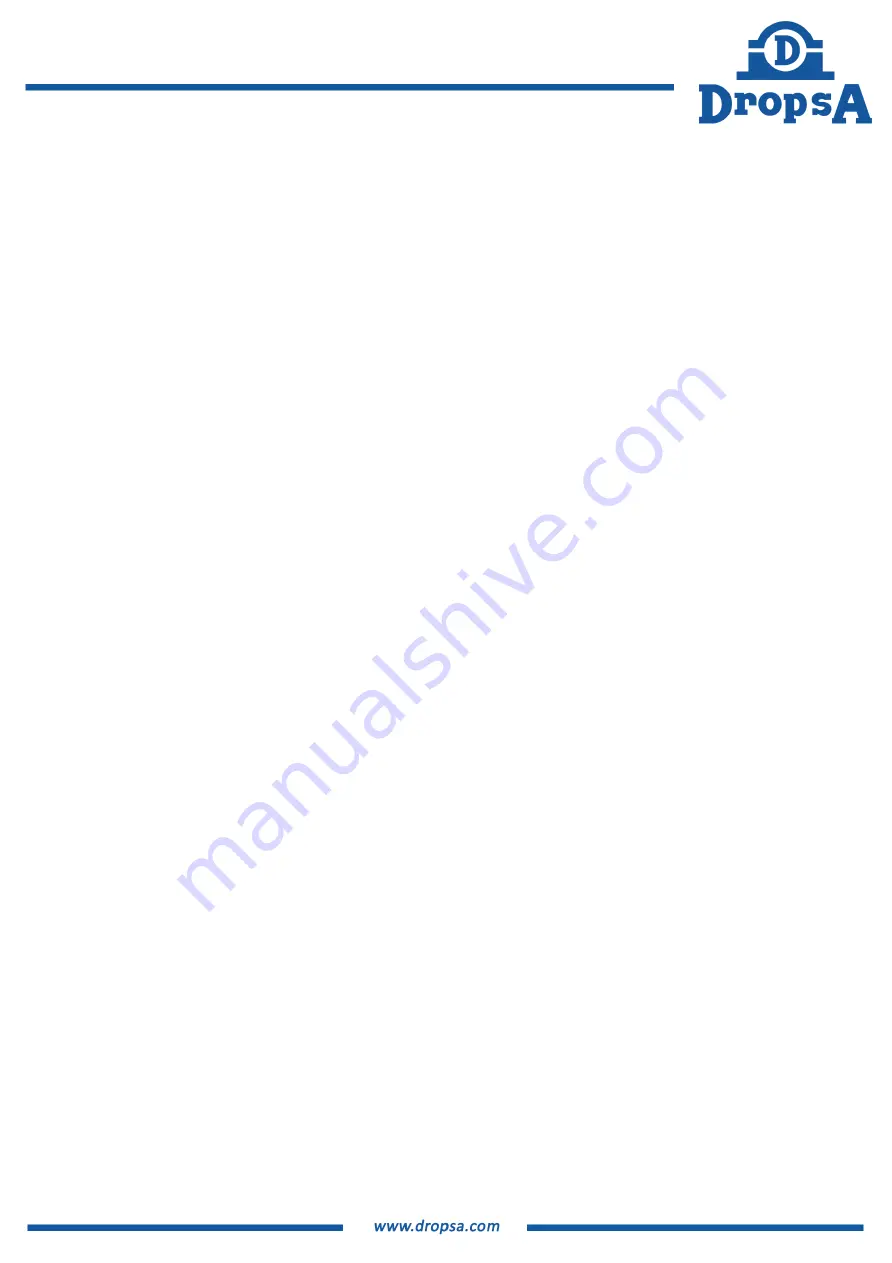
5
2. STRUCTURE AND OPERATION
2.1 LP/HP CIRCUIT OPERATION
The system consists of a pressurised lubricant reservoir with air. The lubricant contained in the tank (1) is sent through
a pipeline inside the tank itself, to the generator nozzle (3) located inside the generator head, as a result of the
pressure from the air, regulated by the valve (2).
The oil previously regulated by the valve (4) meets the airflow placed in rotation at high speed, thus splitting into
micro-particles that form the aerosol mist conveying with the opening of the electro-pneumatic valve (14), towards
the use in the CNC chamber.
By simply turning the valve (4), the quantity of oil introduced into the circuit is defined in % according to the position
of the ball on the flowmeter (11), and the fog density is varied accordingly. (only for LP mode).
Even if totally closed, the valve (4) allows a minimum oil passage that can guarantee minimum lubrication.
The flowmeter has reading integrated for both HP / LP operating modes.
The left scale reading indicates oil supply on LP circuit, while right scale indicates oil supply on HP circuit.
In case of high airflow rates, the valve (5) feeds additional air into the tank in order to keep the pressure in the tank
constant.
(Ref sheet 1 – Page 6)
When using drills with very small lubrication diameters, there is an increase in pressure in the reservoir. This condition
causes the pneumatic valve (10) to open the high-pressure duct, thus activating the multiplier (8) (if present) or
external accessory connected to the port (7).
In this situation, the pressure inside the tank will tend to increase, thus closing the check valve (9). Increased pressure
will facilitate the release of machining waste material, ensuring continuous tool cooling/lubrication
. (Ref sheet 2 -
Page 6)
There is no oil regulation on the HP circuit.
The oil can be filled from the port (16) or the valve (15), which also acts as an oil drain.
The max/min oil level in the tank is directly observable from the pipe (12) located on the tank.
Note: The oil level must not exceed the reference on the tank.
When topping up, make sure to exclude the mains air by acting on the valve (18), discharge the residual pressure
contained in the tank by acting on the quick-release valve (22).
It is also possible to connect a minimum level alarm (13) directly to the connector under the equipment in order to
prevent machining without lubricant when the system is unattended.
(Ref sheet 1 – Page 6)
Note:
A single nozzle version is available in which the HP circuit is deactivated.
2.2 HP CIRCUIT DRIVE WITH REMOTE CONTROL
It is possible to mount an ON/OFF solenoid valve (21) externally controlled by the CNC that controls the intervention
of external accessories.
In this case, it is preferable to deactivate the pneumatic valve (10) by completely unscrewing the adjustment screw on
the valve itself. (
Ref sheet 3 – Page 6)
In case of maintenance, it is possible to eliminate the residual pressure on the multiplier circuit by opening the valve
(23) and energising the ON/OFF solenoid valve (21) if present.
ADVANTAGES:
Reduction of the cycle time: from 25% to
80%.
Reduction of the quantity of lubricant
required
Longer utensil life
Improved finishing of the pieces
Application:
Machine tools;
Sheet metal cutting and bending machines;
Steel mills.