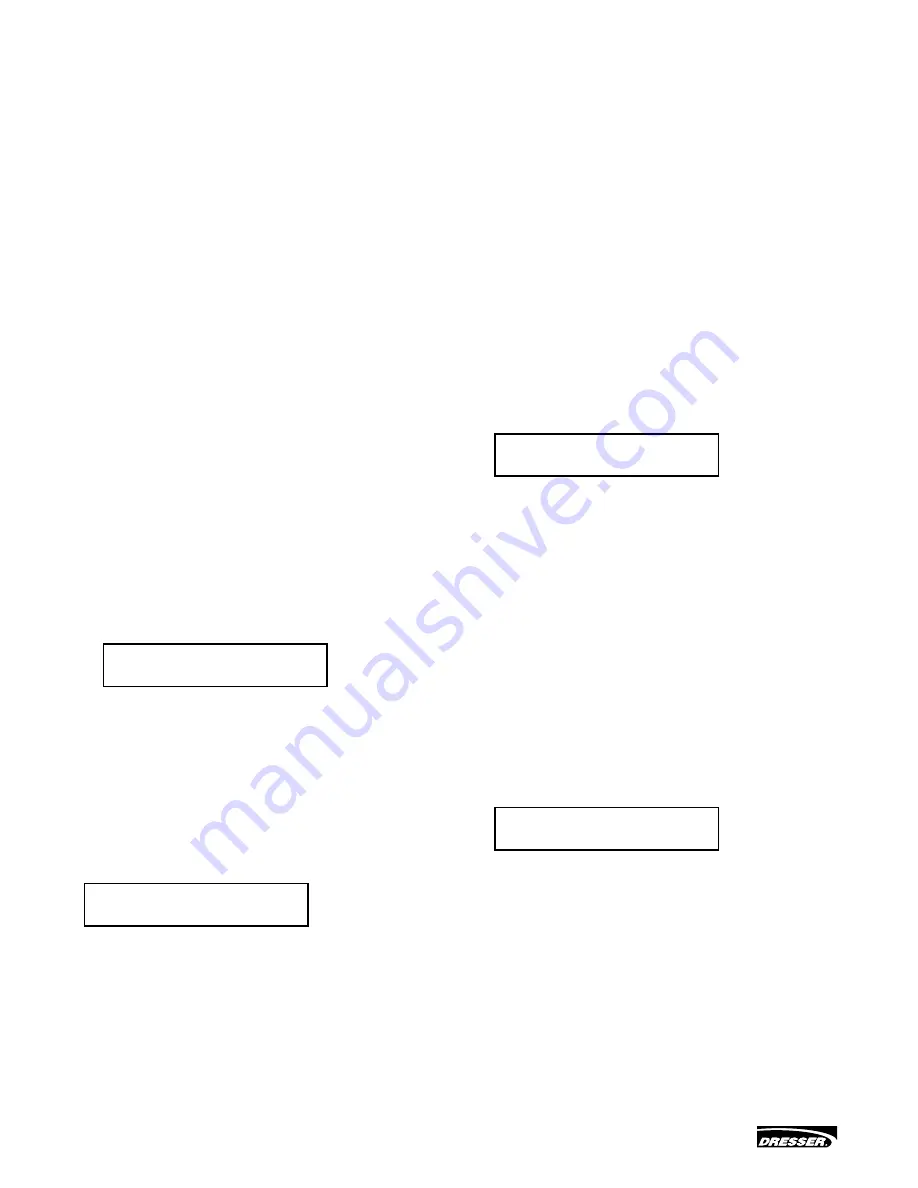
Instructions EF35002 - 08/10
Camflex
®
II 35002 Series Control Valves
4
C.
To allow for in-line inspection, maintenance or removal of
the valve without service interruption, provide a manually
operated stop valve on each side of the Camflex
®
II valve
with a manually operated throttling valve mounted in the
by-pass line.
