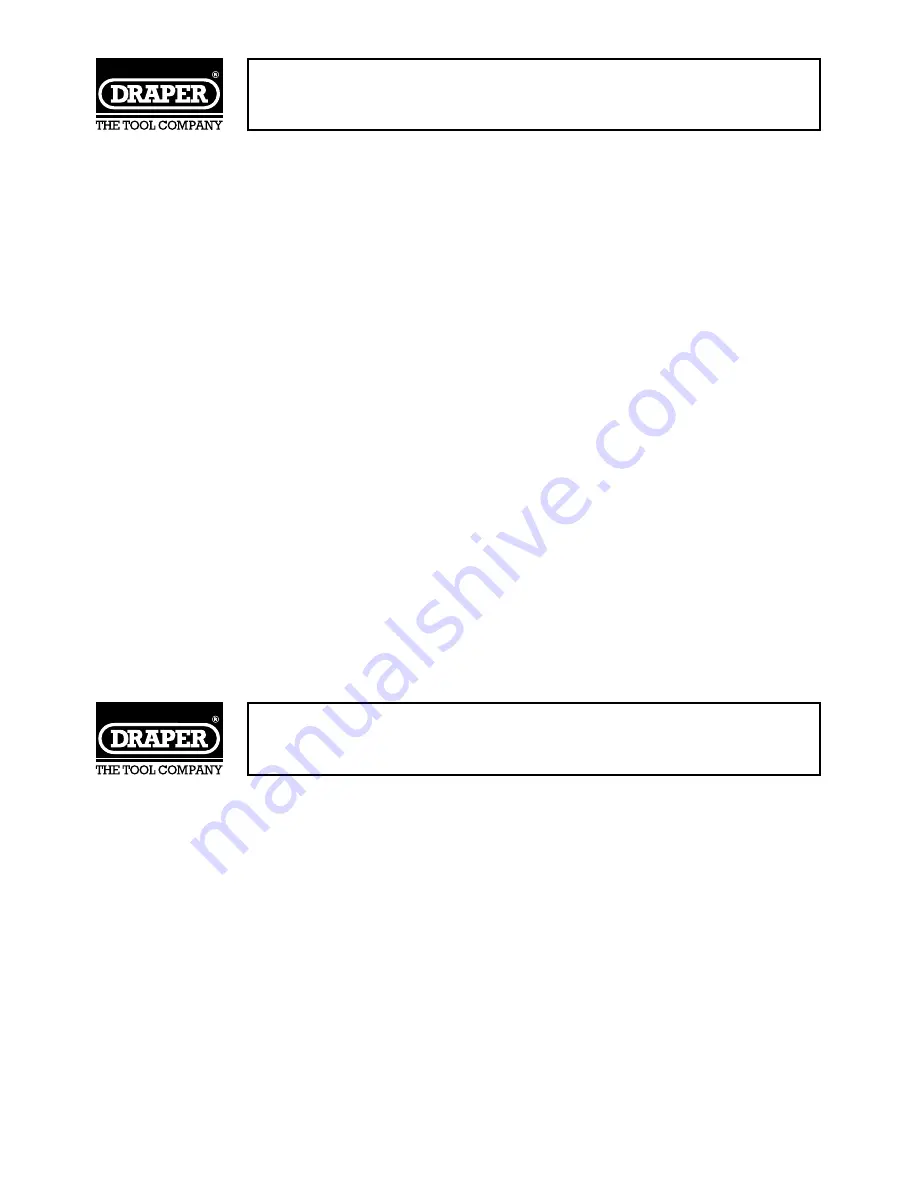
- 9 -
OPERATING INSTRUCTIONS
GRINDING TIPS
A bench grinder is designed for hand grinding operations only, such as sharpening drill bits,
chisels and screwdrivers or removing excess metal from workpieces.
A coarse grit grinding wheel could be used for grinding rough metals, to remove large amounts of
metal, or where a smooth finish is not important.
A fine grit grinding wheel could be used for sharpening tools or grinding close to size. A fine grit
wheel removes a metal more slowly and therefore gives the workpiece a smooth finish and does
not generate enough heat to anneal the cutting edges.
1.
Check that there is a 1.5mm (
1
⁄
16
") clearance between the tool rests and the surface of the
grinding wheels. Adjust as necessary. Now check the gap between the spark deflectors and
the surface of the grinding wheels. These should also be 1.5mm (
1
⁄
16
"). Adjust as necessary.
The tool rests should be adjusted so that they are just below the centre line of the grinding
wheels. This should help prevent accidental jamming of the work between the tool rest and the
wheel.
2.
Check that the eye shields have been secured in the correct position and that the grinding
wheel lock nuts are tight.
NOTE: Before fitting a new grinding wheel to the bench grinder always carefully check the
wheel for damage such as chips, flaws or cracks. Then if the new wheel appears to be
satisfactory fit the wheel to the grinder. Stand to one side of the grinder and switch “ON”. Let
the grinder operate at full speed for approximately one minute so that any undetected cracks
or flaws in the wheel will become apparent.
3.
Stand to one side of the bench grinder, switch on and let it build up to full speed.
4.
When grinding, always keep the workpiece moving across the face of the wheel. Grinding
against the same part of the wheel will cause uneven wear of the wheel face.
5.
When necessary redress the grinding wheels using a wheel dressing tool. After redressing
adjust the tool rests and spark deflectors as necessary to maintain a 1.5mm (
1
⁄
16
") clearance
from the wheel.
1.
Ensure that the item to be ground is comfortably and securely held.
2.
Adjust tool rest to correct angle.
3.
Present the workpiece smoothly on to the grinding wheel face with a light and even pressure.
4.
Grind against the edge of the workpiece to avoid burrs.
5.
Never grind on the sides of the wheels.
6.
Best results are achieved if the grinder is allowed to rotate at its maximum speed. Excess
pressure from the workpiece can damage the wheel and overload the motor.
7.
Check grinding wheels regularly for wear or damage. Replace wheels that are worn more than
25%. Damaged wheels should be discarded immediately as they are dangerous and can cause
the grinder to vibrate.
8.
After grinding fine edge tools, they should be honed by hand on a fine slip stone.