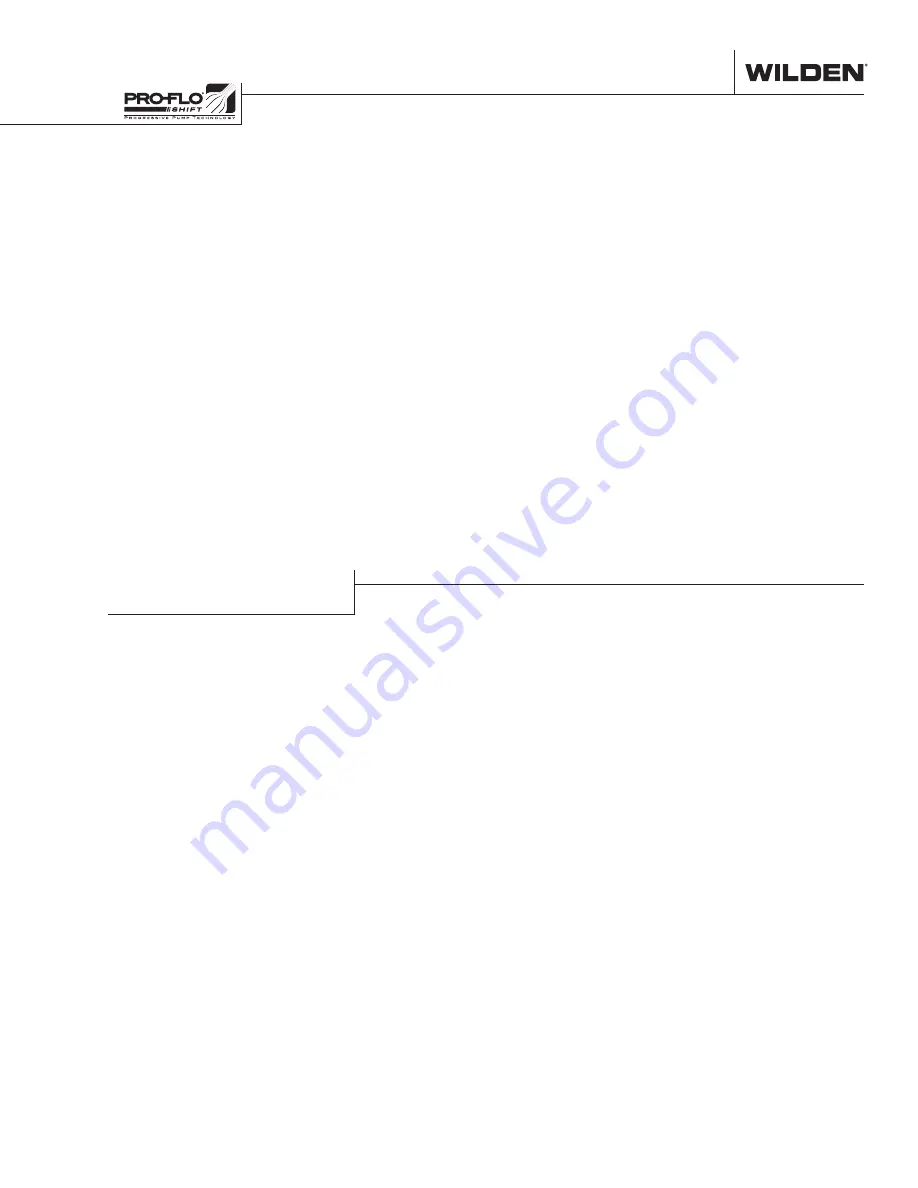
WIL-11520-E-07
13
WILDEN PUMP & ENGINEERING, LLC
T R O U B L E S H O O T I N G
OPERATION: The Pro-Flo
®
SHIFT pumps are pre-
lubricated and do not require in-line lubrication.
