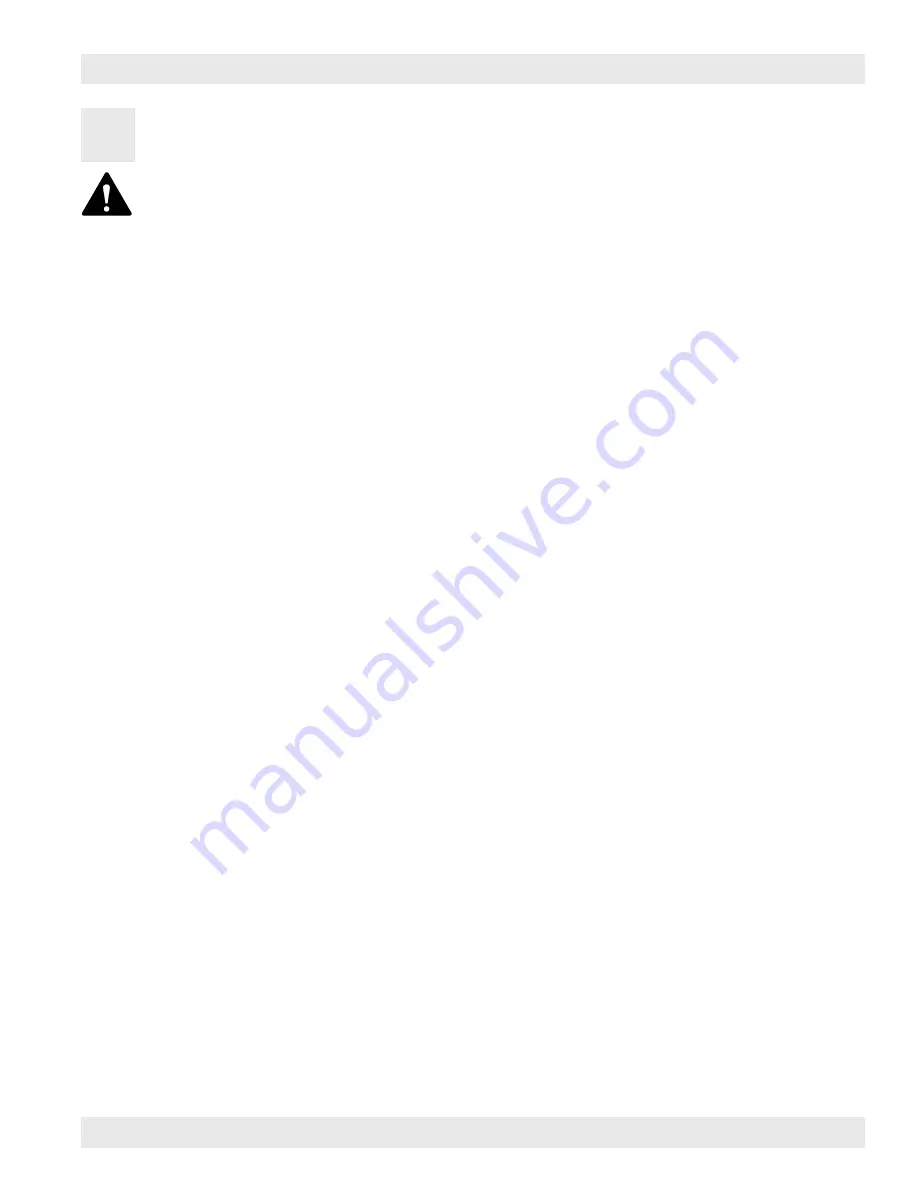
8
LP Panelized Baghouse 684LP - 882LP
During any service activities there is some potential for exposure to the dust in the collector. Most dusts present
safety and health hazards that require precautions. Wear eye, respiratory, head, and other protection equipment
suitable for the type of dust when performing any service activities.
Use appropriate access equipment and procedures. Note the standard collector is not equipped with access
platforms unless noted on the specification drawing.
LOCK-OUT all energy sources prior to performing any service or maintenance on the equipment.
Electrical service or maintenance work must be performed by a qualified electrician and comply with all applicable
national and local codes.
Donaldson Torit filters require little maintenance in most applications. Bags require replacement on a periodic basis. The severity of
the application will dictate the time interval for bag replacement.
4
Product Service
1. Monitor the physical condition of the collector and repair or replace any damaged components.
Routine inspections will minimize downtime and maintain optimum system performance. This is particularly important on
continuous-duty applications.
2. Monitor pressure drop across filters.
Abnormal changes in pressure drop may indicate a change in operating conditions and possibly a fault to be corrected.
3. Monitor exhaust for any signs of material emissions/bypass.
4. Monitor dust disposal out of the hopper discharge opening.
Check the following items at the recommended intervals shown below.
Weekly
1. Check that pressure drop is within normal operational range.
Quarterly
1. Check/monitor drive chain tension and lubrication of upper and lower bearing.
2. Check reverse air cleaning fan wheel set screw and tighten if necessary.
3. Check reverse air cleaning fan wheel for excessive noise and/or vibration.
4.
Check condition of the clean-air plenum. If dust accumulation is present, check filter bags for damage or wear and replace as
necessary.
5.
Check the rotating arm drive gear reducer oil level. The gear reducer is filled with AGMA 8c or equivalent oil. See reducer
manual for more information.
Annual
1. Verify smooth operation of cleaning arm/skid.
2.
Monitor thickness of wear material on the cleaning skid, look for filter cages not fully inserted into tubesheet.
3. Check structural support for any signs of damage or wear and take appropriate steps to correct any problems.
4.
Inspect explosion vents, if applicable, for signs of damage or wear and replace as necessary.
5. Check door seals for signs of damage or wear and replace as necessary.