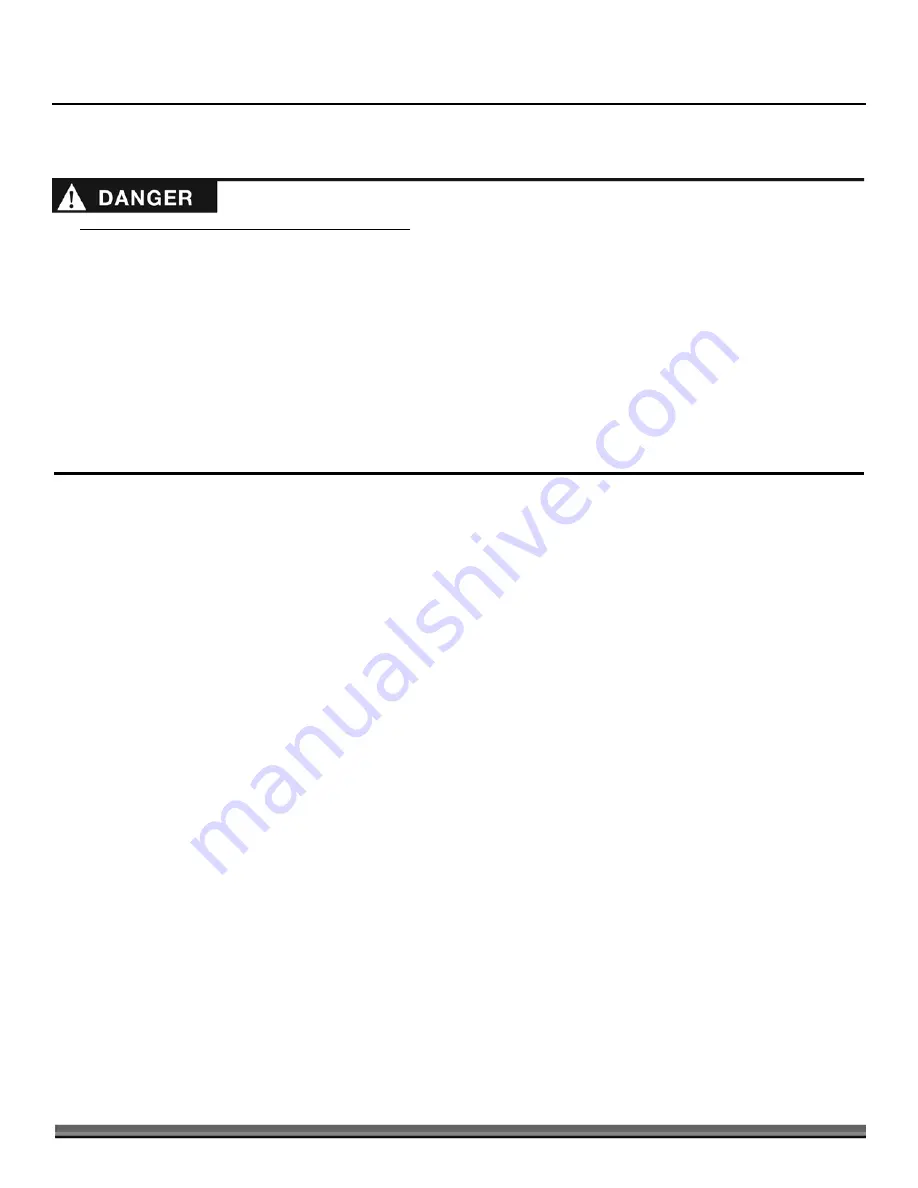
16
3-POINT HITCH
DR
®
SELF-FEEDING™ CHIPPER
Chapter 3: Operating Your 3-POINT HITCH DR SELF-FEEDING CHIPPER
This chapter covers the procedures for starting and stopping your new 3-POINT HITCH DR SELF-FEEDING CHIPPER and
discusses basic operation features.
Starting the Chipper
NOTE:
Some tractors may require the use of an
Over Running Clutch. Consult your local dealer for more information.
1.
Ensure that the Chipper is lowered to the ground and all Guards are in place and properly secured before using.
2.
Remove any debris buildup from the machine before every use of the Chipper.
3.
Set Tractor throttle at IDLE before engaging PTO with Chipper attached.
4.
Increase Tractor throttle to the RUN RPM’s required to obtain 540 PTO speed before chipping.
5.
Reduce Tractor throttle to IDLE before disengaging PTO.
NOTE:
Check the Drive Belt, if necessary, after an initial break-in period of one (1) hour (see Chapter 5 “Maintaining the 3-POINT
HITCH DR SELF-FEEDING CHIPPER”).
This machine is designed to operate at 540 rpm only! Never operate the machine at a faster speed; doing so can cause
serious injury to the operator or bystanders and could cause damage to the machine that is not covered under warranty.
The DR 3-Point Hitch Chipper must be operated with the weight of the machine on the ground. Operating the machine while
it is off the ground can result in injury to yourself or others, and can cause damage to the machine which is not covered under
warranty.
The design of this machine is for chipping wood. Never use this machine for any other purpose as it could cause serious
injury.
Contact with internal rotating parts will cause serious personal injury. Never put hands, face, feet, or clothing into chipper
hopper or discharge opening or near the discharge area or PTO shaft at any time.
Disengage PTO, shut down the tractor engine, remove the key, wait for all moving parts to come to a complete stop,
disconnect the PTO shaft from the tractor, then wait 5 minutes before moving or performing maintenance/inspection on the
chipper. Use only a wooden stick to clear jammed material.
Never operate the machine without the hopper or discharge chute or PTO shaft properly installed.
Содержание 372111
Страница 4: ...4 3 POINT HITCH DR SELF FEEDING CHIPPER 250581 227391 248791 248831 248841 248811...
Страница 33: ...CONTACT US AT www DRpower com 33...
Страница 35: ...CONTACT US AT www DRpower com 35 Schematic Frame and Drive Assembly...
Страница 37: ...CONTACT US AT www DRpower com 37 Schematic Chipper Basic Assembly...
Страница 39: ...CONTACT US AT www DRpower com 39 Schematic Hopper Assembly...
Страница 41: ...CONTACT US AT www DRpower com 41 Schematic Extended Top Discharge Chute...
Страница 43: ...CONTACT US AT www DRpower com 43...