drill bit to keep it from overheating. oil will prolong life of bit and improve the drilling action.
5.3.6 for hard smooth surfaces use a centre punch to mark desired hole location. this will prevent bit from slipping as your start to drill.
5.3.7 A pilot hole may be necessary to assist the final drill size through the workpiece. lock a pilot drill (smaller size drill than the finished hole
size) into the chuck. follow steps 5.3.1. to 5.3.3. above and drill a pilot hole in the middle of the centre punch mark where final hole is to be
drilled. insert the final sized bit in chuck. Hold drill firmly, place the bit at the entrance of the pilot hole and depress the trigger.
WARNING! be prepared for drill binding on break through. When these situations occur the drill has a tendency to grab and kick
in the opposite direction which could cause loss of control. If you are not prepared, this loss of control can result in damage
and/or personal injury.
5.3.8 if the bit jams in the workpiece or if the drill stalls, release the trigger switch immediately. remove the bit from the workpiece and determine
the reason for jamming. it may be necessary to reverse the direction of rotation by moving the lever adjacent to the trigger to the reverse
“r” position (fig 4).
fig.4
6. MAINTENANCE
WARNING!
Disconnect drill from air supply before changing drill bit, servicing or performing maintenance.
replace or repair
damaged parts.
Use genuine parts only. Unauthorised parts may be dangerous and will invalidate the warranty.
6.1.
if the air supply does not have an oiler, lubricate the drill daily with a few drops of good grade air tool oil, such as sealey Ato/500 or
Ato/1000, dripped into the air inlet before use or dispensed automatically through an air system oiler, such as sealey model sA100l or
sA1/l.
6.2.
clean the drill after use and change the bit when worn or damaged.
6.3.
loss of power or erratic action may be due to the following:
a)
excessive drain on the air supply. moisture or restriction in the air line. incorrect size or type of hose connectors. to remedy check the
air supply and follow instructions in section 4.
b)
Grit or gum deposits in the drill may also reduce performance. flush the drill with gum solvent oil or an equal mixture of sAe no 10 oil
and kerosene. Allow to dry before use.
if you continue to experience problems, contact your local sealey service agent.
6.4.
for a full service contact your local sealey service agent.
6.5.
When not in use, disconnect from air supply, clean drill and store in a safe, dry, childproof location.
sA241 issue:5(l) - 06/10/17
Original Language Version
© Jack sealey limited
fig.3
4.1.3.
WARNING!
ensure the air supply is clean and does not exceed 90 psi while operating the tool. too high an air
pressure and unclean air will shorten the product life due to excessive wear, and may be dangerous causing
damage and/or personal injury.
4.1.4. drain the air tank daily. Water in the air line will damage the tool.
4.1.5. clean air inlet filter weekly.
4.1.6. line pressure should be increased to compensate for unusually long air hoses (over 8 metres). the minimum
hose diameter should be 1/4” i.d. and fittings must have the same inside dimensions.
4.1.7. Keep hose away from heat, oil and sharp edges. check hose for wear, and make certain that all connections are
secure.
4.2. Couplings.
Vibration may cause failure if a quick change coupling is connected directly to the tool.
to overcome this, connect a leader hose to the tool. A quick change coupling may then be used to connect the
leader hose to the air line recoil hose. see fig 1 & 2.
fig.2
5. OPERATION
Ensure you read, understand and apply safety instructions before use.
WARNING! Unplug from the air supply before placing bit into chuck.
5.1. DRILL bIT FITTING.
regularly check the drill bit and always change if worn, cracked or otherwise damaged.
5.1.2. open or close the chuck jaws to a point where the opening is slightly larger than the drill or tool bit to be used
by unscrewing the chuck (fig 3). insert the drill bit into the chuck as far as it will go. tighten the chuck securely.
5.2.
connect air supply to drill. squeeze the trigger to check that the drill is working correctly before starting work.
5.2.1.
DO NOT
allow drill to run freely for an extended period of time as this will shorten the life of bearings.
WARNING! Ensure you wear approved safety goggles and any other safety items required for the job.
5.3.
USING THE DRILL
5.3.1. ensure the drill is turning in the forward direction by checking that the lever adjacent to the trigger is next to
the forward symbol “f” (fig 4). if not, push the lever over to the forward position.
5.3.2. Hold tool firmly and place the bit tip to the point to be drilled.
5.3.3. depress the trigger to start drill. move the drill bit into the workpiece applying only enough pressure to keep the bit cutting.
DO NOT
force
or apply side pressure to elongate the hole.
5.3.4. if the material to be drilled is free standing it should be secured in a vice or with clamps to keep it from turning as the drill bit rotates.
5.3.5. When drilling metals, use a light oil on the drill bit to keep it from overheating. oil will prolong life of bit and improve the drilling action.
5.3.6 for hard smooth surfaces use a centre punch to mark desired hole location. this will prevent bit from slipping as your start to drill.
5.3.7 A pilot hole may be necessary to assist the final drill size through the workpiece. lock a pilot drill (smaller size drill than the finished hole
size) into the chuck. follow steps 5.3.1. to 5.3.3. above and drill a pilot hole in the middle of the centre punch mark where final hole is to be
drilled. insert the final sized bit in chuck. Hold drill firmly, place the bit at the entrance of the pilot hole and depress the trigger.
WARNING! be prepared for drill binding on break through. When these situations occur the drill has a tendency to grab and kick
in the opposite direction which could cause loss of control. If you are not prepared, this loss of control can result in damage
and/or personal injury.
5.3.8 if the bit jams in the workpiece or if the drill stalls, release the trigger switch immediately. remove the bit from the workpiece and determine
the reason for jamming. it may be necessary to reverse the direction of rotation by moving the lever adjacent to the trigger to the reverse
“r” position (fig 4).
fig.4
6. MAINTENANCE
WARNING!
Disconnect drill from air supply before changing drill bit, servicing or performing maintenance.
replace or repair
damaged parts.
Use genuine parts only. Unauthorised parts may be dangerous and will invalidate the warranty.
6.1.
if the air supply does not have an oiler, lubricate the drill daily with a few drops of good grade air tool oil, such as sealey Ato/500 or
Ato/1000, dripped into the air inlet before use or dispensed automatically through an air system oiler, such as sealey model sA100l or
sA1/l.
6.2.
clean the drill after use and change the bit when worn or damaged.
6.3.
loss of power or erratic action may be due to the following:
a)
excessive drain on the air supply. moisture or restriction in the air line. incorrect size or type of hose connectors. to remedy check the
air supply and follow instructions in section 4.
b)
Grit or gum deposits in the drill may also reduce performance. flush the drill with gum solvent oil or an equal mixture of sAe no 10 oil
and kerosene. Allow to dry before use.
if you continue to experience problems, contact your local sealey service agent.
6.4.
for a full service contact your local sealey service agent.
6.5.
When not in use, disconnect from air supply, clean drill and store in a safe, dry, childproof location.
sA241 issue:5(l) - 06/10/17
Original Language Version
© Jack sealey limited