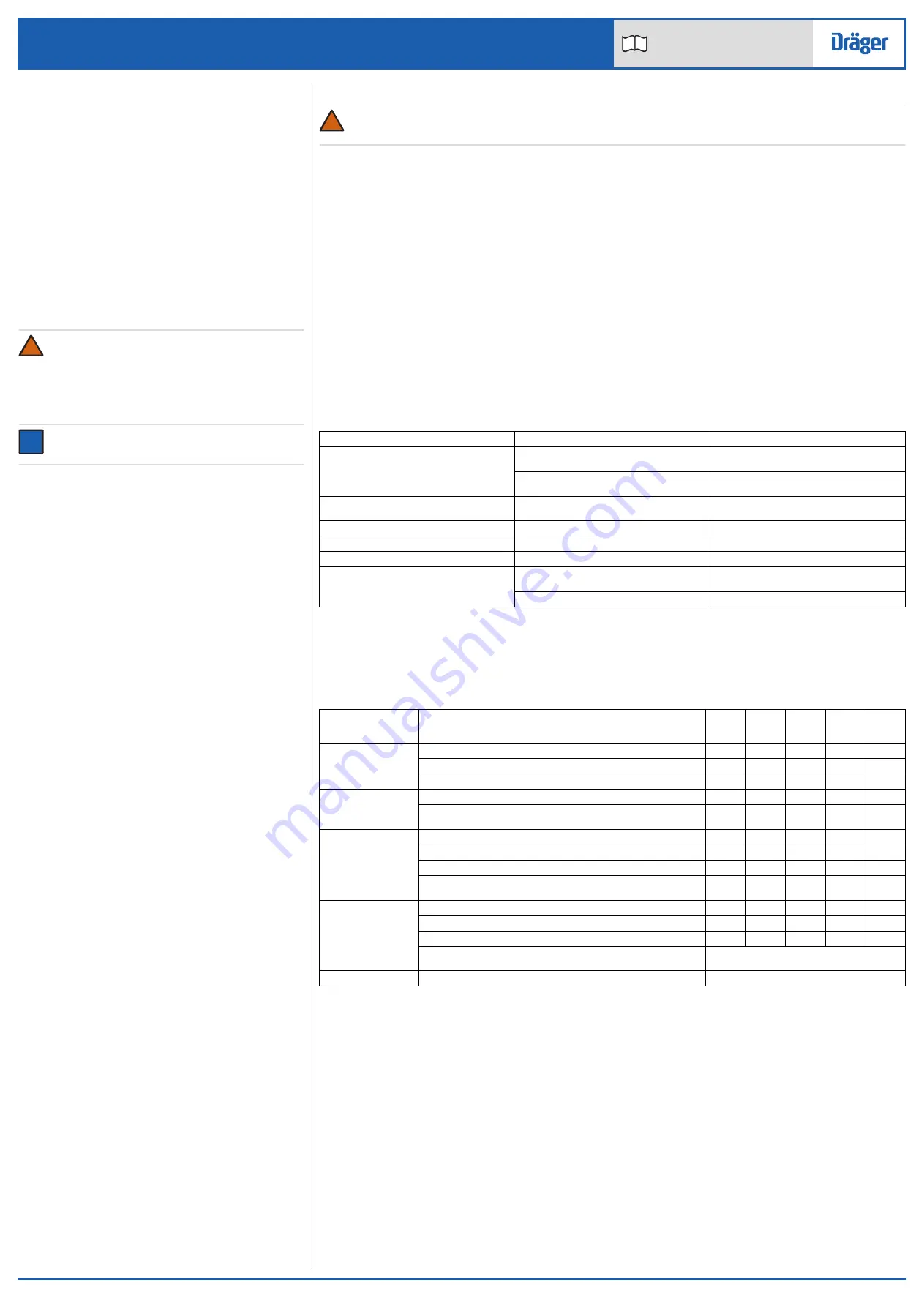
PSS
®
4000 Series
Self-contained breathing apparatus
Instructions for Use
i
Dow Corning
®
and Molykote
®
are registered trademarks of Dow Corning Corporation
3363923 (A3-D-P) Page 2 of 3
3. Press the rubber cover at the front of the lung demand valve to vent
the system fully. Press the reset button when using a positive-pressure
lung demand valve.
4. Release the waist belt buckle.
5. Lift the shoulder strap buckles to loosen the straps.
6. Remove the breathing apparatus and face mask.
7. Carry out the after use tasks in the maintenance table (see Section 5).
8. Remove the air cylinder (see Section 3.5.2) if required.
9. Pass the breathing apparatus to the service department with details of
any faults or damage that occurred during use.
