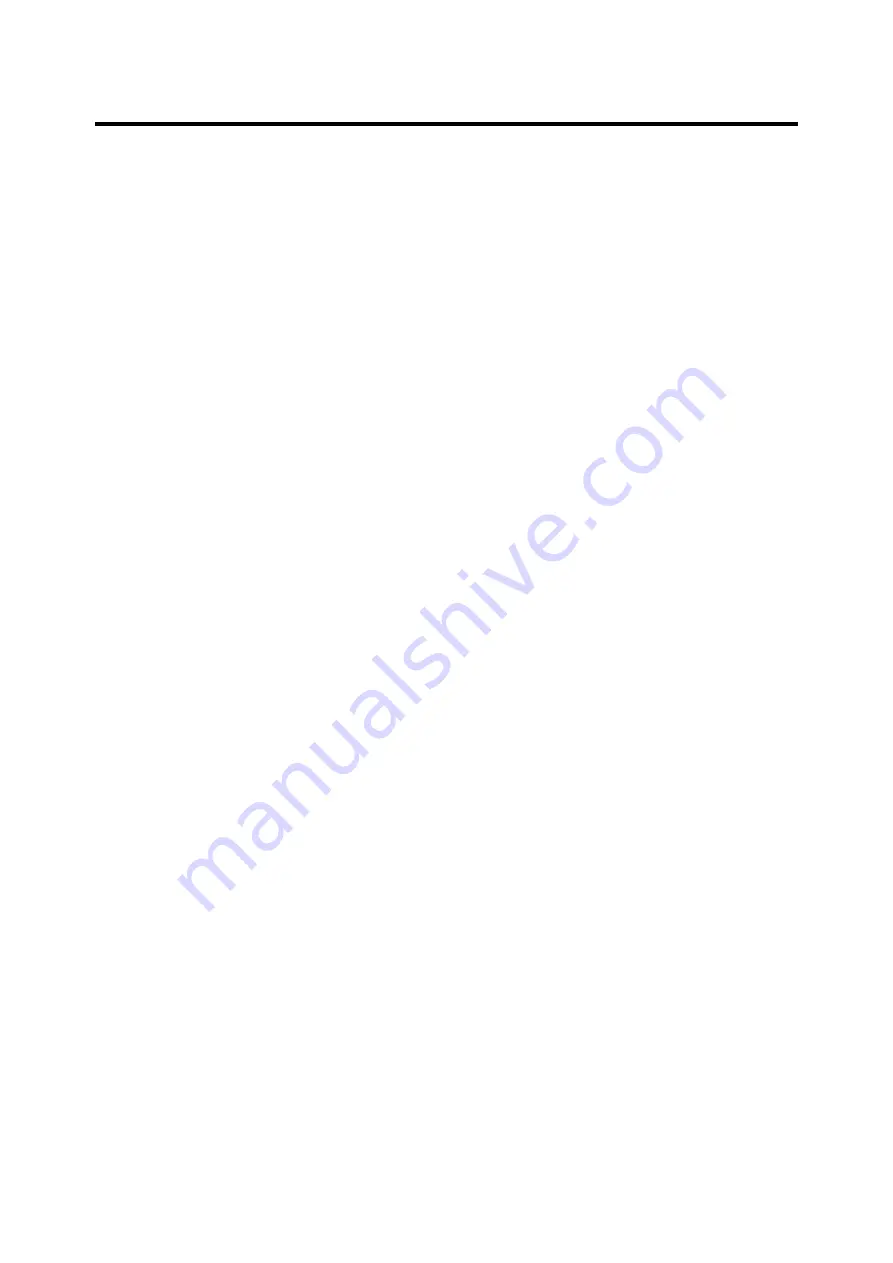
3
.
0 OPERATION
for the piping schematics. Each vertical screw
compressor discharges hot and high pressure gas
through a discharge service valve (or check valve
in multiple compressor units) into the condenser,
where it condenses by rejecting heat to water
inside the tubes. The liquid refrigerant drains to
the bottom of the condenser and exits via the
economizer feed line.
The refrigerant flows through the economizer
feed ball valve, in which its pressure drops, and
thus it flashes. It then flows into the flash
economizer tank which is at an intermediate
pressure between condenser and evaporator.
