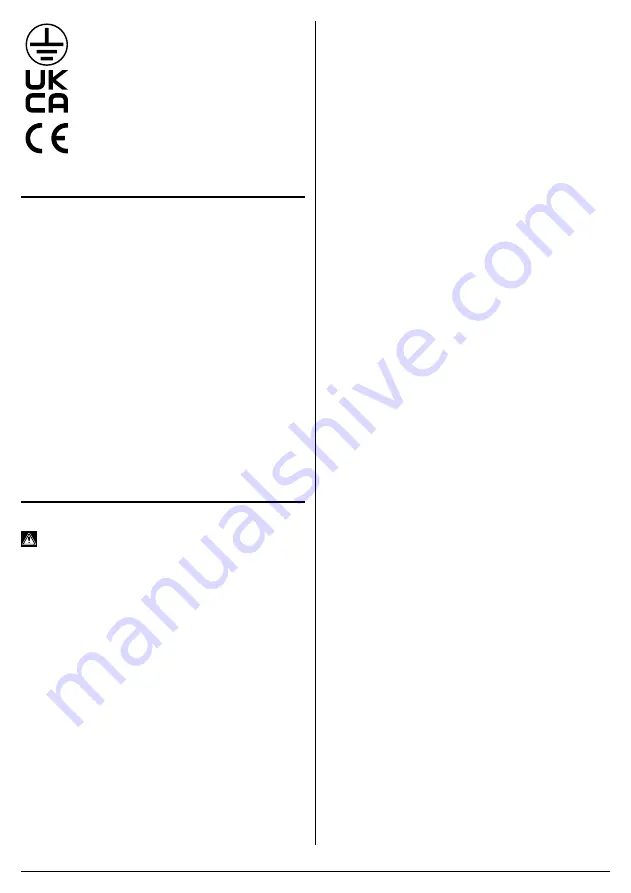
– 3 –
Class 1 appliance
(Must be earthed).
UK Conformity Assessed
European conformity.
2. SPECIFICATION
2.1 SPECIFICATION
Stock No. .............................................................. 71095
Part No. ........................................................... MW170T
Rated voltage .................................................. 230~50Hz
Input current .............................................................. 16A
Current range ................................................... 60 - 160A
MIG wire range ............................................. 0.6 - 0.9mm
MIG Wire Spool .......................................................... 1kg
Degree of protection .............................................. IP21S
Cooling ............................................................... Air (fan)
Insulation class ............................................................. H
Duty cycle: .............................. 10% @ 160A 60% @ 65A
Weight (Net) ............................................................ 32kg
3. HEALTH AND SAFETY
INFORMATION
3.1 General Safety Instructions
Warning! Read all safety warnings and all
instructions. When using electric tools basic safety
precautions should always be followed to reduce the risk
of fire, electric shock, and personal injury including the
following.
Read all these instructions before attempting to operate
this product and save these instructions.
Electric shock can kill:
– Remove the plug from the socket before carrying out
adjustment, servicing, or maintenance.
– Allow 5 minutes waiting time for the capacitors to
discharge before removing the panels for any
maintenance operations
– Do not touch live electrical parts.
– Never use electrode holders or cables with damaged
or deteriorated insulation.
– Keep the working environment, equipment, cables,
and clothing free from grease, oil, moisture, and dirt.
– Ensure the welding machine has been correctly
earthed and all panels are fitted securely.
– The operator must be insulated from the floor and
workbench using a dry insulation mat.
– Wear isolating footwear and gloves that are in good
condition, i.e. without holes.
– In hazardous conditions of increased electric shock
always ensure a second person is present in case of
an accident.
– Never change electrodes with bare hands or damp
gloves (for ARC/MMA welders).
– Keep welding cables away from power cables.
– Regularly inspect the condition of the welding, earth,
and power cables for signs of damage.
– Do not leave the machine unattended and remove
the plug from the socket when not in use.
– Do not use welding cables unsuitable for the
amperage.
– Ensure the earth clamp is adjacent to the weld seam,
secured to bare metal and when not in use is
insulated for safety.
– Keep all equipment well maintained.
– The operator shall prevent gas cylinders in the
vicinity of the workpiece from becoming part of the
welding circuit.
Fumes & Gases can be harmful:
– The welding process generates hazardous fumes as
a by-product. Inhalation of these fumes is hazardous
to health.
– Keep your head away from the weld to avoid
breathing the fumes.
– If welding in confined spaces ensure adequate
ventilation and use a fume extractor.
– Welding fumes displace oxygen. The danger of
suffocation.
– By-products of welding can react with other chemical
vapours to produce a toxic/explosive environment.
Welding can cause fire or explosion:
– Arc welding and allied processes can cause fire and
explosions and precautions shall be taken to
prevent these hazards.
– Before starting a weld ensure the area is clear of
flammable materials.
– Remove any inflammables to a safe distance,
especially substances likely to generate a dangerous
vapour.
– The welding arc can cause serious burns. Avoid
contact with skin.
– Sparks and molten metal are cast out during
welding. Take precautions to prevent fire igniting and
wear protective clothing.
– Sparks and molten metal can pass through gaps. Be
aware that fire can start out of sight. Flammables in a