3.5
Common user tasks
3.5.1
Visual inspection
A visual inspection must check the full breathing apparatus including all
component parts and accessories. Check that the equipment is clean and
undamaged, paying particular attention to pneumatic components, hoses
and connectors. Typical signs of damage that may affect the operation of
the breathing apparatus include impact, abrasion, cutting, corrosion and
discolouration. Report damage to service personnel and do not use the
apparatus until faults are rectified.
3.5.2
Air cylinder fitting and removing
WARNING
High-pressure air release may cause injury to the user or other
personnel near the breathing apparatus. Close the cylinder valve
and fully vent the system before attempting to disconnect an air
cylinder.
Impact damage to the cylinder valve or reducer connector may
prevent valve connection or cause an air leak. Handle the air
cylinder and breathing apparatus with care.
NOTICE
For other cylinder connector types, refer to the Instructions for Use
supplied for the connector.
Fitting a single cylinder
1. Check the threads of the cylinder valve port and the pressure reducer.
Ensure that the O-ring seal (Fig D, Item 1) and the sintered filter (2) in
the reducer are clean and undamaged.
2. Lay the apparatus horizontal, with the reducer uppermost, and fully
extend the cylinder strap.
○
Twin cylinder configuration: move the centre strap over the left-
3. Insert the cylinder through the loop of the strap, and align the valve with
the reducer.
4. Lift the cylinder and space frame into the vertical position (supported
on the end of the cylinder opposite the valve).
5. Tighten the hand wheel of the reducer, using only the thumb and index
finger, until a definite metal-to-metal contact is felt.
Do not
use tools or
over tighten.
6. Place the unit back into the horizontal position.
7. Take up the slack in the cylinder strap (Fig F).
○
Twin cylinder configuration: if fitted, feed the cylinder strap through
the metal buckle (Fig G, Item 1).
8. Pull the strap over the cylinder to operate the cam lock (Fig H).
9. Secure the strap end:
○
Single cylinder configuration: using the hook-and-loop fastener.
○
Twin cylinder configuration: feed the cylinder strap through the
metal buckle of the centre strap (Fig I) and secure using the hook-
and-loop fastener.
Fitting twin cylinders
Fitting twin cylinders requires a PSS
®
4000 variant capable of accepting
twin cylinders. Fitting twin 6 litre or 6.8 litre composite material cylinders
requires a compatible connector piece (see Section 2.2.1). Fitting twin
4 litre steel cylinders requires a compatible connector piece and slim hand
wheel (see Section 2.2.1).
1. Check the threads of the cylinder valve port and the pressure reducer.
Ensure that the O-ring seal (Fig D, Item 1) and the sintered filter (2) in
the reducer are clean and undamaged.
2. Lay the apparatus horizontal, with the reducer uppermost, and fully
extend the cylinder strap.
3. If not fitted, fit the connector piece on to the reducer (Fig J, T-piece
shown for illustrative purposes). Tighten the hand wheel of the reducer
using only the thumb and index finger until a definite metal-to-metal
contact is felt. Do not use tools or over tighten.
4. Insert the cylinder through the loop of the strap, and align the valve with
the connector piece.
5. Tighten the hand wheel of the connector piece as previously described
6. If required, fit the anti-vibration straps on to the hand wheel.
7. Take up the slack in the cylinder strap (Fig L).
8. Pull the strap over the cylinder to operate the cam lock (Fig M).
9. Secure the strap end using the hook-and-loop fastener (Fig N).
(Release the cam lock to adjust the position of the cylinder strap if
necessary.)
Removing a single cylinder
1. Close the cylinder valve and fully vent the system.
2. Lay the apparatus horizontal, with the cylinder uppermost.
3. Unfasten the cylinder strap.
4. Lift the strap against the cam lock to release the buckle tension, and
then loosen the strap.
5. Disconnect the cylinder valve from the pressure reducer.
6. Lift the cylinder away from the reducer and remove the cylinder.
Removing twin cylinders
1. Close the cylinder valves and fully vent the system.
2. Lay the apparatus horizontal, with the cylinder uppermost.
3. Release the cam lock, and then loosen the strap.
4. Remove the anti-vibration straps, if fitted, and fully unscrew the hand
wheels of the connector piece.
5. Lift the cylinders away from the connector piece and remove the
cylinders.
6. Remove the connector piece from the reducer.
!
i
i
3.5.3
Functional testing
WARNING
Failure of the breathing apparatus to meet any of the standards or parameters described in the functional tests indicates a system fault. Report
the fault to trained service personnel or contact Dräger. Do not use the breathing apparatus until the fault condition is rectified.
