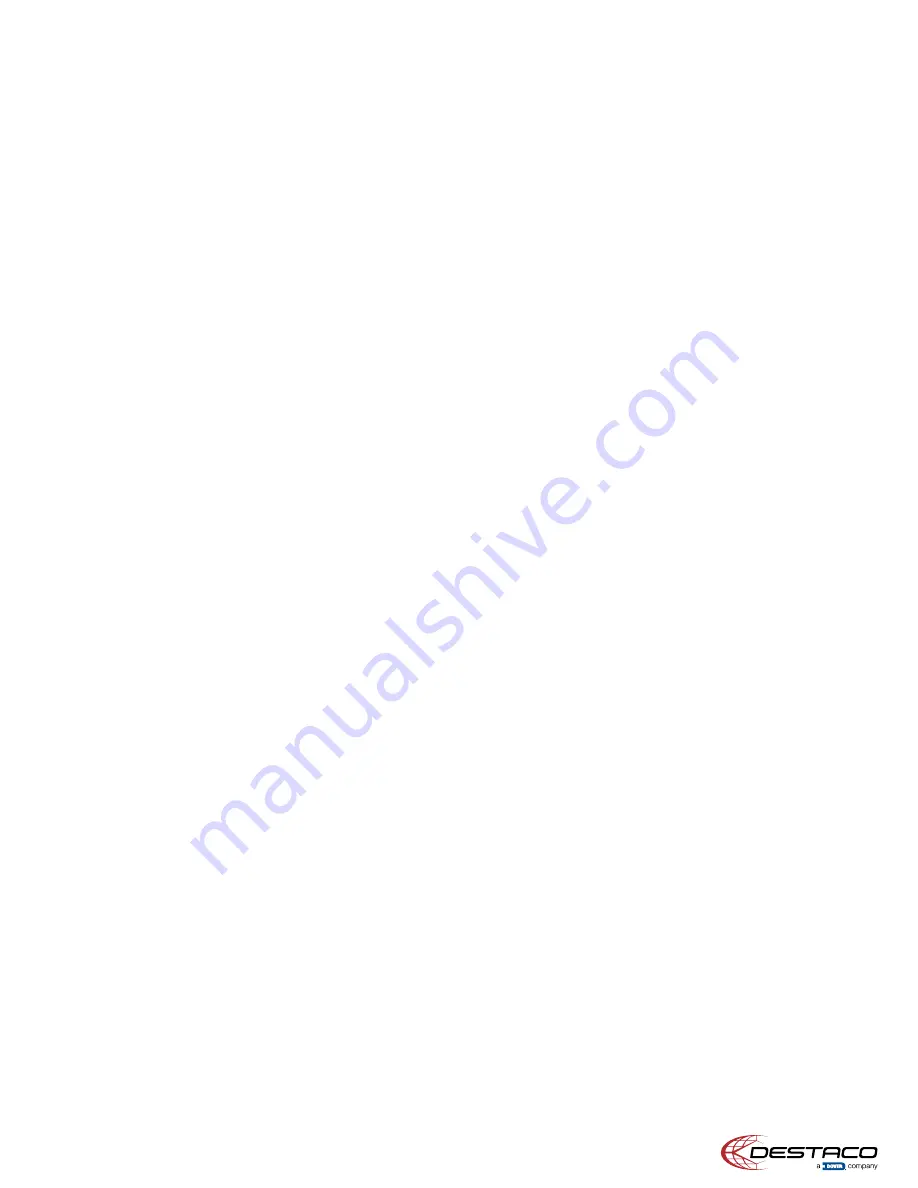
GTB Series
7
Dimensions and technical information are subject to change without notice
Servo Positioner Rotary Table | Instructions for Use
2. Instructions for Use
1. Purpose of the document
The operating manual is intended to help the user familiarize himself with the unit and its intended
application possibilities. The operating manual contains important information on the safe, proper operation
of the unit. Observation of this information will help avoid hazards, reduce repair costs and standstill times
and increase the reliability and service life of the unit.
Notes on precautionary measures to be taken by the unit owner:
• Employ only personnel with the necessary qualification to operate the unit.
• Define clear responsibilities and authorities for the operating and maintenance personnel.
• Supplement the operating manual with rules derived from the national occupational health and safety and
environmental protection regulations (e.g. work organisation).
• Instruct the personnel to observe the operating manual and its additions, and check compliance from time
to time. Have one copy of the operating manual available at the place of operation of the unit always!
• Operate the unit only when it is in a technically safe condition, and take measures to maintain this safety.
In addition to the operating manual, the binding accident prevention regulations applicable in the country of
operation and at the place of work must also be observed. In addition, the acknowledged engineering rules for
safe and proper working must be observed.
2. Target Groups
The owner as superordinate legal entity is responsible for the intended use of the unit and for the training
and employment of the authorised persons. He lays down the binding competencies and authorities of the
authorised persons for his company.
According to the latest Machinery Directive, the operating personnel are the persons responsible for installation,
operation, set-up, maintenance, cleaning, repair or transport of machines.
A specialist is a person who, thanks to his technical training, know-how and experience, is able to assess
the assigned duties and to recognise potential hazards. Furthermore, this person has know-how of the
applicable regulations. Only qualified specialists or such persons considered by the owner to be capable
are to be employed.
Trained/instructed persons are persons who have been instructed and possibly trained in the assigned duty
and in the potential dangers associated with improper behavior. The person has also been instructed about the
necessary protective devices and safety measures. Persons undergoing training, instruction or familiarization and
persons undergoing general training may only work under the constant supervision of an experienced person.
3. Liability and warranty
All information and tips given in this operating manual are given to the best of our knowledge and
belief and based on our experience and findings to date. The original version of this operating manual was
drawn up in English and was examined technically by us. The translation in the respective national/contract
language was produced by an acknowledged translation agency.
This operating manual was compiled with the greatest care. Should you discover any gaps and/or errors,
however, please inform us accordingly in writing. Your suggestions for improvements will help us in producing
a user-friendly operating manual.
4. Recorders and Copyright
Further copies of this operating manual can be ordered from the address shown under “Identification” in
chapter 1. Please note that further copies are subject to payment.
All rights are expressly reserved. Duplication or notification to third parties in whatever form is not permitted
without our written approval.