Liquid refrigerant is centrifugally separated from
the flash gas and the liquid drains to the bottom of
the tank, exits via the economizer drain line, and
passes through the economizer drain ball valve.
Both economizer ball valves are actuated by a
Modutrol motor that adjusts flow to maintain an
appropriate refrigerant level in the evaporator,
which is determined by a liquid level float switch.
From the drain line, liquid refrigerant flows into
the flooded evaporator, where it boils, by
absorbing heat from the water flowing inside
evaporator tubes. Vapor from the boiling
refrigerant flows up the suction pipes through a
shut-off valve (optional), suction check valve and
suction filter (inside compressor) into the
compressor where it is compressed and starts the
cycle again.
Vapor flowing from the top of flash economizer
will be injected into the compressor at the vapor
injection port, which feeds it into the compressor
part way through the compression process. Check
valve prevents backflow at shutdown in multi-
compressor units. All compressors operate in
parallel on a common evaporator and condenser.
3.6 OIL
MANAGEMENT
SYSTEMS
(See Fig. 3.5.)
3.6.1 WCFX 10-18
The compressor is oil lubricated and
discharges a small amount of oil mist
along with refrigerant. This oil is carried
into the evaporator. Oil rich refrigerant is
returned from the evaporator through a
tap in the shell, oil return valve, filter
drier, angle valve, sight glass and into jet
pump installed on the suction line. The
jet pump is powered by high pressure
gas from the compressor discharge line
through hot gas feed valve. This forces
the oil rich mixture from the evaporator
through oil return valve into the suction
line where it is carried into the
compressor.
The hot gas valve should be opened
enough only to allow good oil return
when the unit is fully unloaded. (1/8 to
1/2 turn). Excessive oil return will lower
discharge superheat un-desirably. The oil
return valve should be left wide open.
In normal operation, no oil level will be
visible in the compressor sight glass.
3.6.2 WCFX 20-54
The compressors are oil lubricated and
discharge a small amount of oil mist
along with refrigerant. This oil is carried
into the evaporator. Oil rich refrigerant is
returned from the evaporator through
two taps in the shell, a filter-drier and
isolation valve, and into a manifold that
serves all compressors. At each
compressor, this oil rich liquid flows
through a check valve, sight glass, and
into a jet pump which feeds through an
isolation valve then into the compressor
suction line.
Oil overflow feeds from the C4 port on
the compressor through an overflow
valve, sightglass, and check valve, and is
shared between compressors by feeding
through the overflow feed solenoid
valves into the operating compressors.
3.7 HYDRAULIC
CAPACITY
CONTROL SYSTEM
(See Fig. 3.7.)
Each compressor has a hydraulic control system
to position the capacity control slide valve, in
order to regulate compressor capacity. It is
composed of a normally closed solenoid valve, a
normally open solenoid valve and internal
pressure regulating valve.
- 30 -
Содержание WCFX 10
Страница 8: ...TWO PASS RIGHT HAND ARRANGEMENT SHOWN 1 0 GENERAL INFORMATION WCFX 20 22 24 27 30 33 36 8...
Страница 9: ...1 0 GENERAL INFORMATION WCFX 39 42 45 48 51 54 9...
Страница 31: ...3 0 OPERATION FIGURE 3 5 PIPING SCHEMATIC 1 1 COMPRESSOR WCFX 10 12 15 18 31...
Страница 32: ...3 0 OPERATION 2 2 COMPRESSORS WCFX 20 22 24 27 30 36 32...
Страница 33: ...3 0 OPERATION 3 3 COMPRESSORS WCFX 39 42 45 48 51 54 33...
Страница 36: ...4 0 ELECTRICAL FIGURE 4 2 TYPICAL WIRING SCHEMATIC A 1 COMPRESSOR 36...
Страница 37: ...4 0 ELECTRICAL 37...
Страница 38: ...4 0 ELECTRICAL B 2 COMPRESSORS 38...
Страница 39: ...4 0 ELECTRICAL 39...
Страница 40: ...4 0 ELECTRICAL 40...
Страница 41: ...4 0 ELECTRICAL C 3 COMPRESSORS 41...
Страница 42: ...4 0 ELECTRICAL 42...
Страница 43: ...4 0 ELECTRICAL 43...
Страница 44: ...4 0 ELECTRICAL 44...