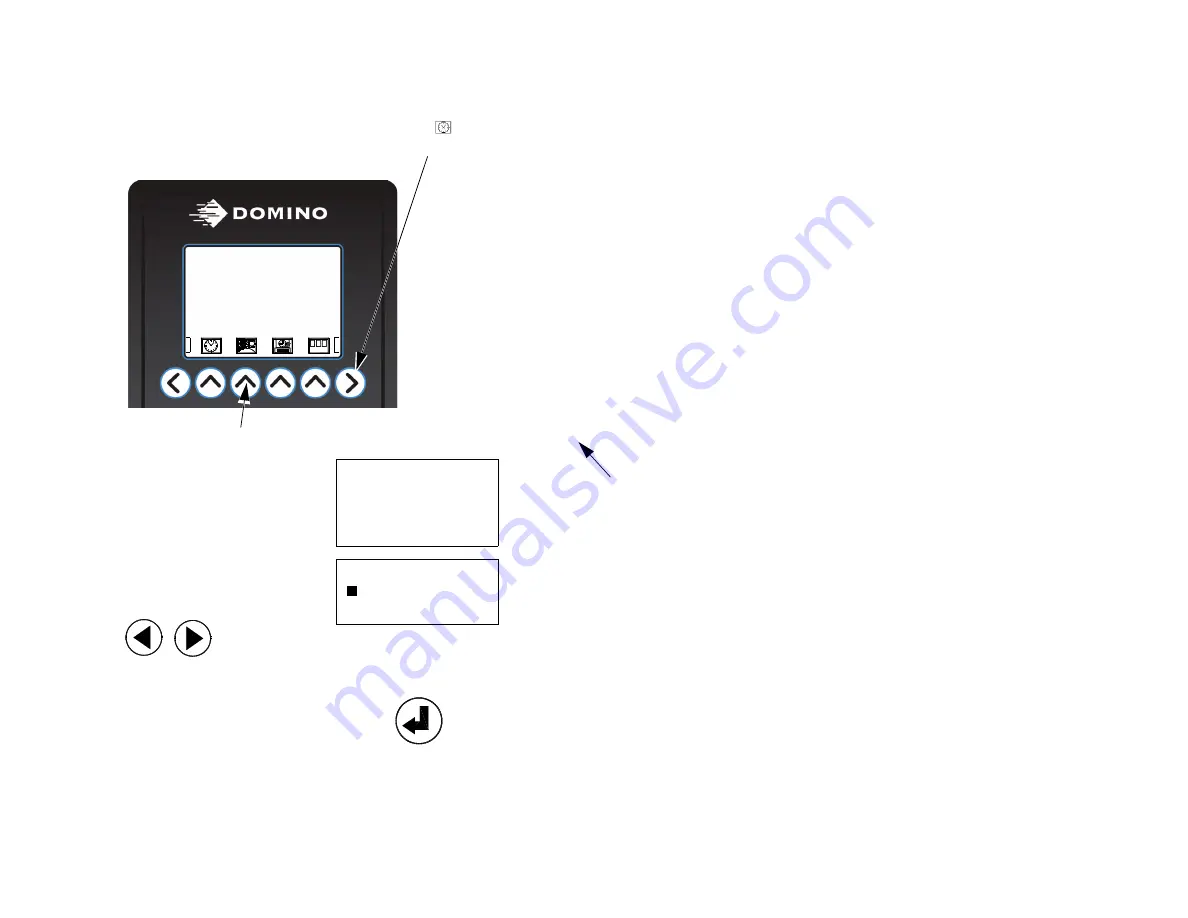
PROGRAMMING THE PRINTER
74
77144 Issue 8 August 2009
Amend the clock function, as follows:
(1) Scroll through the menu bar functions and select the
set clock
icon.
(2) The Clock Options submenu is displayed.
Select the time option by using the up down
cursor keys and press
enter
.
(3) A flashing cursor block at the beginning of
the hours format can be moved left or right
by pressing the cursor arrows on the key pad.
(4) To re-adjust any of the values, place the
cursor over the character to be adjusted and
overtype the new value, when all changes are
completed press
enter
.
Note:
Values that are outside the parameters of the 24 hour clock or calendar month,
are not accepted.
Press the corresponding key to select the function
PRINTING MESSAGE1
NORMAL PRINT
INK STATUS OK
Press right directional key until the menu bar starts to scroll
1 2 3
CLOCK OPTIONS
> FIRST WOY
TIME
HR:MI DT/MO/YR D
5 : 28 10/12/99 5
Flashing block cursor can scroll
across time/date/day format
enabling operator to edit the
clock time.
Содержание C1000 plus
Страница 1: ...C Seriesplus Printer Operation and Maintenance Manual ...
Страница 2: ...2 77144 Issue 8 August 2009 THIS PAGE INTENTIONALLY BLANK ...
Страница 12: ...INTRODUCTION 12 77144 Issue 8 August 2009 THIS PAGE INTENTIONALLY BLANK ...
Страница 17: ...BASIC OPERATIONS 77144 Issue 8 August 2009 17 2 Litre Base Unit ...
Страница 18: ...BASIC OPERATIONS 18 77144 Issue 8 August 2009 200ml Base Unit ...
Страница 24: ...BASIC OPERATIONS 24 77144 Issue 8 August 2009 Conveyor ...
Страница 62: ...BASIC OPERATIONS 62 77144 Issue 8 August 2009 THIS PAGE INTENTIONALLY BLANK ...
Страница 64: ...BASIC OPERATIONS 64 77144 Issue 8 August 2009 THIS PAGE INTENTIONALLY BLANK ...
Страница 141: ...DIMENSION DRAWINGS 77144 Issue 8 August 2009 141 Base Unit Length 507 0 20 0 139 0 5 5 412 8 16 25 2L Base ...
Страница 145: ...DIMENSION DRAWINGS 77144 Issue 8 August 2009 145 Base Unit Width 162 0 6 37 200ml Base Unit ...
Страница 147: ...DIMENSION DRAWINGS 77144 Issue 8 August 2009 147 C6000 MF ...
Страница 148: ...DIMENSION DRAWINGS 148 77144 Issue 8 August 2009 C6000 MF ...
Страница 149: ...DIMENSION DRAWINGS 77144 Issue 8 August 2009 149 C6000i ...
Страница 150: ...DIMENSION DRAWINGS 150 77144 Issue 8 August 2009 C6000i ...
Страница 151: ...DIMENSION DRAWINGS 77144 Issue 8 August 2009 151 C3000 ...
Страница 152: ...DIMENSION DRAWINGS 152 77144 Issue 8 August 2009 C3000 ...
Страница 153: ...DIMENSION DRAWINGS 77144 Issue 8 August 2009 153 C3000X ...
Страница 154: ...DIMENSION DRAWINGS 154 77144 Issue 8 August 2009 C3000X ...
Страница 155: ...DIMENSION DRAWINGS 77144 Issue 8 August 2009 155 C1000 ...
Страница 156: ...DIMENSION DRAWINGS 156 77144 Issue 8 August 2009 C1000 ...
Страница 158: ...DIMENSION DRAWINGS 158 77144 Issue 8 August 2009 C1000X ...
Страница 165: ...OPERATOR NOTES 77144 Issue 8 August 2009 165 ...
Страница 166: ...166 77144 Issue 8 August 2009 ...
Страница 170: ...THIS PAGE INTENTIONALLY BLANK ...