Additional lubrication will not damage the pump;
however if the pump is heavily lubricated by an
external source, the pump’s internal lubrication may
be washed away. If the pump is then moved to a non-
lubricated location, it may need to be disassembled
and re-lubricated as described in the DISASSEMBLY/
REASSEMBLY INSTRUCTIONS.
Pump discharge rate can be controlled by limiting
the volume and/or pressure of the air supply to the
pump. An air regulator is used to regulate air pressure.
A needle valve is used to regulate volume. Pump
discharge rate can also be controlled by throttling
the pump discharge by partially closing a valve in
the discharge line of the pump. This action increases
friction loss which reduces flow rate. (See Section
5.) This is useful when the need exists to control
the pump from a remote location. When the pump
discharge pressure equals or exceeds the air supply
pressure, the pump will stop; no bypass or pressure
relief valve is needed, and pump damage will not
occur. The pump has reached a “deadhead” situation
and can be restarted by reducing the fluid discharge
pressure or increasing the air inlet pressure. Wilden
Pro-Flo
®
SHIFT pumps run solely on compressed air
and do not generate heat; therefore, your process fluid
temperature will not be affected.
MAINTENANCE AND INSPECTIONS:
Since each
application is unique, maintenance schedules may
be different for every pump. Frequency of use, line
pressure, viscosity and abrasiveness of process fluid
all affect the parts life of a Wilden pump. Periodic
inspections have been found to offer the best
means for preventing unscheduled pump downtime.
Personnel familiar with the pump’s construction and
service should be informed of any abnormalities that
are detected during operation.
RECORDS: When service is required, a record should
be made of all necessary repairs and replacements.
Over a period of time, such records can become a
valuable tool for predicting and preventing future
maintenance problems and unscheduled downtime. In
addition, accurate records make it possible to identify
pumps that are poorly suited to their applications.
Pump will not run or runs slowly.
1. Ensure that the air inlet pressure is at least 0.4 bar
(5 psig) above startup pressure and that the differential
pressure (the difference between air inlet and liquid
discharge pressures) is not less than 0.7 bar (10 psig).
2. Check air inlet filter for debris (see SUGGESTED
INSTALLATION).
3. Check for extreme air leakage (blow by) that would
indicate worn seals/bores in the air valve, pilot
spool and main shaft.
4. Disassemble pump and check for obstructions in
the air passageways or objects that would obstruct
the movement of internal parts.
5. Check for sticking ball check valves. If material being
pumped is not compatible with pump elastomers,
swelling may occur. Replace ball check valves and
seals with proper elastomers. Also, as the check
valve balls wear out, they become smaller and can
become stuck in the seats. In this case, replace balls
and seats.
6. Check for broken inner pistons that would cause the
air valve spool to be unable to shift.
7. Remove plug from pilot spool exhaust.
Pump runs but little or no product flows.
1. Check for pump cavitation; slow pump speed down
to allow thick material to flow into liquid chambers.
2. Verify that vacuum required to lift liquid is not
greater than the vapor pressure of the material
being pumped (cavitation).
3. Check for sticking ball check valves. If material being
pumped is not compatible with pump elastomers,
swelling may occur. Replace ball check valves and
seats with proper elastomers. Also, as the check
valve balls wear out, they become smaller and can
become stuck in the seats. In this case, replace balls
and seats.
Pump air valve freezes.
1.
Check for excessive moisture in compressed
air. Either install a dryer or hot air generator for
compressed air. Alternatively, a coalescing filter
may be used to remove the water from the
compressed air in some applications.
Air bubbles in pump discharge.
1. Check for ruptured diaphragm.
2. Check tightness of outer pistons (refer to Section 7).
3.
Check tightness of fasteners and integrity of
O-rings and seals, especially at intake manifold.
4. Ensure pipe connections are airtight.
Product comes out air exhaust.
1. Check for diaphragm rupture.
2. Check tightness of outer pistons to shaft.
S U G G E S T E D O P E R A T I O N & M A I N T E N A N C E
Содержание PSG Wilden PS1520
Страница 29: ...N O T E S ...
Страница 30: ...N O T E S ...