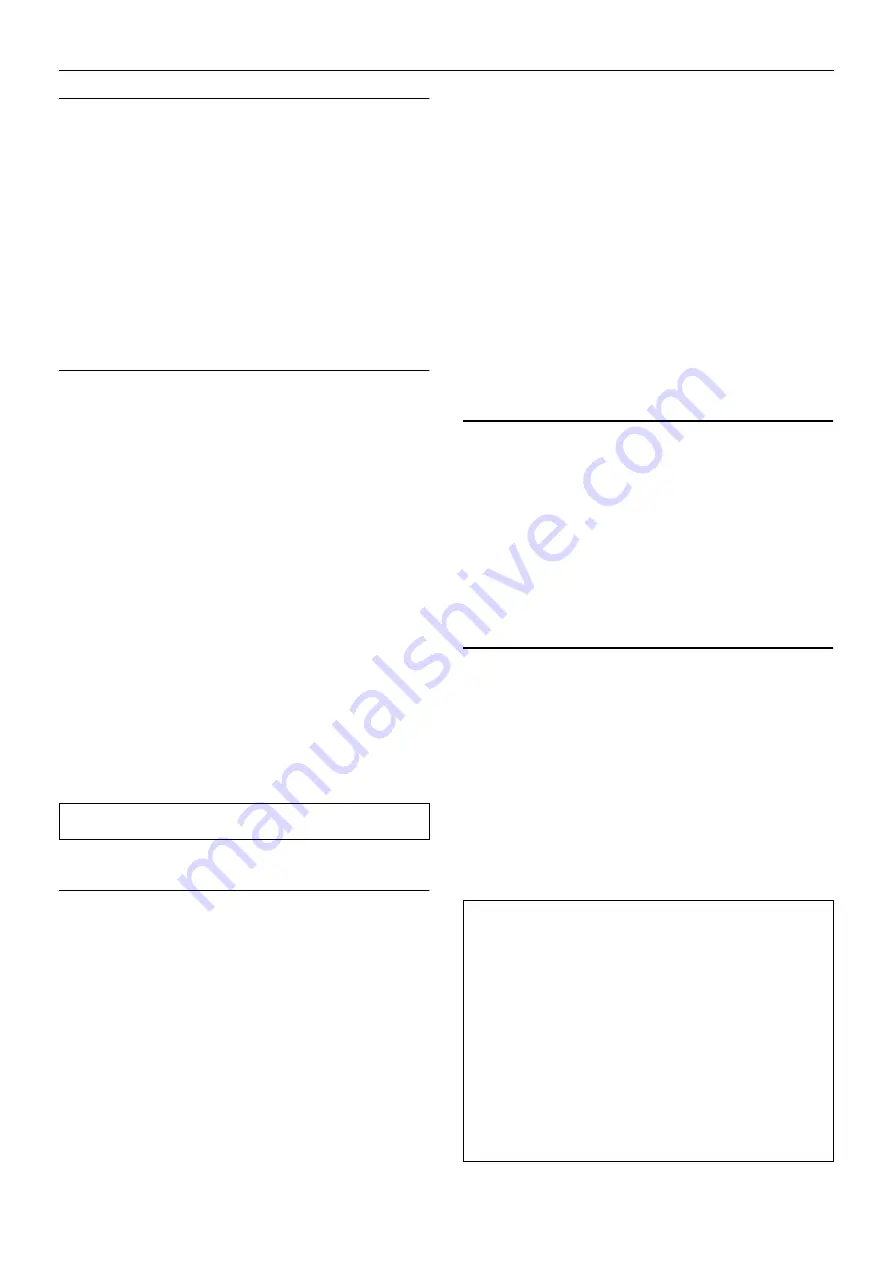
OPERATING INSTRUCTIONS
57
12/154
DECOMMISSIONING
When the machine is to be permanently decommissioned or
dismantled, it is important to ensure that all hazard risks are either
eliminated or notified to the recipient of the machine. In particular:-
•
Do not destroy batteries or components containing asbestos
without containing the materials safely.
•
Do not dispose of any pressure vessel that is not clearly marked
with its relevant data plate information or rendered unusable by drilling,
cutting etc.
•
Do not allow lubricants or coolants to be released into land surfaces
or drains.
•
Do not dispose of a complete machine without documentation
relating to instructions for its use.
BUNDED BASE
Description
This machine is fitted with bund equipment to contain leakages and
spillages, which occur within the machine enclosure.
