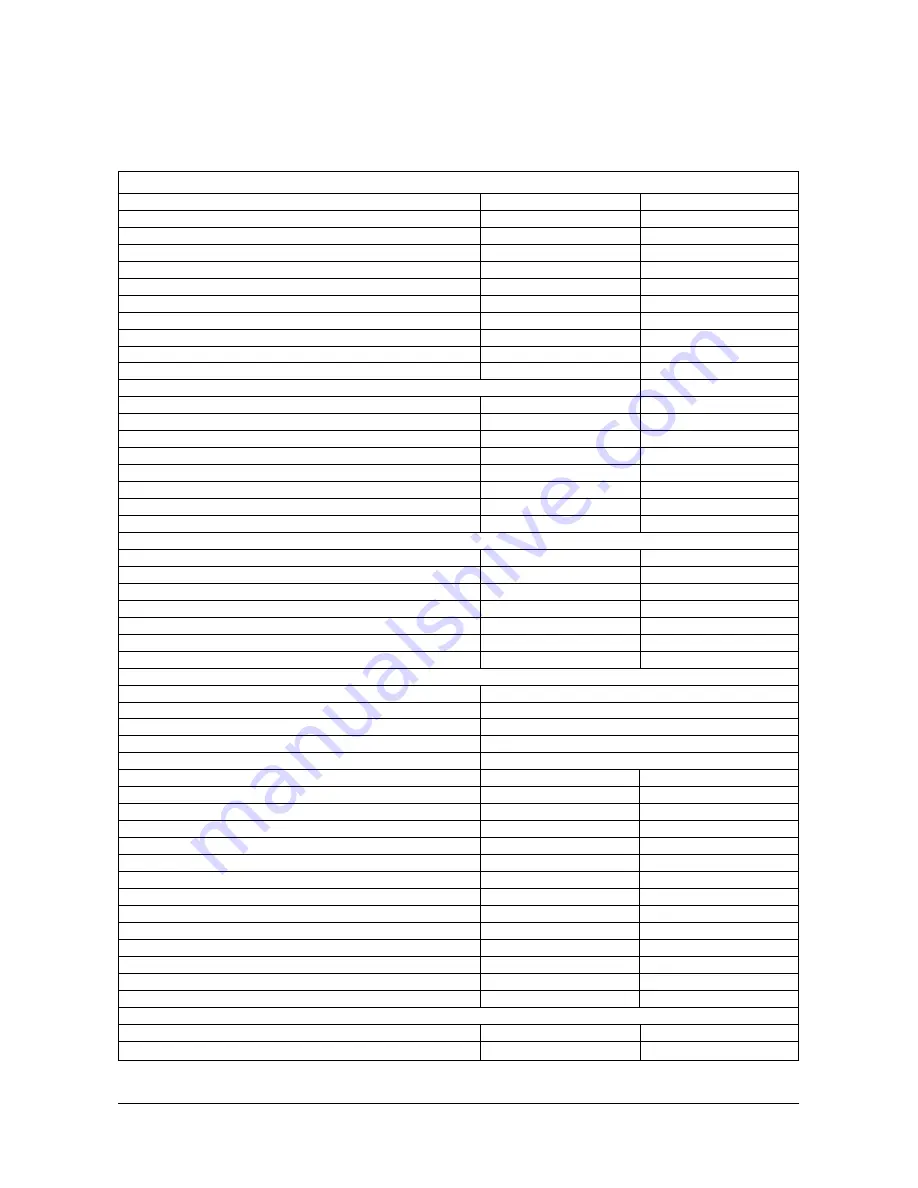
- 19 -
LP Engine G430 (3.0L)
Specifications
Engine Mechanical Specifications (2 of 2)
Crankshaft
Crankshaft Journal Diameter (All)
Crankshaft Journal Taper Production
Crankshaft Journal Taper Service Limit
Crankshaft Journal Out-of-Round Production
Crankshaft Journal Out-of-Round Service Limit
Crankshaft Bearing Clearance Production #1-#4
Crankshaft Bearing Clearance Production #5
Crankshaft Bearing Clearance Service Limit #1-#4
Crankshaft Bearing Clearance Service Limit #5
Crankshaft End Play
Crankshaft Sprocket Runout
Connecting Rod
Connecting Rod Journal Diameter
Connecting Rod Journal Taper Production
Connecting Rod Journal Taper Service Limit
Connecting Rod Journal Out-of-Round Production
Connecting Rod Journal Out-of-Round Service Limit
Rod Bearing Clearance Production
Rod Bearing Clearance Service Limit
Rod Side Clearance
Camshaft
Journal diameter
End Play
Camshaft Sprocket Runout
Timing Sprocket Teeth Backlash
Lobe Lift Intake
Lobe Lift Exhaust
Lobe Lift Service Limit
Valve System
Valve Lifter
Hydraulic
Valve Rocker Arm Ratio
1.75:1
Valve Lash
Half to One Turn Down From Zero Lash
Face Angle
45 Degrees
Seat Angle
46 Degrees
Seat Runout
Seat Width Intake
Seat Width Exhaust
Stem Clearance Intake Production
Stem Clearance Exhaust Production
Stem Clearance Intake Service Limit
Stem Clearance Exhaust Service Limit
Valve Spring Free Length
Valve Spring Pressure Closed
Valve Spring Pressure Open
Valve Spring Installed Height Intake
Valve Spring Installed Height Exhaust
