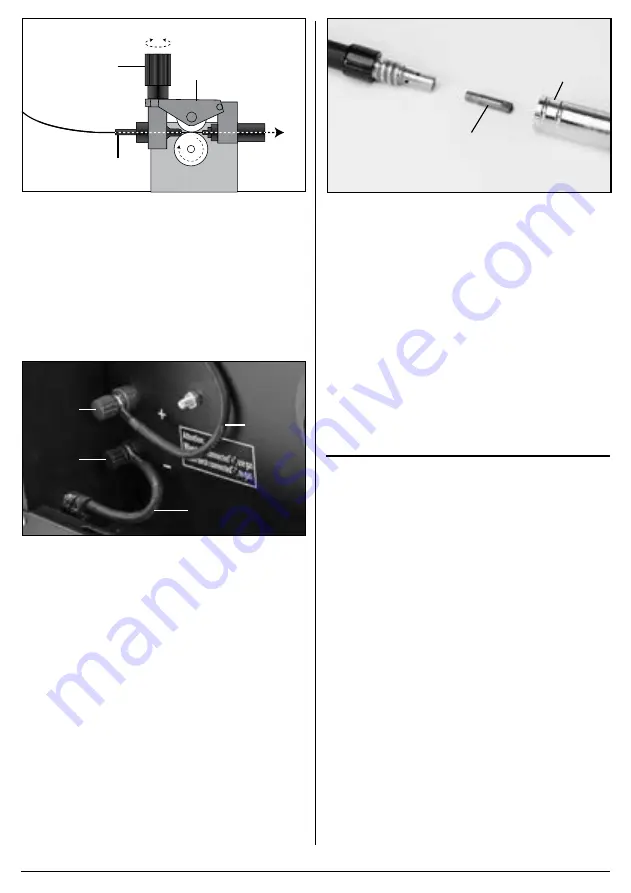
– 8 –
2
FIG.
(11.1)
(11.2)
(11.3)
8. GASLESS (no-gas / flux cored).
The polarity of the torch and earth clamp must be
made correctly to suit the gas setup.
i. Attach the earth clamp connector
(10.1)
to the
positive terminal
(16.1)
.
ii. Attach the welding torch connector
(11.1)
to the
negative terminal
(16.2)
.
Note:Reverse the torch and earth clamp for gas
welding.
3
FIG.
(16.1)
(10.1)
(11.1)
(16.2)
9. Press the feed trigger on gun and observe the wire
feed mechanism. If the wire is being fed correctly it
will come out of the swan neck. If it jams you will
need to remove the gas shroud
(2.1)
and with a
small spanner unscrew and remove the tip
(2.2)
.
Pass the tip over the wire and secure back onto the
swan neck. Do not over tighten. Resecure the gas
shroud and trim the wire back as required.
Note: Ensure the tip size matches the wire size prior to
installing.
4
FIG.
(2.2)
(2.1)
7.5 NO GAS WELDING PRINCIPLE
For a successful weld joint, the molten metal must be
protected from contaminating gases found in the air.
This is achieved by using a flux cored filler wire. The flux
is produced as the wire melts.
The flux creates a coating over the weld and once
cooled will need to be removed by chipping it off.
If allowed to cool naturally some areas of the flux may
ping off of the weld by themselves due to thermal
contraction for this reason it is recommended that eye
protection is worn.
8. BASIC WELDING
OPERATION
NOTE: Although this machine is medium weight and
portable take care.
Note: Welding is a mix of science and art and due to the
complex principles and vast differences in parameters
(ie. Material type, position, condition etc.) That
information is well beyond the scope of this manual.
Draper Tools suggest training be obtained from a third
party or refer to a suitable reference book on the subject
additionally; nothing can beat practice using the welder
on scrap material to get a better understanding.
8.1 ON/OFF SWITCH - FIG. 5
The on/off switch is a rocker switch. Press the top half in
to switch the welder ‘on’ and the bottom half in to switch
the welder ‘off’.