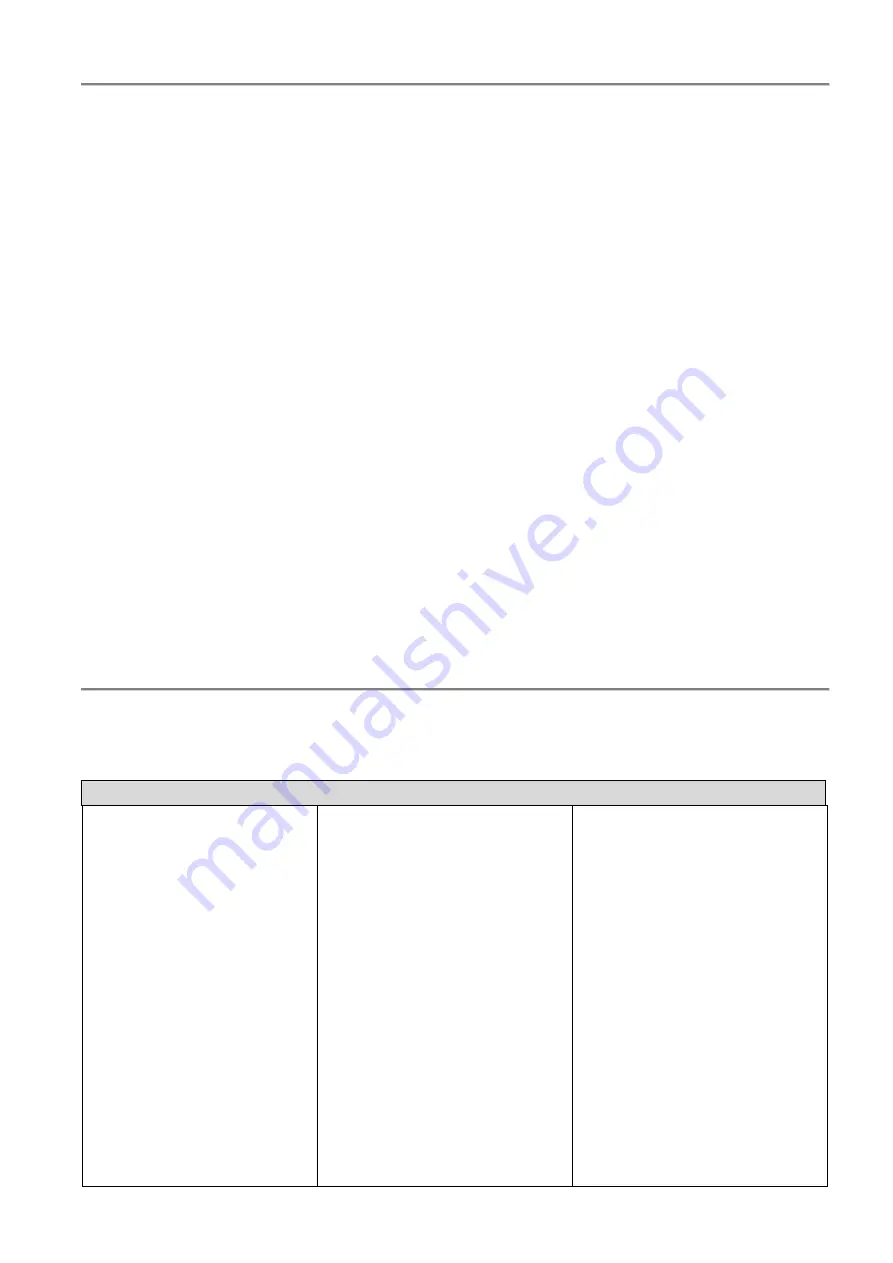
5
7. PUMP OPERATION
7.1 COMMISSIONING THE PUMP
•
The unit can only be opened and repaired by authorized Dropsa personnel.
•
Do not use the pump submerged in fluids, in aggressive environments such as close to extremely hot
substances, flammable or explosive material whether the supplier has not specifically prepared the
pump for it.
•
Always wear safety glasses and gloves when working with pneumatic and hydraulic systems.
•
Do not use abrasive lubricants with gaskets NBR. In the event of doubts, contact the Dropsa technical
centre that will provide all details on indicated lubricants.
•
Do not ignore hazards for health and observe hygienic rules.
•
Always use tubing suited for the specific working pressure.
Before using the pump, it is necessary to perform some preliminary checks:
•
Check the integrity of the pump; ensure there is no physical damage.
•
Fill the Oil reservoir with suitable lubricant (see instructions min/max on the reservoir).
•
Check the pump working temperature and ensure there is no trapped air within tubing.
•
Check electrical connections have been carried out correctly (CEI 64/8, IEC 364).
•
Check level control panel connections and their operating status.
7.2 USING THE PUMP
•
Check set data on the panel.
•
Push the start button of the machine to which the pump is connected.
•
Check
pump
commissioning.
•
Ensure the machine is properly lubricated (in the event of doubts, contact the Dropsa technical centre to
request the testing procedure.
8. TROUBLESHOOTING
The following table highlights some of the most common problems encountered when using the
Locopump and how to resolve them.
In the event of doubts or problems not listen, do not dismantle the pump but contact a DropsA technical
centre for assistance.
DIAGNOSTIC TABLE
PROBLEM
The pump starts but does not
deliver lubricant or delivers
different quantities from the
required discharge.
The pump does not deliver
lubricant at the set pressure or
does not keep the working
pressure.
PROBABLE CAUSE
o
The reservoir has insufficient oil.
o
The control valve does not
discharge.
o
Fittings may have become lose.
o
Incorrect adjustment of the
control inlet air pressure.
o
The check valve may be
damaged or clogged.
SOLUTION
o
Fill the oil reservoir. Do not
exceed the max. level.
o
Check the pump control valve 3
ways is normally discharging
compressed air.
o
Tighten any loose fittings on the
pump or the lubrication system.
o
Adjust properly the air pressure
within the established range of
pressures considering the
compression ratio.
o
Clean or change the valve
(chapter 6.6 point F) which is
comprised in the kit 3132671