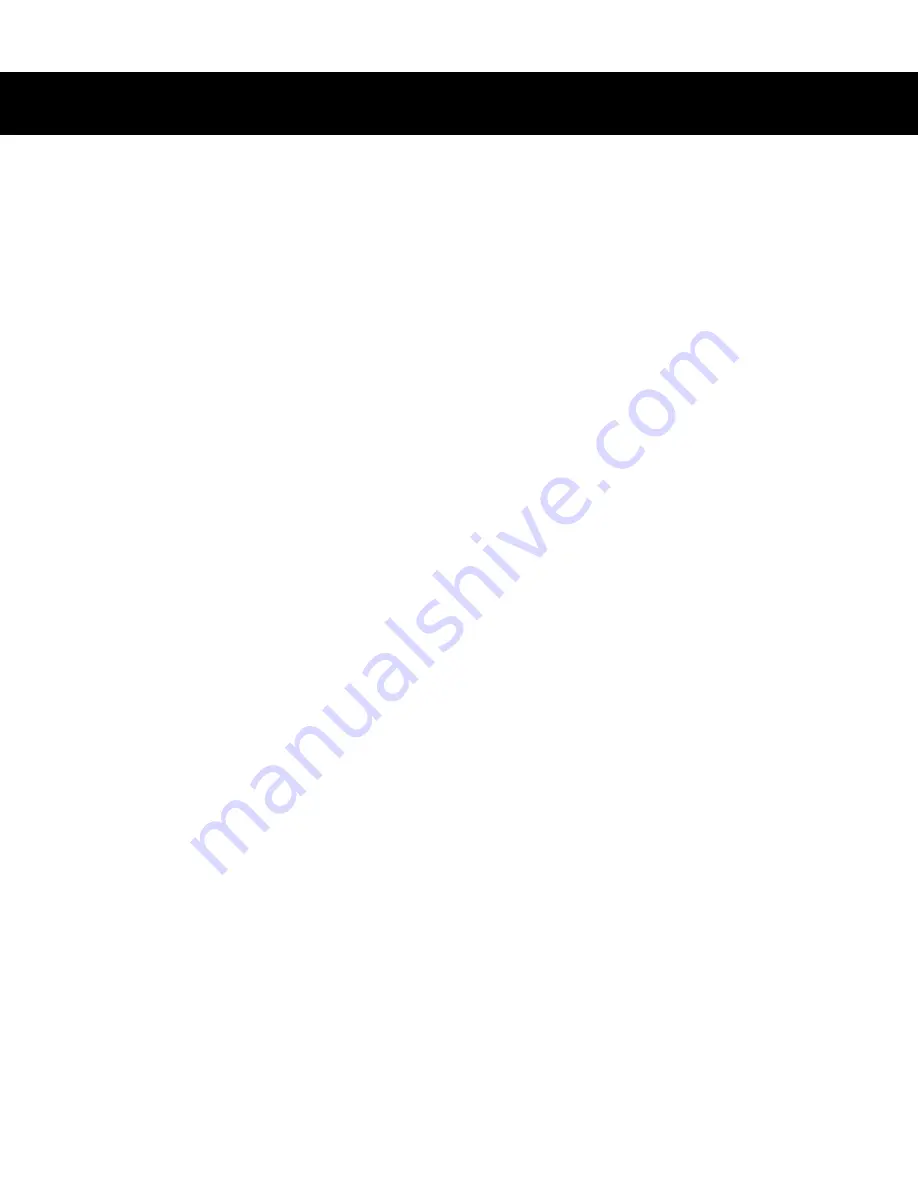
SERVICING THE BRAKE
1.
Evenly remove the two capscrews
(Item 9)
and four nuts
(Item 65)
holding the brake cover
(Item 20)
in place. Spring pressure will raise the cover as the capscrews are loosened. Remove
the cover from the brake housing.
2.
Remove the springs
(Item 24)
from the piston
(Item 10)
and check the free height. Each spring
should measure at least 1.200 inches with no force on them.
3.
Remove the brake piston
(Item 10)
by installing two pieces of 3/8"-16NC all-thread in the
bottom of two spring pockets. Using jam nuts, screw the all-thread pieces in evenly until the
piston is clear of the housing. An alternate way of removing the piston is to use a portable
power unit or shop air to slowly pressurize the brake cavity until the piston is out of the bore.
4.
Remove the brake driver/clutch assembly
(Items 13, 14, 15, 17, 34, and 38)
from the brake
housing
(Item 21)
.
5.
Remove the stator plates
(Item 19)
and friction discs
(Item 18)
from the brake housing and
check them for excessive wear, then replace if necessary. Additionally, check the top stator
plate for scoring caused by the removal tools and polish if necessary. Friction discs should
measure no less than 0.055 inches thick and stator plates should measure no less than 0.064
inches thick.
6.
If necessary, remove the seal
(Item 7-9)
from the brake housing by first removing the retaining
ring
(Item 72)
.
7.
If the brake housing
(Item 21)
is removed from the hoist, examine the journal on the brake
housing where the seal
(Item 7-8)
runs for wear. If severely worn, replace the brake housing.
8.
Carefully disassemble the brake driver/clutch and note the side in which the markings on the
clutch
(Item 34)
are facing
.
The clutch assembly must be re-assembled with the markings
facing the proper direction in order for the hoist to function properly. Inspect the surface on the
input and brake drivers
(Items 13 & 38)
where the clutch
(Item 34)
runs. If there is any pitting
or spalling on the drivers then both it and the clutch must be replaced.
9.
Re-assemble the driver/clutch assembly, making sure that the clutch is installed properly.
10.
Install a new seal
(Item 7-9)
into the brake housing. If the brake housing is removed from the
hoist, temporarily install the input sun gear
(Item 8)
into the brake housing and slide the
driver/clutch assembly onto the sun gear spline.
11.
Install the stator plates
(Item 19)
and friction discs
(Item 18)
into the brake housing starting
with a stator and alternating friction discs and stator plates. There is one more stator plate than
friction disc so you will finish with a stator plate.
12.
Coat the new o-rings and backup rings
(Items 7-1, 7-5, 7-6, & 7-7)
with light oil and install onto
the piston
(Item 10)
.
See Fig. 5 for proper o-ring/backup ring installation
.
13.
Carefully install the piston
(Item 10)
into the brake housing
(Item 21)
and gently tap it down
until it is seated.
11
Содержание TWG TULSA WINCH 506W
Страница 4: ...HYDRAULIC SCHEMATIC 4 ...