Leak test and whistle warning test
1. Press the reset button when using a positive-pressure lung demand valve.
2. Slowly and fully open the cylinder valve (anticlockwise). During pressurization a momentary sounding of the whistle will occur.
3. Fully close the cylinder valve.
4. After one minute, check the contents gauge and then reopen the cylinder valve. The gauge must not show an increase in pressure of more than
5. Fully close the cylinder valve.
6. Observe the contents gauge and slowly release the pressure as follows:
a. Cover the outlet port of the valve with the palm of the hand.
b. Press the rubber cover to switch on the positive pressure.
c. Vent the system by carefully lifting the palm of the hand from the outlet port to maintain a slow pressure decrease.
7. The whistle must begin to sound in the range 60 bar to 50 bar.
8. Continue to vent the system until fully exhausted.
9. Press the reset button when using a positive-pressure lung demand valve.
4
Troubleshooting
The troubleshooting guide shows fault diagnosis and repair information applicable to breathing apparatus users. Further troubleshooting and repair
information is available in Instructions for Use supplied with associated equipment.
Where the troubleshooting guide shows more than one fault or remedy, carry out repair actions in the order that they appear in the table.
Contact service personnel or Dräger when the remedy information indicates a service task, or if the symptom remains after all remedy actions have been
attempted.
5
Maintenance
5.1
Maintenance table
Service and test the breathing apparatus, including out-of-use apparatus, in accordance with the maintenance table. Record all service details and testing.
Refer also to the Instructions for Use for the lung demand valve, face mask and other associated equipment.
Additional inspection and testing may be required in the country of use to ensure compliance with national regulations.
Symptom
Fault
Remedy
High-pressure air leak or failed leak test
Loose or dirty connector
Disconnect, clean and reconnect couplings and
retest
Faulty hose or component
Substitute user replaceable accessories and
retest
Air leak from medium-pressure hose connection
at the pressure reducer (safety relief valve)
Faulty O-ring, retainer, spring or pressure
reducer
Service task
High or low medium pressure
Pressure reducer fault
Service task
Poor sounding whistle
Whistle dirty
Clean whistle flute and retest
Whistle not functioning correctly
Activation mechanism fault
Service task
Difficulty connecting or disconnecting the
medium-pressure quick coupling
Dirty connector
Disconnect, clean and reconnect couplings and
retest
Burring of the male coupling
Replace the hose with the male coupling
Component/System
Task
Before
use
After
use
Every
month
Every
year
Every
10
years
Complete apparatus
Visual inspection (see Note 1 and Section 3.5.1)
Notes
O Dräger recommendations
1
Clean the equipment if it is dirty. If it the equipment has been exposed to contaminants, disinfect any components that come into direct and prolonged
contact with the skin.
O
O
O
Functional testing (see Section 3.5.3)
O
O
O
Breathing cycle and static tests (see Note 2)
2
These maintenance tasks may only be carried out by Dräger or trained service personnel. Details of the tests are contained in the Technical Manual
which is issued to service personnel that have attended a relevant Dräger maintenance course.
O
Lung demand valve
Check push-in type connectors for lubricant (see Note 3)
3
For type A check the O-ring on the lung demand valve; and for type ESA check the outer surface of the male part of the push-in connector on the
lung demand valve. As a guide, lubricant should be felt on the fingers but not seen. If relubrication is required, lightly apply Dow Corning
®
Molykote
®
111 (other lubricants are not tested and may damage the equipment).
O
Check the male element of the quick coupling for burring (see Step 3 in
O
Pressure reducer
Medium-pressure check (see Note 2)
O
Inspect the sintered filter (see Note 2 and Note 4)
4
Replace the sintered filter if a drop in reducer performance is observed during a flow check or if it is visibly damaged.
O
Inspect the high-pressure connector O-ring (see Note 2 and Note 5)
5
Replace the high-pressure connector O-ring if it is found to leak during functional testing or if the O-ring is visibly damaged.
O
Overhaul. Contact Dräger for the Repair Exchange (REX) service
(see Note 6)
6
Where the breathing apparatus is subjected to a high level of use (in training establishments etc.), reduce the overhaul period for the pressure reducer.
In these circumstances, Dräger recommend that the overhaul frequency should be less than 5,000 applications of use. An application of use is defined
as a single use of the fully assembled breathing apparatus, where the user breathes from the air cylinder. It does not include system pressurization
for pre-operational checks.
O
Cylinder
Charge cylinder to correct working pressure
O
O
Check charged pressure (stored cylinders only)
O
Check test date of cylinder
O
Recertification
According to national regulations in the country of
use
Cylinder valve
Overhaul
At the time of cylinder recertification
!