Note: If a flanged Camflex
®
II is being installed and the
distance between flanges is established by ANSI or DIN,
spool pieces (spacers) are inserted between the line flange
and the valve body flange. Gaskets and valve bolting are
then installed and torqued using standard flange and line
bolting criteria.
D.
For flangeless valves, refer to Figure 23 and determine the
correct size and quantity of bolts to be used for the valve and
flange rating.
E.
If the valve is to be installed in a horizontal position, install the
lower flange bolting to provide a cradle, which will help support
the valve while installing the remaining bolts.
F.
Place the valve in the line.
G.
Select and install correct gaskets.
Note: Spiral wound gaskets, suitable for service conditions
are recommended.
H.
Insert remaining flange bolting ensuring that the bolts align
with the special bosses on the body, which assure the valve is
centered in the line and also prevent rotation.
Note: For certain flange standards, through bolting is not
possible because of the valve body neck or bonnet. To
accommodate flange bolting, guide arms with threaded
holes or slots are provided on the valve body to receive
flange bolts (refer to Figure 22).
I.
Tighten flange bolts evenly and firmly.
CAUTION
CAUTION
WARNING
DANGER
If the valve is to be insulated, do not insulate the valve bonnet.
Note: If the valve is equipped with manual handwheel, it
may now be placed in service.
6. Air Supply Piping
Air is supplied to the actuator through the 1/4" NPT tapped
connection in the diaphragm case. Refer to Figure 14 to
determine the correct supply pressure and tubing size, then
connect air supply piping.
CAUTION
CAUTION
WARNING
DANGER
Do not exceed maximum air pressure indicated. Personal injury
and equipment malfunction could result.
Note: When the valve is equipped with regulators or other
accessories supplied by Masoneilan, only connections to
those accessories are required since the piping to the actua-
tor is connected at the factory. Some valves equipped with
electrical accessories will require appropriate wiring. Refer to
manufacturer’s instructions for correct wiring information.
7. Placing in Service
With the valve properly installed in the line and all air or electrical
service connected, it is recommended that the valve be run
through one cycle to ensure proper functioning. Proceed as
follows:
A.
Back off the handwheel (53) so that it will not interfere with the
operation of the valve and tighten the handwheel lock (52).
Note: If the valve is equipped with the optional limit stop
(77), it should also be backed off to prevent interference
with the operation of the valve.
B.
Apply correct air pressure to the actuator.
Note: Valve should function smoothly and with maximum
pressure, the valve indicator (6) should show full open or
full close depending on valve mode.
C.
Relieve air pressure and return valve to normal mode.
D.
Gradually open process lines to place the valve in service.
E.
Check for leaks. Repair as required.
CAUTION
CAUTION
WARNING
DANGER
Always ensure process pressure, air pressure and electrical
service are off and the valve is isolated and relieved of
pressure before performing maintenance on the valve.
F.
If desired, the handwheel may be used as a limit stop. Set in
desired position and lock.
G.
If the optional limit stop (77) is used, set and tighten locknut.
8. Disassembly
8.1 Actuator Removal From Body S/A (Refer to
Figure 16 and Figure 17)
Maintenance required on the internal components of the
valve or re-orientation of the actuator and body, requires that
the actuator and yoke be removed from the valve. On the size
6, 7 and 9 actuators, for ease of handling and reassembly, it
is recommended that the spring barrel be removed from the
yoke and then the yoke separated from the valve body.
CAUTION
CAUTION
WARNING
DANGER
Prior to performing maintenance on the valve, isolate the
valve, vent the process pressure and shut off supply and
signal air lines to the actuator.
Note: If the valve will be reassembled in the same
orientation, it is recommended that the body to yoke
orientation and the actuator to yoke orientation be marked
in relation to each other. This will simplify reassembly.
A.
If required, remove the valve from the line.
B.
Remove rear cover (29) and front cover (32) by removing
the two cover screws (30).
C.
Remove bottom cover (11) and spring barrel boss
cover (58).