The bund will contain all fluids normally installed in the machine, plus
an additional 10%, when operated within 3 degrees of level.
Drains for engine water & oil and compressor oil are located at the front
corner of the machine
The rear air intake is covered to prevent rainwater ingress. Ensure that
the cover is not prevented from moving.
Draining of contaminated fluids
Contaminated fluid must be removed by authorized personnel only.
Captured fluids can be drained from the bund by uncoupling the flexible
pipe secured at the rear / side. This pipe must be re-secured after
draining.
Drainage of machine fluids
During maintenance operations drain machine fluids using the drain
ports indicated.
When cleaning of the fuel tank is needed, tank should be removed from
compressor.
Captured fluids can be drained from the bund by uncoupling the
flexible pipe secured at the rear / side. This pipe must be re-secured
after draining.
LONG TERM STORAGE RECOMMENDATIONS
(6 months or more)
Spare Airends
•
Long-term storage of airends should include filling the airend with
the standard compressor fluid, PRO-TEC, XHP605 or XHP405. Upon
installation of the airend, drain the storage oil from the airend and
proceed with the installation, assuring fresh oil is poured into the intake
prior to start up.
Portable Compressors
•
Airend – Remove the intake connection and fill the airend intake
with Doosan compressor fluid PRO-TEC, XHP605 or XHP405.
Reconnect the intake connection.
•
Engine cooling system – Treat with rust inhibitor and drain. Check
with engine dealer for further recommendations.
•
Compressor Oil Filter/s- fill with Doosan compressor fluid PRO-
TEC, XHP605 or XHP405.
•
Seal all opening with waterproof tape
•
Place a desiccant in the exhaust pipes, engine and compressor air
intake pipes.
•
Loosen tension on belts, fan, airend, etc.
•
Block axles so tyres are off ground and do not support any weight.
•
Disconnect battery cables.
•
Drain the fuel system.
SHORT TERM STORAGE
Machines that stand idle for extended periods of time greater than
30 days:
•
Be started and operated every 30 days. Operate long enough to
allow the engine and compressor to reach operating temperature.
•
Open and close the service valve to exercise machine from full load
to idle RPM.
•
Drain fuel tank to remove any water.
•
Drain water from fuel water separator.
•
Remove batteries and connect to trickle charger.
COMPRESSOR MOUNTING
Portable compressors, which are modified to remove the running
gear and mount the compressor directly to trailers, truck beds or
frames, etc. may experience failure of the enclosure, frame, and/or
other components.
It is necessary to isolate the compressor package from the carrier
base with a flexible mounting system. Such a system must also prevent
detachment of the package from the carrier base in the event the
isolators fail.
Contact your Portable Power representative for flexible mounting
kits.
Warranty does not cover failures attributable to mounting of the
compressor package to the carrier base unless it is a Portable Power
provided system.
WARNING: Major leakages or spillages must be drained before
the machine is towed.
NOTE:
The maintenance schedule in this manual describes the
service intervals that should be followed for “normal” applications of
this compressor. This page may be reproduced and used as a
checklist by service personnel.
In more severe applications such as but not limited to sandblasting,
quarry drilling, well drilling, and oil and gas drilling, more frequent
service intervals and/or the installment of a heavy duty air filtration
system will be required to ensure long component life.
Dust and dirt, high humidity, and high temperatures will affect
lubricant life and service intervals for components such as inlet air
filters, oil separation elements and oil filters.
Should you require assistance in determining the effect your
application may have on compressor performance, we suggest you
contact your Doosan dealer.
Содержание 12/154
Страница 2: ......
Страница 4: ......
Страница 84: ...80 MACHINE SYSTEMS 12 154 page ...
Страница 86: ...82 MACHINE SYSTEMS 12 154 ...
Страница 88: ...84 MACHINE SYSTEMS 12 154 ...
Страница 90: ...86 MACHINE SYSTEMS 12 154 ...
Страница 92: ...88 MACHINE SYSTEMS 12 154 ...
Страница 94: ...90 MACHINE SYSTEMS 12 154 ...
Страница 101: ...OPTIONS 97 12 154 PRIMARY AND SECONDARY FILTER MAINTENANCE FIGURE 1 FIGURE 2 FIGURE 3 FIGURE 4 FIGURE 5 ...
Страница 102: ...98 OPTIONS 12 154 WATER SEPARATOR MAINTENANCE FIGURE 1 FIGURE 2 FIGURE 3 FIGURE 4 FIGURE 5 FIGURE 6 ...
Страница 108: ......