Valve Lift Intake
Valve Lift Exhaust
Cylinder Head Warpage
Cylinder Head Deck (measured within a 152.4 mm (6.0 in) area)
Cylinder Head Deck (measuring the overall length of the cylinder head)
58.3666-58.4047 mm
0.005 mm (Maximum)
0.0254 mm (Maximum)
0.005 mm (Maximum)
0.0254 mm (Maximum)
0.0254-0.06096 mm
0.0406-0.0889 mm
0.0254-0.0635 mm
0.0381-0.0889 mm
0.05-0.1524 mm
0.07 mm (Maximum)
53.2892-53.3273 mm
0.00762 mm (Maximum)
0.0254 mm (Maximum)
0.005 mm (Maximum)
0.0254 mm (Maximum)
0.04318-0.06858 mm
0.0762 mm (Maximum)
0.1524-0.4318 mm
47.440-47.490 mm
0.0762-0.2032 mm
0.1 mm (Maximum)
0.10-0.15 mm
6.4247 mm
6.4247 mm
L
0.0254 mm
0.05 mm (Maximum)
1.27-1.778 mm
1.524-2.032 mm
0.0254-0.06858 mm
0.01778-0.06858 mm
0.09398 mm (Maximum)
0.1193 mm (Maximum)
52.324 mm
444-490 N at 40.89 mm
925-987 N at 30.99 mm
41.91 mm
41.91 mm
11.25 mm
11.25 mm
0.0762 mm
0.1778 mm
2.2979-2.2994 in
0.0002 in (Maximum)
0.001 in (Maximum)
0.0002 in (Maximum)
0.001 in (Maximum)
0.001-0.0024 in
0.0016-0.0035 in
0.001-0.0025 in
0.0015-0.0035 in
0.002-0.006 in
0.003 in (Maximum)
2.0980-2.0995 in
0.0003 in (Maximum)
0.001 in (Maximum)
0.0002 in (Maximum)
0.001 in (Maximum)
0.0017-0.0027 in
0.003 in (Maximum)
0.006-0.017 in
1.8677-1.8697 in
0.003-0.008 in
0.004 in (Maximum)
0.004-0.006 in
0.25294
0.25294
L
0.001 in
0.002 in (Maximum)
0.050-0.070 in
0.060-0.080 in
0.001-0.0027 in
0.0007-0.0027 in
0.0037 in (Maximum)
0.0047 in (Maximum)
2.06 in
100-110 lb at 1.61 in
208-222 lb at 1.22 in
1.65 in
1.65 in
0.443 in
0.443 in
0.003 in
0.007 in