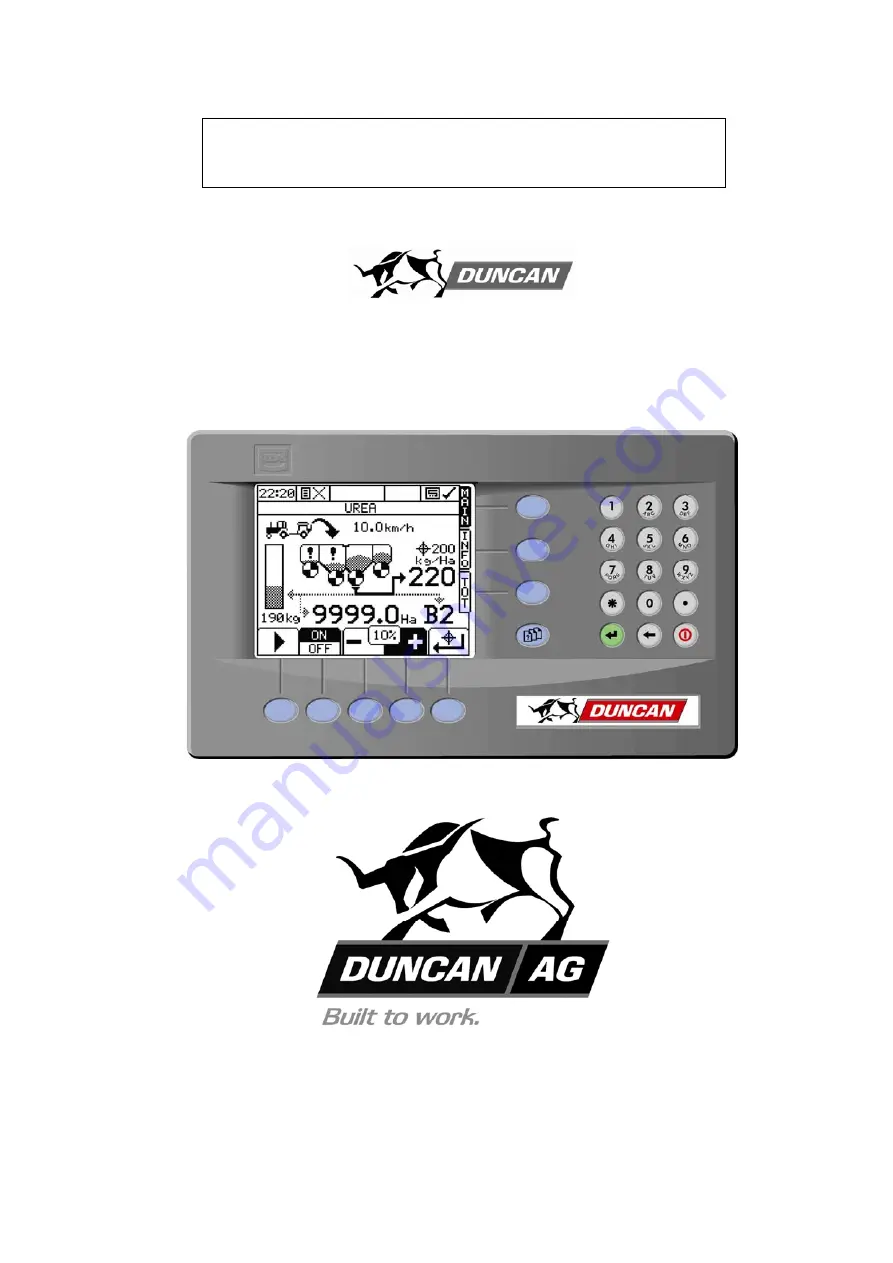
Pt. No. 67385
Issue
1005
Owners Manual
Duncan Drill
Electric Drive System
Head Office:
Australian Branch:
P.O. Box 2018
4B Silverton Close
Hilton Highway
Laverton North
Timaru, New Zealand
Melbourne, Australia
Telephone (03) 688 2029
Telephone (03) 9314-9666
Facsimile (03) 688 2821
Facsimile (03) 9314-6810
Содержание Enviro 3000e
Страница 2: ......
Страница 24: ...22 Enviro 3000e Seed Drill Calibration Notes ...
Страница 25: ...23 Pt No 67303 Issue 0806 Enviro 3000e Seed Drill Calibration Notes ...
Страница 32: ...30 Enviro 3000e Seed Drill Maintenance Notes ...
Страница 34: ......
Страница 38: ...4 61 60 70 63 64 65 66 67 68 71 62 59 69 ...
Страница 40: ...6 3 9 6 17 28 19 33 34 35 7 36 8 1 10 14 11 25 20 13 24 29 26 27 31 9 31 2 22 23 32 30 4 5 18 12 15 16 21 ...
Страница 46: ...12 5 6 ...
Страница 60: ...26 1 1 2 3 3 4 4 5 6 6 7 7 8 8 9 9 10 10 11 14 ...
Страница 62: ...28 4 3 1 13 15 16 11 17 7 5 8 6 2 9 14 12 12 11 10 10 11 12 Not Shown ...
Страница 64: ...30 2 2 1 8 9 2 5 5 3 4 3 4 6 6 7 3 10 7 ...
Страница 66: ...32 Enviro 3000e Seed Drill Operator Notes ...
Страница 68: ...1 ...
Страница 95: ...28 Figure 33 Motor control module offline A B C D E F G H I ...
Страница 101: ...34 Figure 43 NUDGE screen 3 A B C D E F G H I ...